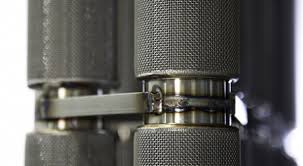
Metal filters are critical to improving process and environmental quality. Unfortunately in doing their job, filters can corrode or capture particulates and eventually clog and foul.*
Corrosion and fouling can disrupt process fluid flow and cause process shutdowns, in this blog post we'll discuss how to make metal filters last longer by reducing fouling and improving filter performance and corrosion resistance.
In this blog post you will learn:
- How silicon CVD coatings can change the surface energy, corrosion resistance, lubricity and fouling properties of a surface.
- How coatings like Dursan and Notak can reduce filtration differential pressure and prevent metal filter fouling.
- How anti fouling coatings can extend the life of metal filters and prevent membrane fouling.
|
Metal filter corrosion and fouling can increase maintenance, reduce efficiency and contaminate product flow paths. Additionally metal fritted filters commonly used in analytical and lab applications adsorb reactive flow path samples, causing test failures and inconsistent test results. That's why it's important to protect metal filters while they protect your process.
Improved filter performance can be achieved by several means:
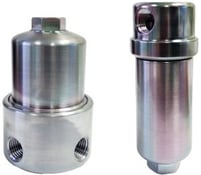
- Changing the filter design or size.
- Installing a purge/recharge system to reduce fouling and obstruction.
- Changing the filter material to improve corrosion resistance.
- Changing the surface energy/hydrophobicity of the surface
Coatings are rarely considered when looking for options to improve performance and durability. That's because coatings can foul filters and increase filter back pressure which will end up causing more problems. But precision coatings applied by chemical vapor deposition (CVD) should be considered when evaluating options for corrosion and fouling resistance. That's because high temperature CVD coatings prevent the interaction of process fluids and test analytes with the metal filter surface, reducing fouling, corrosion, contamination, and sample adsorption. They also won't significantly obstruct the filter while penetrating the filter media and coating within the pore or fiber media.
The CVD process distributes a coating without blinding the filter surface or significantly impacting filter efficiency. A cross section of a precision coated filter (below) shows coating throughout the filter without blocking the pores.
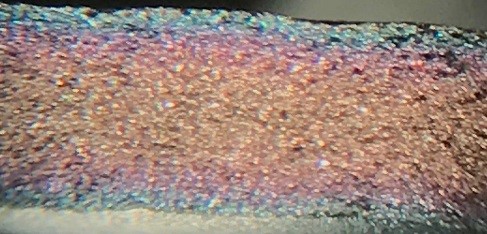
Want to learn more about how we coat metal filters and sintered metal frits? Read our Technical Insight.
How silicon coatings change the surface properties of metal filters.
CVD coatings like Dursan® and Notak™ are bonded to the surface of metal filters by a patented chemical vapor deposition process. The coating gas penetrates the filter and creates a micro thin barrier coating throughout the filter area. Even sintered metal frits can be treated. The barrier coating bonds and penetrates into the surface creating a corrosion resistant, fouling resistant surface with high lubricity. The sputter depth profile below highlights the silicon steel diffusion zone and bond to the stainless steel filter surface. See how Dursan can solve your material problem.
