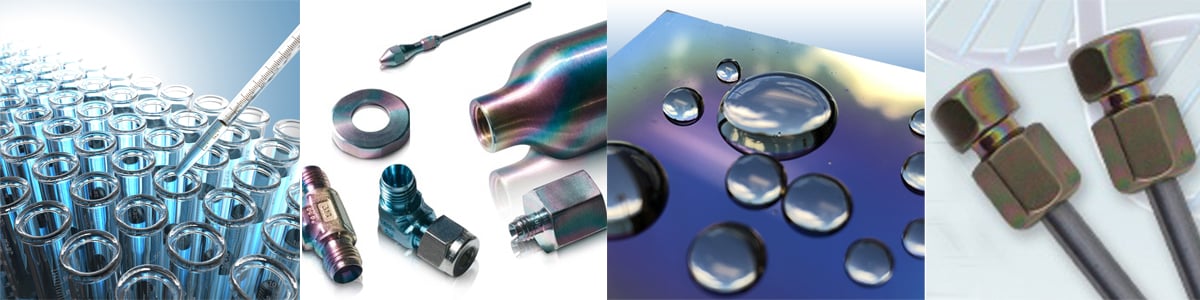
A group from Konkuk University in Korea tested SilcoNert 2000 on aluminum and compared the results with anodized aluminum.
Can Aluminum be Used for Testing Ammonia?
A group from Konkuk University in Korea looked to create an ammonia sensor that would be suitable for use in combustion situations (home heating, automotive, industrial, etc.). Ammonia is known to be an active compound, particularly toward metal surfaces. SilcoNert® 2000 is well known to not allow ammonia to stick to metal surfaces, but SilcoNert 2000 for aluminum has not yet been investigated. The group showed good results for the coating over an anodized aluminum part.
In this blog post you will learn:
- How SilcoNert® coated aluminum (the process is called SilcoNert-SP12) improves aluminum response when compared to anodized aluminum.
- How to measure ammonia response on metal surfaces and improve air quality measurement.
- How anodized aluminum compares to SilcoNert when improving aluminum inertness.
|
Background:
Ammonia can be an issue for the health of plants, animals, and humans. Ammonia exposure can cause numerous conditions depending on concentrations, including eye and skin irritation, burns, coughing, wheezing, shortness of breath and potentially death. The bulk of ammonia in the atmosphere comes from agricultural activities such as fertilizer production and animal husbandry. A smaller, yet still significant amount (roughly 20%) of the emissions are from combustion processes across a wide variety of industries. Continuous air quality monitoring of ammonia from these processes is important for regulatory purposes as well as general health.

There are a variety of ways to monitor ammonia, but a group from Konkuk University in Korea looked to develop a cold-type non-dispersive infrared analyzer. The details on that analyzer can be found in their paper published in Atmosphere.1 One hurdle for developing such an analyzer is the choice of materials to build the instrument. Ammonia can be quite reactive toward metals and many polymers. The group investigated the use of SilcoTek’s new coating developed especially for aluminum: SilcoNert 2000–SP12. This blog post will focus on their investigation between an anodized aluminum gas chamber vs an aluminum chamber coated with SilcoNert 2000–SP12.
Read more about how SilcoNert improves ammonia detection. Read the study from EURAMET and EMRP by clicking the box below.

