Preventing Corrosion in Solar and Wind Applications
Fittings, solar cell support structures, wind turbines and heat exchangers are exposed to pollution related corrosion and extreme environmental conditions. Additionally, systems located in coastal environments are exposed to high salt levels which can lead to component corrosion and failure. Get our corrosion presentation to learn about all our corrosion resistant coatings for stainless steel and other metals.

Typical polymeric coatings are degraded by UV and acid rain exposure, limiting their ability to achieve the target 30 year life. Metallic coatings can extend service life but cannot achieve the target 30 year lifespan. That leaves corrosion resistant alloys which will certainly achieve the performance goal but will add cost and lead time. Semi metallic coatings like silicon offer a favorable mix of corrosion resistance, UV resistance, and durability that can help solar and wind fields achieve their target 30 year life. Here are some examples of how silicon coatings can improve component and system life.
Salt Exposure
EIS (Electrochemical Impedance Spectroscopy) data show Dursan remains pinhole free after over 250 days of salt spray exposure. In the experiment below, test coupons were subjected to salt spray for 247 days.
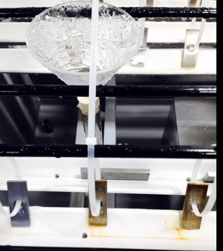
Figure 1: Test coupons in salt spray chamber
The test samples were periodically tested by introducing a voltage between 5 to 50 mV in a range of frequencies. If the resulting data points do not diverge or curve as the voltage and frequencies change, that indicates no voltage breakthrough and no additional pin holes in the surface were produced during the salt spray exposure. For example the uncoated stainless steel test coupon began to show pinholes after just 15 days of exposure. Note the divergent EIS lines below.
After 61 days of salt spray exposure, the Dursan coated stainless steel test coupon exhibited minimal pin-holing and EIS divergence.
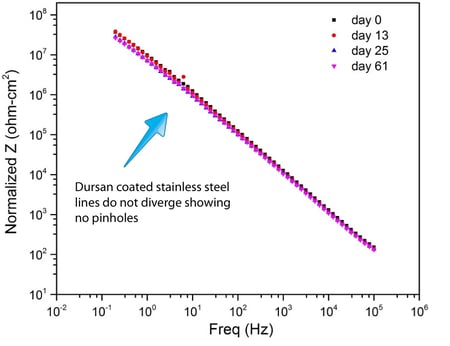
We continued the salt spray test for 247 days. On day 247 we tested the Dursan coupon again and found minimal divergence, indicating little pitting corrosion.
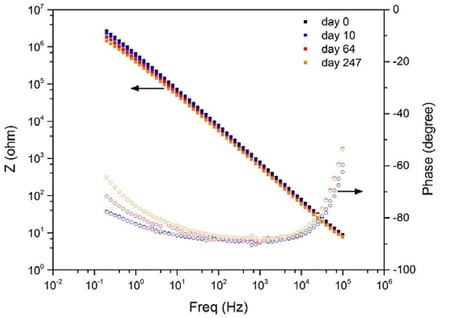
Chloride Exposure
Industrial acid pollution is common, especially in urban environments. Acid exposure can significantly reduce the life of solar and wind systems, making improved acid corrosion essential to sustaining energy production over the projected 30 year lifespan. We conducted a series of comparative ATSM G31 immersion tests of various alloys to see how they performed after exposure to concentrated hydrochloric acid. We found the Dursan® and Silcolloy® coated samples performed comparably to Hastelloy® and other super alloys. All at a fraction of the cost of exotic alloys.
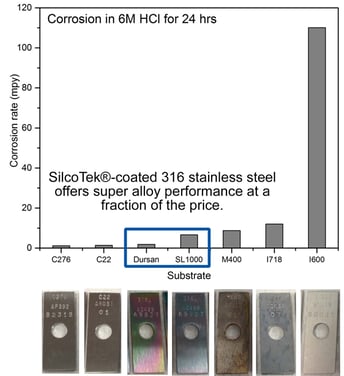
Environmental Pollution and Sulfuric Acid Corrosion
Solar and wind farms are often exposed to industrial pollution, one of the most common pollutants being sulfur species like sulfuric acid found in acid rain. Over tim,e exposure to acid rain will degrade fittings and structural components of wind and solar farms. Silicon coatings can improve the durability of surfaces exposed to acid rain.
ASTM G31 immersion comparison of uncoated stainless steel vs. silicon coated (Dursan® and Silcolloy®) surfaces shows an order of magnitude reduction of sulfuric acid corrosion rate (see graph below). Making silicon coatings an option to consider when increasing the life of renewable energy systems.
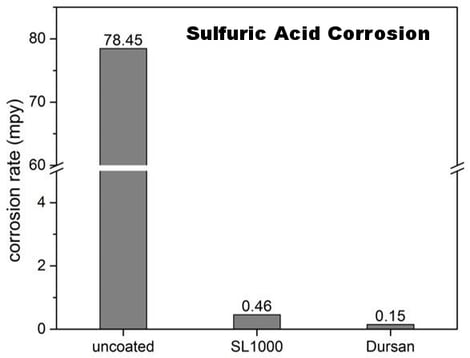
Galvanic Corrosion
Comparative galvanic corrosion was measured by immersing uncoated and coated aluminum test coupons into a salt solution. Galvanic potential was measured in a cathodic/anodic flat cell at a separation distance of 14 cm. The artificial seawater electrolyte conformed to ASTM D1141. The silicon coated (Dursan® and Silcolloy®) coupons exhibited significantly higher potential indicating fewer pinholes in the surface.
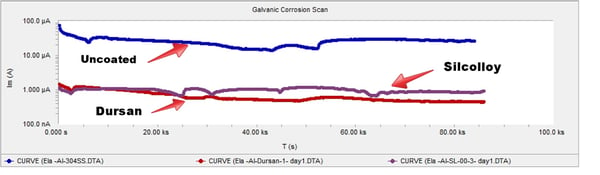
Read the entire galvanic corrosion comparison by clicking the report below.
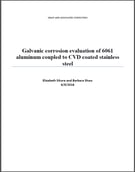
A Unique Problem for CSP Plants
Concentrated Solar Power plants (CSP) face one additional challenge. Temperatures on some CSP surfaces can reach 550 to 750c. Making it impossible to consider common coatings when selecting corrosion resistant materials. Silicon coatings can withstand exposure to extreme temperatures, making coatings like Silcolloy and Dursan an attractive option when improving corrosion resistance in high temperature applications like CSP plants. The SilcoTek R&D Team studied how our coatings perform under high temperature corrosion conditions. Read our Technical Insight to learn how we improved the thermal performance of our coatings.

Continued Reading
Interested in learning more about coatings for renewable energy? Go to our Coating Properties Page and then contact a Technical Service Team Expert to discuss your application. You can also go to our Learning Center to read our latest e-books and Technical Insights.