SilcoTek enhanced the aluminum CVD barrier coating process for better inertness and corrosion resistance.
Barrier Coatings for Aluminum Inertness and Corrosion Resistance
SilcoTek® refined the CVD barrier coating process to improve the inertness and corrosion resistance of aluminum substrates. In this blog we discuss our SP12 process and learn how this enhancement compares to our standard process on aluminum and other substrates.
In this blog post you will learn:
- How SilcoTek refined the silicon CVD coating process to improve coating performance on aluminum.
- How our refined process, called SP12, performs under corrosive conditions when compared to our standard coating process on aluminum.
- How the SP12 process improves the inertness performance of aluminum substrates.
|
Background: How We Coat Aluminum
Aluminum can be a difficult substrate for silicon to form an effective bond. The resulting coating can have at times a flat dark or blotchy appearance, not the customary bright rainbow appearance expected from our coating (as seen in the top photo of our blog post). More concerning, the performance of the coated surface may, for some aluminum substrates, be less effective when compared to our standard coating.
The R&D Team set out to study and understand the silicon-aluminum interface and to refine the coating process to match the performance of our standard coating process.

After extensive research, the R&D Team found that the aluminum substrate had a catalytic effect at the silicon-aluminum interface that promoted silicon nanowire growth. The Team then set out to develop a "primer" layer that minimized the catalytic effect. The characteristics of the resulting primer process include:
- Use a primer layer to isolate aluminum from the a-Si coating.
- Primer layer itself is immune to aluminum’s catalytical effect.
- Primer layer bonds well to both substrate and a-Si coating.
- Primer layer can be applied in the same CVD process to be production friendly.
SilcoTek® developed a proprietary process that meets the above requirements and can be implemented within our current process capabilities. The graphic below demonstrates how the primer layer acts as a barrier between the aluminum substrate and the silicon coating but enhances the performance of the CVD process when applied to aluminum substrates.
Standard Coating Aluminum Coating (SP12)
The results of the SP12 coating process showed comparable coating appearance to standard coated stainless steel. To verify the coating performance, the team tested uncoated aluminum, standard coated aluminum, and coated aluminum using the SP12 process. The team tested sample coupons for corrosion resistance and inertness.
Is SilcoNert® 2000 applied with the SP12 process different from SilcoNert applied to stainless steel?
Basically no. The SilcoNert applied to stainless steel is essentially the same surface as what's applied to aluminum. The SP12 process is not a replacement for SilcoNert but rather a process enhancement designed to enable the SilcoNert 2000 coating to be applied on a wider variety of substrate materials. The standard SilcoNert coating is still the default process for stainless steel substrates.
Inertness Testing
There are a wide range of uses for aluminum in analytical applications, unfortunately there aren't so many options to passivate the surface, especially passivation technologies that create a durable inert surface.
A silicon coated aluminum surface dramatically improves inertness and saves significant manufacturing cost and weight when compared to stainless steel coated products; especially in sample transport and field test applications. SP12 can be applied to other surfaces, like high porosity or oxidation prone surfaces, that may benefit from a primer coating technology. Let's review some examples of SilcoNert SP12 performance on various surfaces.
SilcoNert® SP12 Pesticide Analysis
Liner testing done by a customer showed comparable performance of SP12 applied SilcoNert 2000 to standard process SilcoNert 2000-coated borosilicate liners in trace level pesticide analysis. The test criteria is highlighted below:
- Test conditions: Endrin at 50 pg/µL and DDT at 100 pg/µL.
- Typical pass/fail criteria are below 10% breakdown rates, which are met by both coatings.
Test breakdown percentage graphs (below) for the SP12 process were comparable if not better than the standard application process for SilcoNert 2000.
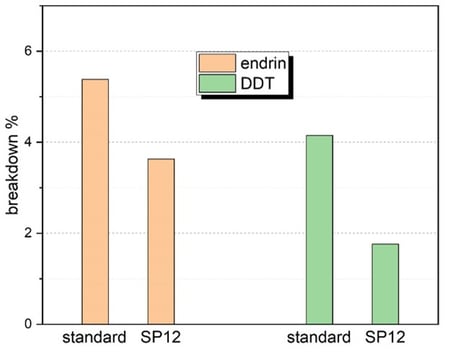
Additionally SP12-coated aluminum has shown good inertness properties in sulfur and ammonia analysis in customer applications. Inertness results are comparable to standard process-coated stainless steel counterparts.
