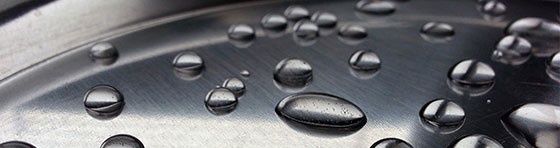
Can a process tailored for aluminum improve performance on stainless steel? We tested and found some surprising results.
Comparing SilcoNert to an Optimized SilcoNert Surface
SP12 is a special process for SilcoNert® 2000 that was developed for aluminum substrates. It has the same external surface chemistry as standard SilcoNert, but with an additional treatment underneath to overcome the undesirable reactions induced by aluminum. The SP12 process can also be applied to stainless steel substrates successfully. This blog compares a range of properties between the two versions of the SilcoNert coating (standard SilcoNert process (SOP) vs. SP12) on stainless steel substrates. We conducted various tests to evaluate and compare the coatings, including FTIR, Raman, water contact angle, SEM, EIS, polarization resistance and ASTM G31 immersion tests in hydrochloric acid.
In this blog post you will learn:
- How a SilcoNert® process designed for improving aluminum performance can benefit stainless steel surfaces in select applications with additional evaluation.
- How to compare the performance of a coating on various materials.
- Get comparative test results for SilcoNert coated surfaces and see how analytical flow path corrosion resistance can be improved .
|
Background Development of the SP12 Process:
SilcoNert® 2000 (we'll call it SilcoNert®, or SN2000 for short in this blog post) is one of SilcoTek’s most popular and recognized coatings. Over the past 20 years the coating has been adopted by a broad range of industries; benefiting analytical, oil/gas, refinery, and process sampling applications. (SilcoNert® is also known as Siltek® and Sulfinert® as sold through Restek® Corporation). Learn more about SilcoNert and how it improves the inertness performance of analytical and process flow paths, get the SilcoNert brochure.

The bulk of the SilcoNert coating consists of hydrogenated amorphous silicon, while the surface is further modified with organic functional groups to impart ultra-inertness properties. SilcoNert was originally developed and optimized on stainless steel (SS) substrates, which is also the most common substrate coated at SilcoTek.
This standard version of SilcoNert (shown as SN2000 in the comparison below), however, produces a less desirable coating on aluminum substrate, as it can induce several abnormal growth modes. As demand for inert coatings for aluminum continues to increase, there has been a growing need to optimize the SilcoNert coating for the aluminum market.
The SP12 process was developed for this specific reason. This special process utilizes a primer layer technique to overcome the undesirable reactions induced by aluminum, but still preserves the same external surface chemistry of SN 2000, as shown in Figure 1 below.
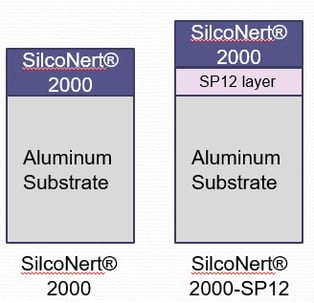
Figure 1: Comparison of the two versions of SN2000 coating
The SP12 process is not a replacement for SilcoNert but rather a process enhancement designed to enable optimal SN2000 coating on a wider variety of substrate materials. The standard SilcoNert coating is still the default process for stainless steel substrates, but SP12 can also be successfully applied to stainless steel parts, and there may be performance advantages by doing so. The goal of this blog post is to characterize and compare the standard (SOP SilcoNert process) vs. the SP12 process versions of the SilcoNert 2000 coating on stainless steel substrates and summarize their similarities and differences. Want to learn more about inert coatings and how they can improve analytical test quality? Get our inert coating webinar.