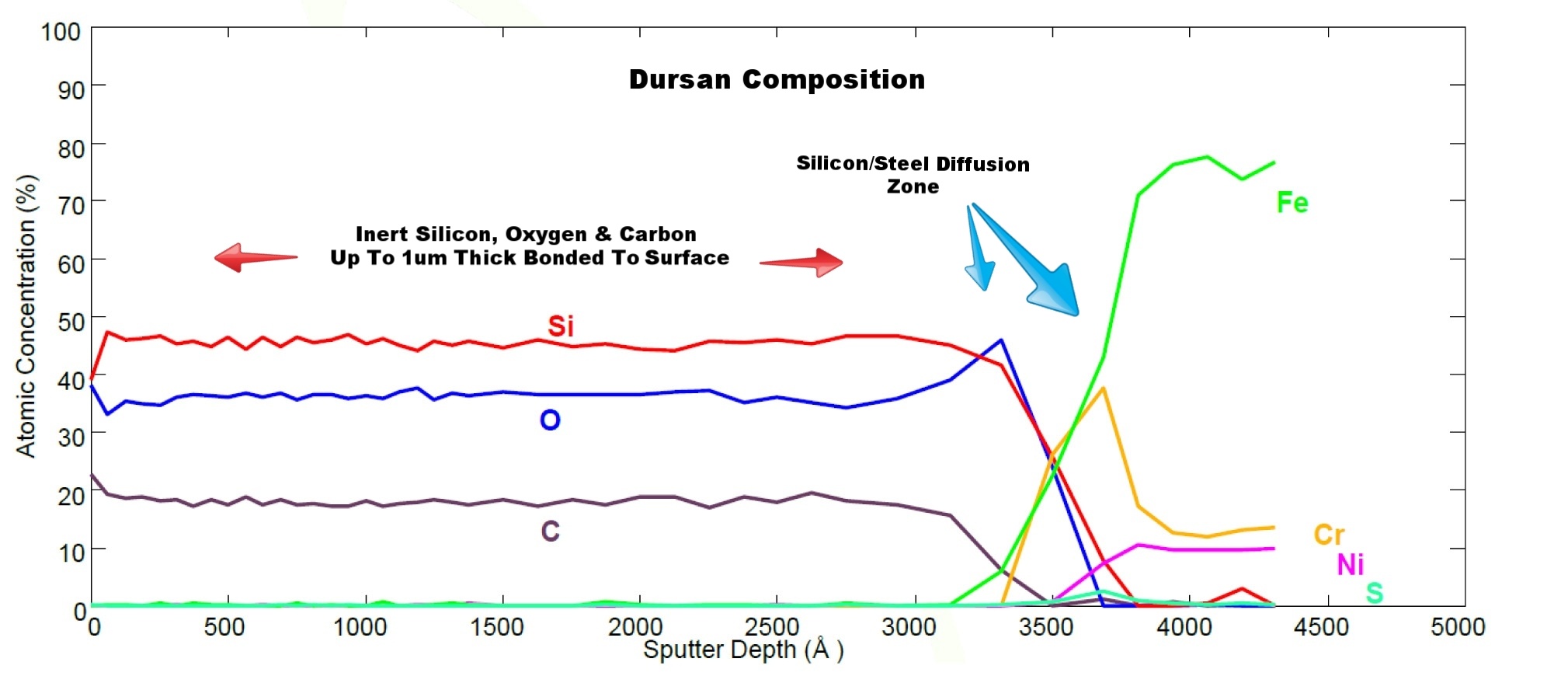
After processing, the filter will take on the surface properties of the coating, enhancing the corrosion resistance, fouling resistance, lubricity, surface energy/ hydrophobicity of the filter. Read more about how our coatings prevent fouling.
Wear and Friction Data
Pin-on-disc comparison of Dursan (carboxysilane) to an oxidized stainless steel surface shows a 50% reduction in wear rate and a 35% reduction in coefficient of friction, improving the efficiency and wear resistance of the filter. Read the complete study.
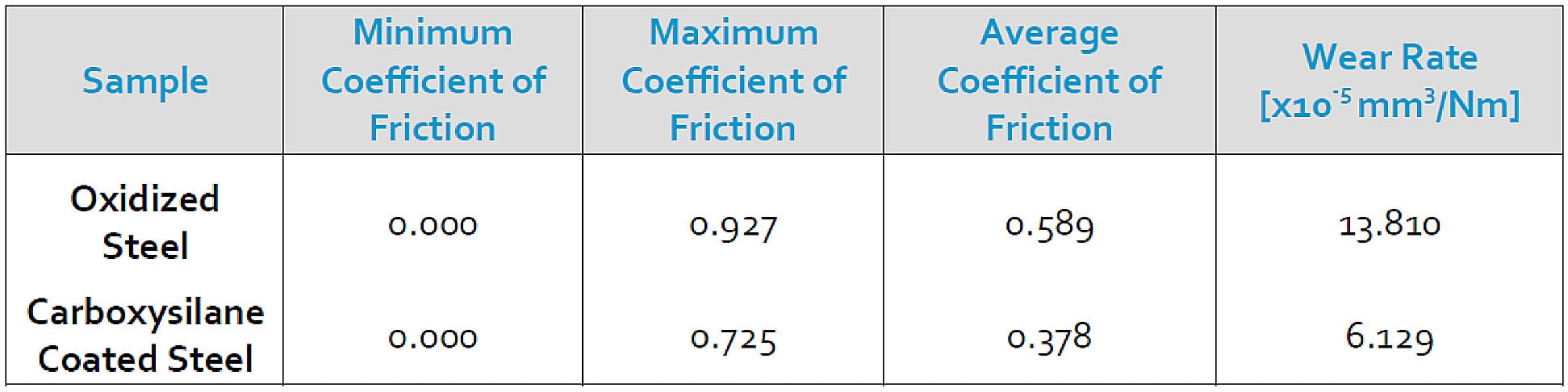
Carbon Coking Fouling Resistance
Coking and fouling studies show SilcoTek® coatings and coatings combined with a surfactant reduce fouling by 50% or more. Reducing the particulate binding effect and making the filter easier to clean.