The research group was investigating ammonia in trace levels and noticed that unlike the other gases in their study, the anodized aluminum chamber would adsorb small amounts of the ammonia causing issues with response time. The researchers discussed various options such as Teflon coating, but noted that it is very difficult to apply Teflon coating to long narrow spaces, such as the chamber for their analyzer seen in Figure 1. They also discussed switching to a different alloy such as stainless steel, but steel experiences the same adsorption issue. They then turned to SilcoNert 2000 which has been shown to not allow ammonia adsorption to its surface.
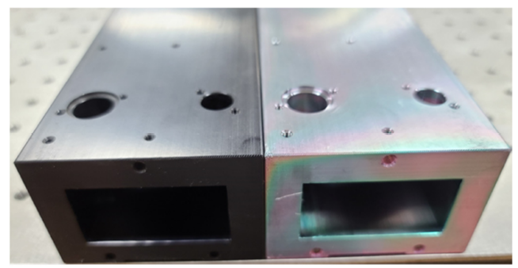
Figure 1: Two different chambers for the cold-type non-dispersive infrared analyzer. Left is the anodized aluminum chamber and the right shows the SilcoNert 2000–SP12 coated chamber.
Aluminum has many advantages over steel in this application such as ease of machinability and its comparatively light weight. SilcoTek® has previously discussed issues with applying SilcoNert 2000 to aluminum substrates and the steps that have been taken to develop a new coating that successfully coats aluminum.
SilcoNert was originally developed and optimized on stainless steel (SS) substrates, which is also the most common substrate coated at SilcoTek. This standard version of SilcoNert (shown as SN2000 in the comparison below), however, produces a less desirable coating on aluminum substrate, as it can induce several abnormal growth modes. As demand for inert coatings for aluminum continues to increase, there has been a growing need to optimize the SilcoNert coating for the aluminum market.
The SP-12 process was developed for this specific reason. This special process utilizes a primer layer technique to overcome the undesirable reactions induced by aluminum, but still preserves the same external surface chemistry of SilcoNert 2000, as shown in Figure 2 below. You can read the complete blog post about the development of SP12 here.
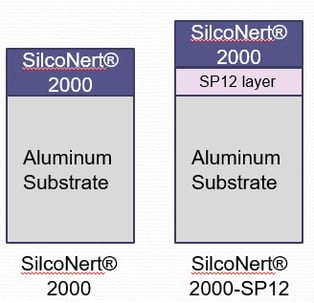
Figure 2: Comparison of the two versions of SN2000 coating
Figure 3 shows the comparison between the anodized chamber and the SilcoNert 2000-SP12 chamber. The SilcoNert 2000–SP12 coated chamber reached the 90% level (72 ppm) in an average of 66 seconds. Alternatively, the anodized aluminum chamber reached the 90% level in an average of 397 seconds across three runs. The graph in Figure 3 (below) is representative of just one of the three runs that were tested.

Figure 3: Comparison of the anodized (blue) and SilcoNert 2000 – SP12 coated (orange) analyzer response to 80 ppm of ammonia. The black triangle and black circle indicate when the detectors have reached 72 ppm, which is 90% of the ammonia that was injected into the system.
The authors noted that SilcoNert 2000–SP12 chamber was consistent in the three runs both before and after the 90% mark. The SilcoNert system quickly reached the full 80 ppm mark and maintained the stability through the time of the measurement. The anodized aluminum chamber experienced “high variability” before and after the 90% mark and took dramatically more time to reach the full 80 ppm level indicating the ammonia was lost due to high adsorption in the chamber.
Is SilcoNert 2000 applied with the SP12 process different from SilcoNert applied to stainless steel?
Basically no. The SilcoNert applied to stainless steel is essentially the same surface as what's applied to aluminum. The SP12 process is not a replacement for SilcoNert but rather a process enhancement designed to enable the SilcoNert 2000 coating to be applied on a wider variety of substrate materials. The standard SilcoNert coating is still the default process for stainless steel substrates.
Conclusion:
Researchers looking to develop an ammonia detection system investigated the use of anodized aluminum and SilcoNert 2000–SP12 coated aluminum. They found that while an anodized aluminum chamber had inconsistent results, a chamber coated by SilcoTek yielded fast and consistent results. The group investigated numerous other conditions to optimize the detector, but when it comes to material compatibility, SilcoNert 2000-SP12 was the clear winner.
Want to keep up with the latest in coating technology? Follow us on LinkedIn or subscribe to our email and blog.

Reference:
1Dinh, T.-V.; Choi, I.-Y.; Park, B.-G.; Lee, J.-H.; Kim, I.-Y.; Gil, H.-N.; Lee, S.-W.; Kim, J.-C. Development of a Negligible Zero-Drift NDIR Analyzer for Measuring NH3 Emitted from an Urban Household Solid Waste Incinerator. Atmosphere 2021, 12, 858. https://doi.org/10.3390/atmos12070858