
Aluminum is lightweight and inexpensive but it can be reactive in analytical flow paths. We discuss how to improve the inertness and corrosion resistance of aluminum.
Improve Aluminum Corrosion Resistance and Inertness
The physical properties of chemical resistant aluminum (Al) alloys are versatile and ideal for use in a variety of analytical, manufacturing, or industrial applications. Aluminum can react with chemicals used in some analytical applications. Aluminum corrosion resistance can also be an issue in some applications involving exposure to corrosive chemicals. We discuss how CVD silicon barrier coatings make aluminum inert and corrosion resistant.
In this blog post you will learn:
- How to improve the corrosion resistance of 6000 series aluminum.
- How a SilcoNert® 2000 applied using our new SP-12 process (optimized for aluminum), performs in inertness and corrosion tests and helps to prevent chemical adsorption in analytical applications.
- How coated 5000 series aluminum compares to 6000 series aluminum in corrosion studies.
|
First a disclaimer: Because of the temperature related strength limitations associated with aluminum; SilcoTek® does not recommend coating cylinders or any other aluminum product that will be pressurized or used in high stress applications.
Aluminum is weakened at temperatures in excess of 100° C and because we process parts above that temperature aluminum strength can be compromised. Go to our Coating Aluminum web page to learn more.
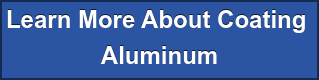
But there are many low stress applications where aluminum corrosion resistance and inertness is needed. In this blog post we'll discuss recent coating developments relating to inertness, non-reactivity, and corrosion resistance of 6000 series aluminum.
Background
While stainless steel is naturally compatible with SilcoTek’s CVD chemistry and fosters a smooth amorphous silicon film growth (preferred), aluminum interacts very differently with the CVD process, i.e. they not only induce silicon nanowire growth but also catalyzes the amorphous-to-crystalline transition so that the deposited film contains a mixture of amorphous and micro-crystalline silicon.
These growth abnormalities usually manifest as cosmetic coating defects (dark haze, dirty finish, grainy appearance, etc.), and as a result, require SilcoTek to employ special handling procedures for aluminum alloys to control undesirable growth patterns. Here's a picture of a SilcoNert® 2000 coated aluminum coupon without using our new SP-12 process (shown on the left) and a SilcoNert 2000 coated aluminum coupon (right) using our new SP-12 process.
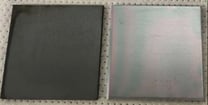
Figure 1: Comparing the surface quality of SilcoNert® 2000 coated aluminum (left) and SilcoNert applied using the SP-12 process (a refined process for aluminum surfaces). The right coupon shows a significant improvement in surface quality.
As you can see there's a big improvement in the appearance of the aluminum surface but that's not the real benefit of the process. Let's discuss how the SP-12 process improves material performance of aluminum in analytical applications.
The process
SP-12 is aimed at improving coating results on aluminum substrate in general. The new process, developed by SilcoTek’s R&D team, involves a more refined CVD process that was designed to address the interface challenges encountered in coating aluminum with silicon coatings. The new CVD process (called SP-12) is more about refinement of the process than a new coating. In fact a SilcoNert coated aluminum surface will have the exact same surface chemistry when applied using the SP-12 process as SilcoNert when applied to stainless steel. The primary impact of the SP-12 is in the consistency of the coating and improved overall coating surface quality. Let's look at the data.
Corrosion Testing
Polarization resistance scans were carried out in 5% HCl solution to test the corrosion resistance of the coated coupons, and the results were shown in Figure 2. Average value of the 5083 and 5456 alloys for each coating type is reported, as these two alloys performed similarly. The Dursan® coating showed no benefit over the uncoated samples, whereas the SP-12 reduced the corrosion rate by about half. A much larger benefit from the SP-12 coating was observed when 6061 aluminum alloys were tested (Figure 3), indicating that the high Mg content in the 5000-series is likely limiting the extent of the coating’s benefit.
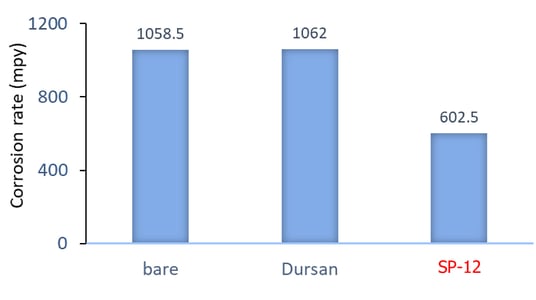
Figure 2: Corrosion rate in mils per year (mpy) obtained from polarization resistance scans in 5% HCl solution (20 minutes immersion) on 5083 and 5456 aluminum alloys
Figure 3: Corrosion rate in mils per year (mpy) obtained from polarization resistance scans in 5% HCl solution (20 minutes immersion) on 6061 aluminum alloys
Inertness Testing
Chemical inertness applications were verified by testing SilcoNert 2000 (applied by the SP-12 process) coated aluminum sample cylinders to confirm comparable inertness performance as standard SilcoNert 2000 coated stainless steel sample cylinders. The inertness response of the coated aluminum sample cylinder was comparable to the standard SilcoNert surface and greatly improved the inertness response compared to uncoated stainless steel surfaces. Glass GC inlet liner testing performed also showed similar performance of SP-12 and standard SilcoNert 2000. Figure 4 below compares the inertness performance of uncoated stainless steel to a SilcoNert 2000 coated surface. The SilcoNert surface prevents interaction of compounds with adsorptive and reactive-prone surfaces like stainless steel and aluminum.
/Inertness%20Response.png?width=535&name=Inertness%20Response.png)
Conclusion
The SP-12 process was found to work very well for 6061 Al. The new coating delivered better visual output and smooth surface coverage on the 5000-Al coupons, but the corrosion performance did not match that on 6061 Al. The inertness performance of SilcoNert coated aluminum is comparable to SilcoNert coated stainless steel. This allows the user to employ aluminum in more demanding analytical applications while enjoying significant weight and cost savings.
Want to learn more about about how our coatings perform in your application? Go to our Coating Applications Page, or ask the experts on LinkedIn.