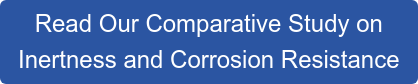
Mercury Testing
Mercury inertness testing on aluminum was performed by Ohio Lumex under a mercury concentration of 9.8 ng/L, injected into the 10.6 mL internal volume of each cell.
Decay curves below show comparable performances between SP12 and standard SilcoNert 2000 processes.
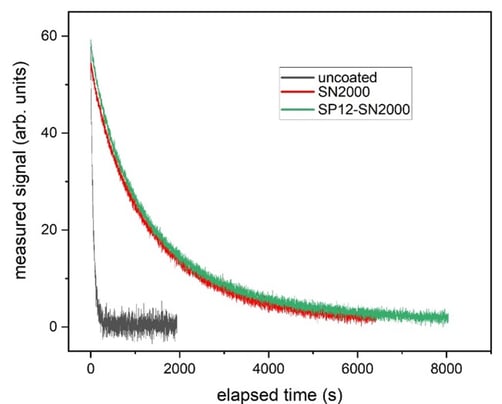
The elapsed time for decay below 10% (table below), shows that the SP12 coated SilcoNert samples performed about 16% better than the standard SilcoNert 2000 process. Both coating processes performed orders of magnitude better than the uncoated surface.
Cell ID
|
Elapsed time for decay below 10% of initial max. signal (seconds)
|
uncoated
|
156
|
SOP
|
3760
|
SP12
|
4391
|
Ammonia Testing
A group from Konkuk University in Korea1 designed and tested an ammonia sensor that is suitable for use in combustion situations (home heating, automotive, industrial, etc.). Ammonia, present in certain emissions, is known to be an active compound, particularly toward metal surfaces. SilcoNert® 2000 is well known to not allow ammonia to stick to metal surfaces, but SilcoNert 2000-SP12 applied to aluminum had not yet been investigated in ammonia test applications. The group showed good results for the SilcoNert-SP12 coating over an anodized aluminum part.
Figure 4 shows the comparison between an anodized test chamber and the SilcoNert 2000-SP12 coated aluminum test chamber. The SilcoNert 2000–SP12 coated chamber reached the 90% level (72 ppm) in an average of 66 seconds. Alternatively, the anodized aluminum chamber reached the 90% level in an average of 397 seconds across three runs. The graph in Figure 4 (below) is representative of just one of the three runs that were tested.1

Figure 4: Comparison of the anodized (blue) and SilcoNert 2000 – SP12 coated (orange) analyzer response to 80 ppm of ammonia. The black triangle and black circle indicate when the detectors have reached 72 ppm, which is 90% of the ammonia that was injected into the system.1
The authors noted that SilcoNert 2000–SP12 chamber was consistent in the three runs both before and after the 90% mark. The SilcoNert system quickly reached the full 80 ppm mark and maintained the stability through the time of the measurement. The anodized aluminum chamber experienced “high variability” before and after the 90% mark and took dramatically more time to reach the full 80 ppm level indicating the ammonia was lost due to high adsorption in the chamber.
Get more details about coating aluminum for ammonia testing, go to our blog post.
Corrosion Performance
Uncoated aluminum test coupons, standard coating process coupons, and SP12 process coupons were immersed in 5% hydrochloric acid solution (HCl) for 20 minutes. The photo below shows intense reaction in the solution while the SP12 coated sample (lower left) does not react in the solution.
Tests done in 5% HCl solution at room temperature, using 6061 Aluminum coupons
Uncoated Aluminum Sample Standard Coating SP12 Coated Aluminum
Corrosion rate obtained via polarization resistance scan after 20 minutes immersion in 5% HCl solution shows the SP12 coated aluminum improved corrosion resistance by orders of magnitude.
Visual inspection of the coupons after immersion show significant corrosion damage to the uncoated aluminum (left) and standard silicon coating process coated aluminum (center). Coated aluminum with the SP12 process (right) shows minimal damage to the surface after corrosion testing.
