We tested our coatings to see how they held up when exposed to a severe alkaline. Here's what we found out.
Can Silicon Coatings Withstand Base Exposure?
Occasionally, SilcoTek’s customers require alkaline exposure in their applications. For example, customers may need a coating that can withstand exposure in a clean-up step after use, or as part of the work process itself. Unfortunately the chemical nature of silicon makes it vulnerable to damage when exposed to a base.
In fact alkaline exposure can remove or damage silicon coatings rapidly under severe conditions. But modifications or enhancements to silicon coatings can improve base exposure performance. This blog post compares the performance of various modified silicon coatings and explores the impact of 5% sodium hydroxide (NaOH) solution on four SilcoTek® coatings (one standard coating and 3 developmental coatings) the coatings tested are:
- Dursan®: An inert high durability silicon coating (a-SiOX:CHY) and one of our most popular coatings.
- Coating 1: A developmental high temperature silicon coating.
- Coating 2: A developmental coating featuring a hydrophobic carbosilane deposition.
- Coating 3: A developmental hardened silicon coating.
In this blog post you will learn:
- How various silicon coatings perform under exposure to sodium hydroxide (NaOH).
- How a carbosilane deposition can improve base resistance under prolonged alkaline exposure test conditions.
- How to test coatings for base exposure.
|
Test Summary
The coatings were tested at 40°C with sonication a total of 200 minutes and up to 10 cycles. The conditions were chosen to imitate parameters used by a customer in a typical cleaning protocol. The hydrophobic carbosilane deposition, Coating 2, was found to have the best resistance against alkaline exposure, followed by Coating 3. Dursan® exhibited some coating loss after 10 cycles, whereas Coating 1 lost all the silicon layer after only one cycle but maintained the undercoat throughout the rest of the exposure. Learn more about our coating applications by going to our website.

Background
SilcoTek’s customers come from a broad range of industries, and their applications encompass the full pH range (0-14). Alkaline exposure is sometimes a necessary component in their process flow, either embedded in the main work environment or as a clean-up step. However, prolonged alkaline exposure can remove silicon-based coatings. The rate at which the coating is removed during alkaline exposure depends on the alkali concentration, temperature, and whether a physical agitation (such as sonication) is present. Therefore, SilcoTek’s coatings (a modified silicon chemistry) can still hold up well and provide lifetime benefits for some applications that involve alkaline exposure, provided the conditions are not so aggressive that they quickly digest the coating.

This blog post explores the impact of 5% NaOH solution on four SilcoTek coatings, one commercially available (Dursan), and three developmental coatings Coating 1 (a high temperature silicon coating), Coating 2 (a hydrophobic carbosilane coating), and Coating 3 (a hardened silicon coating). The conditions were chosen to imitate parameters used by a customer in their clean-up protocol, for up to 10 cycles. The experiment found Coating 2 had the most resistance to the testing conditions, followed by Coating 3, Dursan , and finally Coating 1.
Experiment and Discussion
5% sodium hydroxide (NaOH) solution was prepared by diluting a stock solution of 50% NaOH in water. The test was carried out in a SharperTek XP-Pro heated ultrasonic cleaner with 40 KHz sonication frequency. The Sodium hydroxide (NaOH) bath temperature was controlled in the range of 42.2 – 42.8°C throughout the test. Each testing cycle consists of 20 minutes of immersion and sonication of coated coupons in the heated 5% NaOH bath, while thickness and water contact angle (WCA) readings were taken after 1, 3, 6 and 10 cycles. The coupons were rinsed in deionized (DI) water multiple times followed by nitrogen drying before the thickness and WCA measurements were taken.
Three 316L stainless-steel coupons for each coating type were used in this experiment, and all measurements were taken on the mirror-polished side. Three data points on similar regions of the coupon were taken from each sample, resulting in a total of nine data points (thickness and WCA respectively) from each coating type. The average of the nine data points was reported.
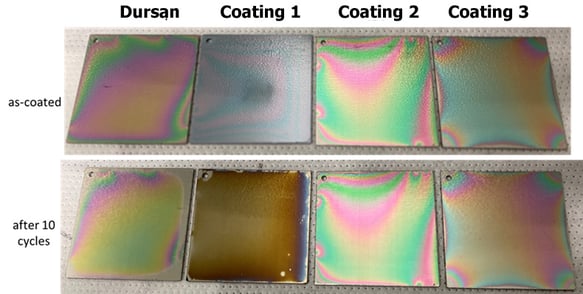
Figure 1: Visual appearance comparison of the four coatings before and after the test
Photos of a representative coupon from each coating were taken before and after the test for comparison, as shown in Figure 1. There was some coating loss around the edges for the Dursan® coupon, the back (non-polished) sides of the Dursan coupons also exhibited partial-to-complete coating loss (not shown in the photo).
The three data points were taken on regions with residual coating, showing an average of 57 nm total coating loss on those regions. Developmental Coating 1 is comprised of a primer layer with an amorphous silicon (a-Si) coating on top of it. While the a-Si coating is completely removed after only one cycle of exposure, the primer layer remained throughout the rest of the exposure, losing about 10 nm between each measurement, resulting in about 40 nm of the primer layer left at the end of the test.
The best NaOH resistance was observed with Coating 2, which showed virtually no change both in visual appearance and thickness measurement after 10 cycles of exposure. Lastly, Coating 3 showed very minimal visual impact and about 47 nm of coating loss on average after 10 cycles. The thickness evolution throughout the test was plotted in Figure 2 below.
Figure 2: Thickness change of the four coatings after the specified number of cycles
Water contact angle (WCA) is another important surface property of the coatings. Robustness in WCA after NaOH exposure can be beneficial in certain applications where hydrophobicity may be a sought-after property. Figure 3 (below) shows that once again, Coating 2 exhibited the smallest change after the test. Whereas the other three coatings all became very hydrophilic after just one cycle. Coating 2 maintained a WCA of 75° after 10 cycles. The surface chemistry of Coating 2 seemed to be most effective in preventing/reducing hydroxylation caused by the exposure conditions.
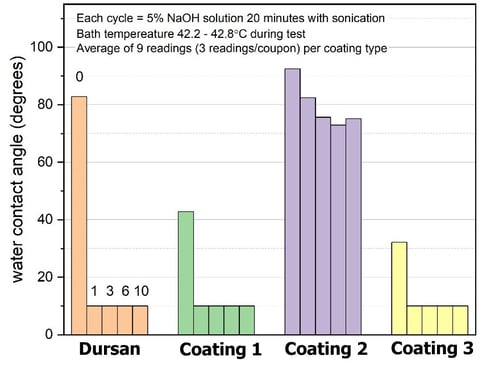
Summary
SilcoTek has conducted an experiment to imitate strong base (NaOH) exposure conditions used in typical manufacturing cleaning, stripping, and finishing operations. The test was designed to determine which coating may best withstand alkaline exposure.
Four coatings (one commercial and three developmental) were examined. The coating exposure performance was rated from best to worst. Coating 2 performed best followed by Coating 3, Dursan, and finally Coating 1. Coating 2 exhibited virtually no change both in visual appearance and thickness measurement after 10 cycles of exposure (200 minutes of sonication), while maintaining a water contact angle of 75° at the end of the test.
The developmental Coating 2 is available on a highly limited test basis. Contact our Technical Service Team to discuss your application. We'll be happy to help recommend the best coating material solution for your application. Our team can also develop a customized coating solution for your application and consult with coating evaluation test methods that fit your needs.
To stay in touch with the latest in chemical resistant coating development and material science, subscribe to our email and blog or follow us on LinkedIn.
