Learn how Silcolloy® and Dursan® improve the corrosion resistance and reduce maintenance of plant exhaust and scrubber systems.
Improving the Lifetime of Industrial Exhaust Systems
Exhaust systems, flares, and gas abatement systems protect indoor and outdoor environments but they also can be exposed to extreme conditions including corrosives and high temperatures. In this blog post we'll discuss challenges to exhaust, abatement and scrubber systems and how silicon coatings can improve corrosion resistance, reduce maintenance and downtime, and extend the life of exhaust systems.
In this blog post you will learn:
- How silicon coatings like Dursan® and Silcolloy® improve corrosion resistance.
- How Silcolloy can prevent oxidation of metal surfaces.
- How SilcoTek® coatings improve equipment uptime, reduce maintenance and cost.
|
Corrosion in Exhaust and Emission Control Systems
Exhaust systems and their associated abatement systems protect both the indoor and outdoor environment. System duct and components are frequently exposed to a mix of corrosives, high temperatures, and environmental conditions that can damage systems. Challenging conditions often result in costly shutdowns for maintenance.
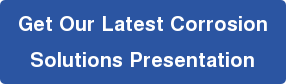
Oxidation resistant, and corrosion resistant high purity coatings, like Silcolloy®, are often used in corrosive and high temperature exhaust applications. High durability coatings prevent corrosive attack and oxidation of the stainless steel and other alloys used in exhaust and emission control systems. Results can be surprising, with a service life extension of orders of magnitude over uncoated systems.

Solving Difficult Corrosion Problems in Exhaust Systems
SilcoTek® coatings help to prevent common corrosion related problems including:
- Frequent component replacement
- Sample probe damage and failure
- Lost productivity due to excessive downtime
|
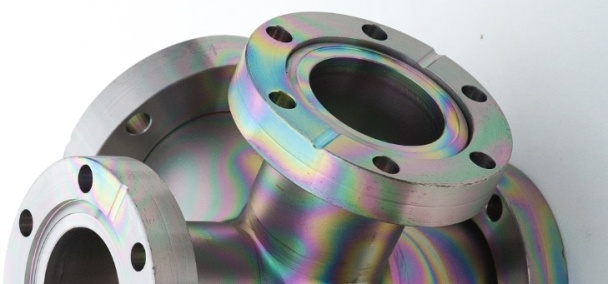 |
ASTM immersion testing proves SilcoTek® coated stainless steel enhances corrosion resistance by orders of magnitude, matching the performance of super alloys in many applications. Even after immersion in concentrated hydrochloric acid (below) the Dursan® coating and Silcolloy coated stainless steel coupons continue to perform with minimal corrosion, demonstrating performance comparable to super alloys.
SilcoTek® coatings perform in a variety of corrosive environments including sulfuric acid and bleach as shown in the table below.
Comparative Corrosion Summary |
|
|
|
Stainless Steel Corrosion Rate (mpy) |
Dursan Coated Stainless Steel (mpy) |
6M Hydrochloric Acid, 24 hr exposure |
160 |
1 |
25% Sulfuric Acid, 24 hr exposure |
55 |
5 |
52 Week Salt Spray |
<0.01 |
<0.01 |
Bleach |
1.7 |
0.1 |

Oxidation Resistance
SilcoTek coatings act as an inert and high purity barrier, improving the oxidation resistance of substrates without reacting with exhaust gases. The photo below compares SOP coated 316 stainless steel coupons with an oxidation resistant coating. As the temperature increases, the oxidation becomes more evident on with the SOP samples.
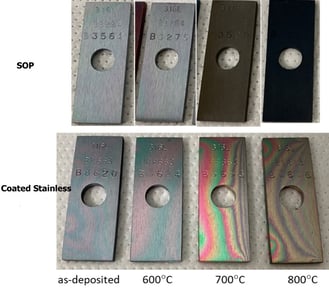
Inert coatings like Silcolloy® improve oxidation and corrosion resistance of stainless steel by preventing oxygen from interacting with the stainless steel surface; increasing oxidation resistance by orders of magnitude.
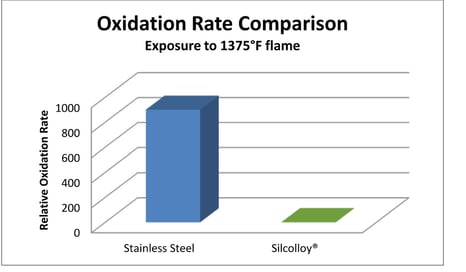
Reduce Maintenance and Downtime
Calculating the benefit of the substantial improvement in corrosion resistance can
be translated to better machine performance and efficiency. For example, if we assume that the corrosion rate of 316L stainless steel in hydrobromic acid (HBr) solution approximates 3000 hours of uptime before failure, the Silcolloy coated part would allow over 23,000 hours of uptime before failure. Less maintenance means lower cost.
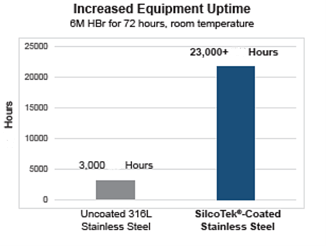
The initial cost of coated products is also lower than using super alloys to solve corrosion problems in exhaust systems. The overall relative cost of Dursan coated stainless steel compared to a high performance alloy, like Hastelloy®*, can be significant as seen in the comparative graph below.
Conclusion
Oxidation resistant, and corrosion resistant high purity coatings, like Dursan® and Silcolloy®, are used in exhaust applications to reduce downtime, maintenance, and cost of the system. The coating prevents corrosive attack and oxidation of duct and components used in exhaust and gas abatement systems.
We offer hybrid coatings that are optimized for your specific applications to better tailor a solution to your exhaust system problem. Results can be surprising, with service life extension of orders of magnitude over uncoated systems.
To learn more about how our coatings can improve the performance of your products, go to our Applications Page. You can keep up with the latest in material science by subscribing to our blog or by following us on LinkedIn.

*Hastelloy® is a trademark of Haynes® Corporation