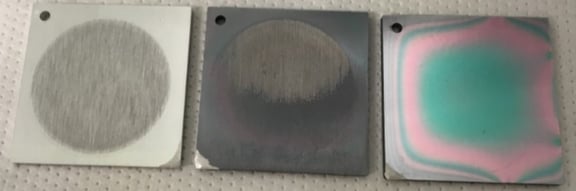
Salt Fog Testing
12 week salt fog testing on uncoated, standard coated, and SP12 coated samples show marked differences in corrosion resistance. The test was carried out in a salt fog (NaCl) chamber per ASTM G85.
Sample photographs (top image shown below), and enhanced magnification images (below middle) show significant corrosion while the coated part using the SP12 process show minimal corrosion.
This is supported by energy dispersive spectroscopy (EDS) analysis (lower tables). The higher oxygen content in EDS (highlighted) indicates more corrosion. That's because aluminum corrodes by oxidation to form aluminum oxide. The SP12 EDS oxygen results indicate O2 levels are significantly lower than the standard coating process or uncoated aluminum (8.8% vs. 54.1% and 63.9% respectively).
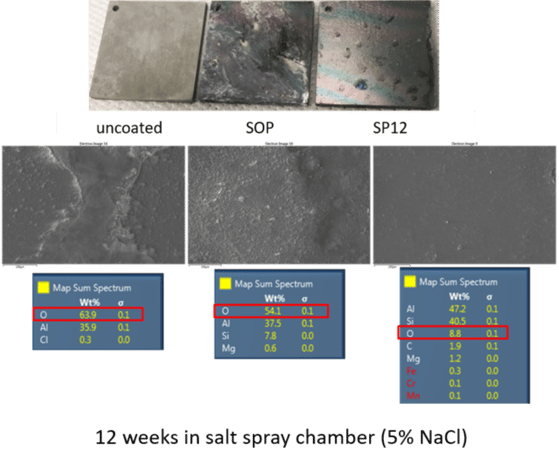
Want to learn more about how SilcoTek can improve the corrosion resistance of your products? Get lots of corrosion performance data and see how our coatings improve corrosion resistance without using costly super alloys, or part redesign. Click the box below to read our latest corrosion presentation.
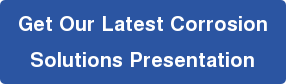
Summary
Aluminum and its alloys present challenges for silicon CVD deposition. Testing shows the SP12 process offers the same great benefits of our standard coating process without the negative effects when coating aluminum.
The issues our new SP12 process address include:
- Same process that work well on stainless steel do not work for aluminum.
- Aluminum catalyzes silicon crystallization and promotes nanowire growth.
- Poor cosmetic output and coating performance can result from crystallization and nanowire growth, this includes higher surface reactivity and corrosion.
A proprietary process (SP12) was developed by SilcoTek® to address aluminum substrate issues. The process employs a strategy of applying a primer layer to isolate the aluminum substrate from the silicon coating while maintaining the same external surface chemistry and coating performance, including improved corrosion resistance and superior inertness.
Performance benefits of SP12:
- Consistent and reliable output
- Enabled the same excellent inertness properties known to stainless steel on aluminum
- Greatly improved corrosion protection on aluminum substrate
- May be applied to porous surfaces or oxidation prone surfaces to improve performance.
A few items to note about the SP12 process:
- 5000-series Al alloys present a special compatibility risk. As a safety precaution, SilcoTek still does not treat 5000-series aluminum alloys.
- SilcoTek® can coat most grades of aluminum alloys. It is important that customers inform SilcoTek of the exact material grade of aluminum substrates prior to sending parts. Learn more by clicking here.
- The SP12 process involves exposure of the aluminum substrate to elevated temperature. Aluminum is weakened at temperatures in excess of 100° C. Because of the temperature related strength limitations associated with aluminum; SilcoTek does not recommend coating cylinders or any other aluminum product that will be pressurized or used in high stress applications. Learn more by clicking here.
Want to keep up with the latest in coating technology? Subscribe to our email and blog or follow us on LinkedIn.

Reference:
1Dinh, T.-V.; Choi, I.-Y.; Park, B.-G.; Lee, J.-H.; Kim, I.-Y.; Gil, H.-N.; Lee, S.-W.; Kim, J.-C. Development of a Negligible Zero-Drift NDIR Analyzer for Measuring NH3 Emitted from an Urban Household Solid Waste Incinerator. Atmosphere 2021, 12, 858. https://doi.org/10.3390/atmos12070858