Data and Discussion:
For comparison of coating characteristics, the mirror-polished sides of coated smooth stainless steel coupons were analyzed by FTIR, Raman, static water contact angle and SEM (scanning electron microscope). Even though corrosion resistance is not one of the major properties sold for SilcoNert 2000 (SilcoTek offers Silcolloy® and Dursan® for corrosion applications), several corrosion tests (i.e. EIS, polarization resistance, ASTM G31 immersion) were performed to look for differences and any potential impact the primer layer may have on performance of the coated product. The coupons used in these tests were coated in two separate batches for each version (i.e. two SOP runs and two SP12 runs), to test run-to-run reproducibility, which looked good for both.
1) Coating characterization:
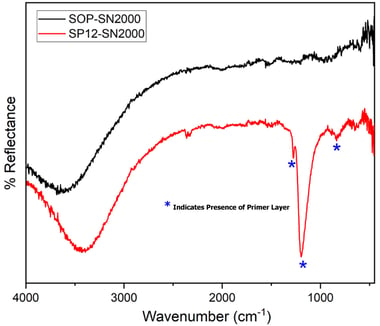
Figure 1: FTIR spectra comparison of the two versions of SN2000 coating, collected from the mirror-polished sides of coated 304 stainless steel coupons. Note presence of primer layer.
FTIR spectra of the two versions are distinct from each other as can be seen in Figure 1. As the bulk of SilcoNert® 2000 is made of amorphous silicon, and Si-Si vibration is inactive in IR, the IR spectrum of the standard process SilcoNert surface is rather featureless. In comparison, the peaks with asterisks in the SP12-SN2000 IR spectrum come from the primer layer, and thus can be used to distinguish the two versions. The broad bands around 3500 cm-1 observed in both spectra likely result from interference fringes, as the position of this band shifts from sample to sample as a function of the thickness of the coating.
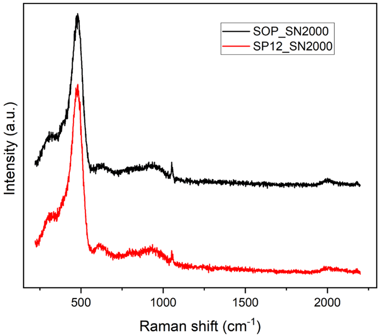
Figure 2: Raman spectra comparison of the two versions of SN2000 coating, collected from the mirror-polished sides of coated 304 stainless steel coupons
Raman spectra were collected on the same samples as a complementary technique to IR. Raman and IR have different selection rules and different sensitivities for the same bond, i.e. bonds that are inactive or weak in IR often have strong and sharp Raman shifts, and vice versa. The two techniques are therefore often used in combination to gain a more complete picture of the chemical bonds within a specimen to be analyzed.
Figure 2 shows that the Raman spectra of the two SN2000 coatings are identical to each other, both dominated by the Si-Si phonon peaks. This can be explained by a combination of factors:
1) The Raman laser used in the study has a smaller penetration depth than the IR light, thus limited detection of the primer layer.
2) The primer layer itself has relatively weak Raman response.
Therefore, Raman highlights the similarities between the two coatings (i.e. the amorphous silicon framework), whereas IR is more sensitive in detecting the primer layer presence.
The surface morphologies of both coatings were analyzed with scanning electron microscope (SEM) and can be seen in Figure 3. Both surfaces are similarly smooth, with the SOP coating exhibiting slightly more granular features than the SP12 coating. This type of variation is not uncommon from sample-to-sample and is not a general attribute of one coating or the other. No major difference is detected under a 10K magnification.
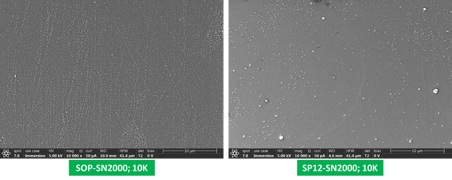
Figure 3: SEM comparison of the two versions of SN2000 coating, collected from the mirror-polished sides of coated 304 stainless steel coupons under 10K magnification
Static water contact angles (WCA) were measured on 10 samples from each coating and the results were plotted in Figure 4. Both coatings met the SN2000 WCA specification of ≥ 65°. The SP12 coating showed slightly higher WCA overall, but still within the typical SN2000 output range. Water contact angle is an indicator of surface energy (i.e. higher contact angle corresponds to lower surface energy), but is not directly correlated with coating inertness. Initial inertness testing showed comparable performance of SP12 to SOP-SN2000 in sulfur and trace level pesticide analysis. A separate blog post will be written to summarize all inertness test results once the data become available.