Corrosion Resistance
ASTM G31 immersion testing compared a Dursan coated surface with silicon and uncoated stainless steel. The Dursan coated surface improved corrosion resistance by an order of magnitude, improving metal filter durability. Get our latest on corrosion prevention, get our corrosion presentation.
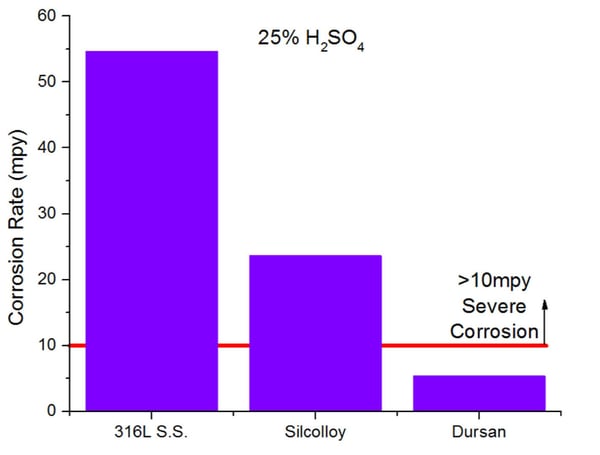
Surface Energy
A key to particulate binding and fouling is surface energy management. A low surface energy surface will reduce the particulate bond energy and make filter cleaning easier. Surfaces like Notak™ (F-Dursan in the graph) offer the lowest surface energy and highest contact angle of any silicon surface tested. The Notak surface reduces surface energy by 80% compared to stainless steel.
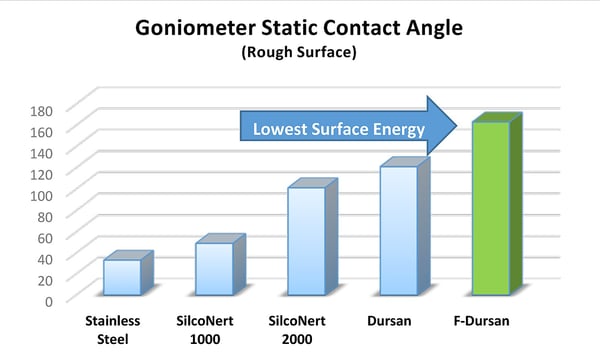
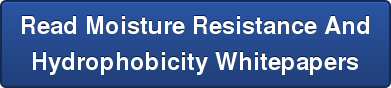
What's it all mean? How Does a Low Friction Low Surface Energy Surface Prevent Membrane Fouling?
So what will a low surface energy high lubricity filter surface contribute to fouling prevention and improved filter performance? Let's compare the differential pressure of an uncoated filter (graph below, top 2 lines) with a Dursan coated filter under simulated process conditions. The coated filter (lower line) had nearly twice the life and half the differential pressure of the uncoated filter.* That means that Dursan or other SilcoTek coatings can help extend the life of your metal filter while reducing energy loss and system back pressure.
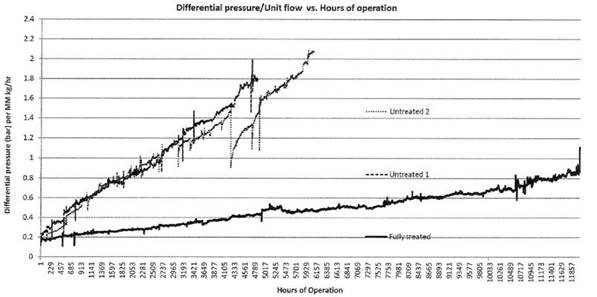
Interested in fouling resistance? Read our webinar presentation and learn about how our coatings reduce fouling in many applications.

*Image courtesy of Porvair Filtration.
Data from Porvair PCT/GB2016/053671