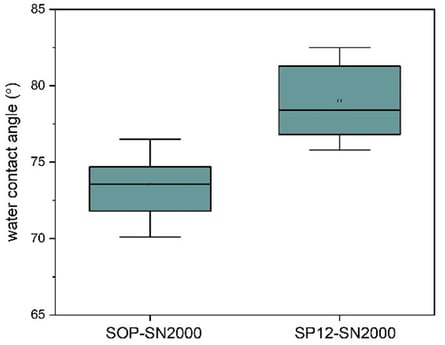
Figure 4: WCA comparison of the two versions of SN2000 coating, collected from the mirror-polished sides of coated 304 and 316 stainless steel coupons
On aluminum substrates, the primer layer in SP12 not only made a visible improvement in the coating’s cosmetic appearance, but also enabled superior corrosion performance in diluted HCl and salt water environments. This is because the primer layer effectively suppresses abnormal silicon growth on aluminum and promotes a smooth conformal coating, leading to greater bonding strengths and higher surface coverage.
On stainless steel substrates, both SOP and SP12 coating processes form nice conformal coatings and there is no visual disparity between the two versions. Several corrosion tests were carried out to probe any potential differences. Figure 5 illustrates EIS (Electrochemical Impedance Spectroscopy) data over 27 days for coated SS coupons exposed to 5% NaCl solution.
Want to learn more about how SilcoTek can improve the corrosion resistance of your products? Get our Corrosion Presentation.
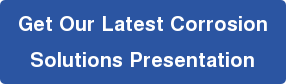
EIS is a largely non-destructive tool to study and evaluate the performance of protective coatings on metal substrates. A good barrier coating usually displays excellent linearity of increasing impedance vs. deceasing frequency and a very high impedance value at low frequencies (i.e. the higher the impedance value, the more resistance by the coating to the solution permeation). While both coatings showed good stability over 27 days and minimal EIS changes, the primer layer in SP12-SN2000 does appear to contribute to better linearity and higher impedance values, correlating with superior barrier properties.
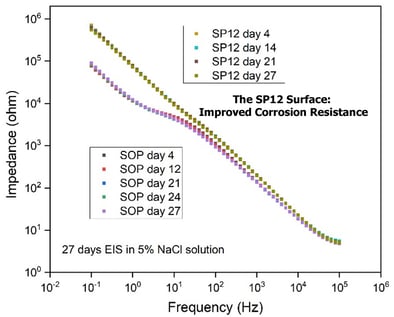
Figure 5: EIS comparison of SOP vs. SP12-SN2000 coatings on stainless steel over 27 days of exposure to 5% NaCl solution
Potentiodynamic polarization resistance scan is another accurate and rapid testing technique commonly used in real time corrosion monitoring of metallic samples. This test can report the corrosion rate of the system at the time of the measurement.
Figure 6 shows a comparison between the two coatings on 304 stainless steel substrates after immersion in a 5% hydrochloric acid (HCl) solution. The data shows performance at the start of the test and after 48 hours of immersion. The primer layer in the SP12-coating again appears to have some benefit in reducing the corrosion rate and slowing down the degradation over 48 hours of HCl exposure. The same test was performed on coated 316 stainless steel substrate as well, and similar results were observed.
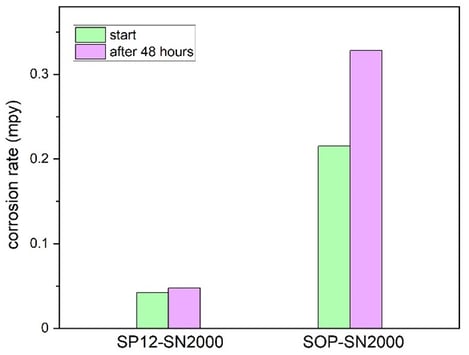
Figure 6: Polarization resistance comparison of SOP vs. SP12-SN2000 coatings over 48 hours of exposure to 5% HCl solution
A more aggressive corrosion test was carried out by immersing testing coupons in 6M (18.5%) HCl solution for one week (168 hours) per ASTM G31 protocol. Figure 7 shows that although both coatings reduced the corrosion rate by about 4x in comparison to the uncoated control coupons, they performed similarly to each other in this test. The primer layer that showed benefits in slower and milder corrosion environments previously (i.e. 5% NaCl solution and 5% HCl solution) did not seem to make a significant impact in a more aggressive environment.
To make sense of this, an analogy may be made between the primer layer and a very thin but dense barrier wall. When the corrosion force is small and gradual like water permeation, the wall adds measurable protection to the substrate underneath it. However, when the corrosion force is heavy and vigorous, like a hammer or tide pounding on the wall, the wall is simply too thin to hold up and will break and succumb at some point, showing negligible impact under these conditions. For this reason, we recommend Silcolloy® or Dursan® for aggressive corrosion applications such as this.
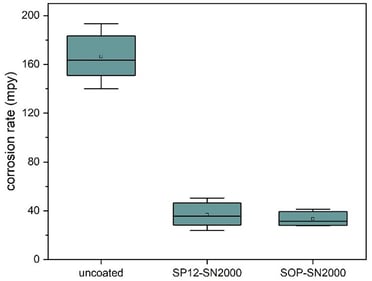
Figure 7: Corrosion rate comparison of uncoated 316L SS corrosion coupons vs. SOP and SP12-SN2000-coated 316L SS corrosion coupons over 168 hours of exposure in 18.5% HCl solution
Conclusion:
SilcoTek® has developed a process called SP12 to optimize the SilcoNert® 2000 coating on aluminum substrates and is approved only for that process. The study above indicates that the SP12 process may be an option for limited applications where our current inert coatings, Silcolloy® and Dursan®, are not appropriate for the application. While the standard SilcoNert coating process remains as the default process for incoming stainless-steel parts, the SP12 coating process version can also be successfully applied to stainless steel if needed to troubleshoot in very select applications. Further product evaluation would be required in order to approve the SP12 process on stainless steel.
This blog examined the coating characteristics of SOP and SP12 SilcoNert coating processes on stainless steel coupons and compared their corrosion resistance in different environments ranging from mild to harsh.
Raman spectroscopy was found to highlight the similarities between the two coatings, whereas FT-IR is more sensitive in detecting their differences. SEM images and water contact angle values were collected and showed similar properties.
Coating coupons using the SilcoNert SP12 process outperformed the standard SilcoNert coating process in both corrosion tests carried out in 5% NaCl solution via EIS, and in 5% HCl solution via linear polarization resistance. However, the two coatings demonstrated similar performance in a harsher corrosion test with a long-term exposure to 18.5% HCl solution.
It was concluded that the thin primer layer in SP12 is beneficial in milder corrosion conditions but has negligible impact when the corrosion force overwhelms the thin barrier. Therefore, Silcolloy® or Dursan® coatings are recommended for more aggressive corrosion applications.
Initial inertness testing showed comparable performance of the SP12 process when compared to the standard SilcoNert® 2000 process in sulfur and trace level pesticide analysis. A separate blog post will be written to summarize all inertness test results once the data become available.
Have a question about how to test our coatings in your application? Contact our Technical Service Team and we'll apply our vast knowledge of coating testing to your application free of charge! To get the latest in coating advancements, follow us on LinkedIn.
