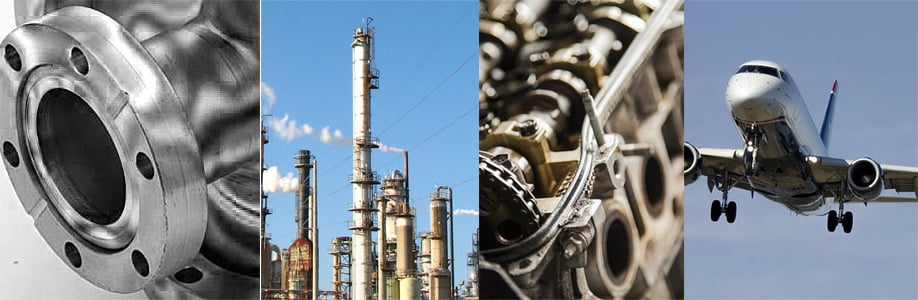
In a previous blog post we discussed the difference between a hard and wear resistant tough coating. Now let's compare wear resistance and hardness test data.
Coating Wear Resistance and Hardness Testing
In this blog post we'll test and compare stainless steel and three SilcoTek® coatings (Silcolloy®, Dursan®, and an experimental R&D coating) for hardness. We'll also compare the wear resistance of silicon coatings vs. stainless steel. We found that "softer" coatings can be wear resistant.
In this blog post you will learn:
- How wear resistant coatings compare.
- Compare the hardness of various coatings and surfaces.
- Discuss why some wear resistant coatings are not necessarily hard.
|
Nanoindentation Hardness Testing Background
Test coupon samples were submitted to Penn State University’s Materials Characterization Lab for nanoindentation testing. The lab subjected the samples to nanoindentation hardness testing to obtain the coating hardness and elastic modulus properties.
A total of eight 316 stainless steel sample coupons were analyzed, including two for each coating and two uncoated samples as baseline reference. The coupons all have a mechanically mirror-polished side and a standard machine-finished side. The polished side is used for the nanoindentation test.
The eight test coupons consist of three coatings, two coupons per coating, Silcolloy® 1000 (SL1000), Dursan® and an experimental coating we'll call RD5. In addition, two uncoated 316 stainless steel coupons were tested as baseline samples.
The nanoindentation test reports hardness and elastic modulus values for each sample. In the case of the coated samples, the mechanical properties of each individual coating are measured and reported.
In the case of the uncoated samples, the mechanical properties of the stainless-steel substrate are measured and reported. Silcolloy 1000 was found to have the highest hardness and elastic modulus values among the three coatings.
Want to keep up with the latest in material science? Click the box below to subscribe to our emails and blog.
Experimental:
Samples were tested using a Bruker Hysitron TI-900 nanoindenter with a standard Berkovich tip made of diamond. The Berkovich indenter is a three-sided pyramid with a half angle of 65.3°, measured from the indentation vertical axis to one of the pyramid flats, as shown in Figure 1.2
The shape of the indentation left by a Berkovich tip is also shown in Figure 1. In order to exclude substrate interference, the indentation depth was controlled to be no more than 10% of the coating thickness. The coating thicknesses for the six coated samples varied between 700-900 nm, so test indents were performed first to determine the corresponding load value for each sample type to reach about 70 nm of indentation depth (including the uncoated control samples to be consistent).
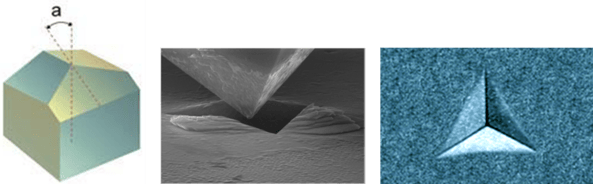
Figure 1: A Berkovich tip with “a” denoting the half angle,2 and the indentation shape it leaves on the surface of the testing specimen3,4
Each sample was indented on the polished side in 2 areas near the center, in a 5x5 XPM load function (a matrix that takes 25 individual measurements), giving 50 data points per sample, and a total of 100 data points per coating type including the bare stainless-steel metal. Click the box below to learn more about how SilcoTek can solve your toughest material problems.
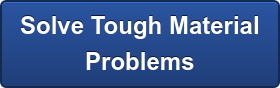
In nanoindentation, the hardness of the testing specimen is defined as peak load / contact area, where the contact area (Apml) is the projected area of contact at the maximum load, as illustrated in Figure 2 below. This area can be calculated from the load-unload curve using an analytical model developed by Oliver and Pharr, without the need to directly measure the area with a microscope.6
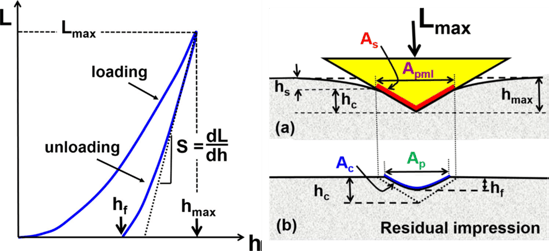
Figure 2: left - The load (L) vs. displacement (h) curve during the load-unload stage of a nanoindentation test, where hf is the final residual penetration depth when a zero load is reached during unloading. The slope of the upper portion of the unloading curve can be used to determine Young’s modulus; right (a) specimen deformation at the maximum applied load Lmax and (b) residual plastic deformation after complete unloading6
Results and Discussion
The load vs. displacement nanoindentation curves for the eight samples were plotted. The example of a nanoindentation curves for 2 Silcolloy coated stainless steel coupons in Figure 3 below shows the plotted nanoindentation curves for each of the 50 data points per coupon sample.
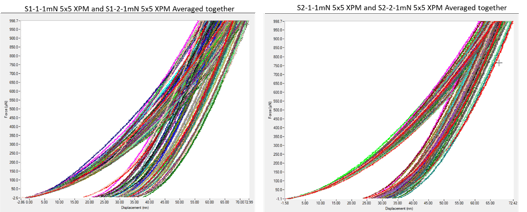
Figure 5: The load (L) vs. displacement (h) curve during the load-unload stage of the nanoindentation test for the two Silcolloy-coated coupons, S1 and S2
Hardness and reduced modulus values, as well as each specimen’s Young’s modulus (i.e. elastic modulus) calculated from the reduced modulus using the equation below are reported in Table 1 (below).
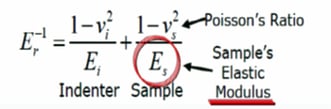
The elastic modulus (Ei) value of 1140 GPa and Poisson’s ratio (ni) value of 0.07 are used for the diamond indenter.6 The Poisson’s ratios for uncoated stainless-steel (0.27), Silcolloy (0.22), Dursan (0.25) and RD5 (0.23) are used based on literature reported values for 316 stainless steel,7 hydrogenated amorphous silicon film,8,9 organosilicate glass coating10 and silicon oxynitride film,11 as RD5 is essentially a silicon oxynitride coating.
Sample |
Uncoated SS |
Silcolloy |
Dursan |
RD5 |
Hardness (GPa) |
4-6 |
12-13 |
4.3-4.4 |
10 |
Reduced modulus (GPa) |
205-209 |
135 |
30-31 |
98.5 |
Sample’s Young’s modulus (GPa) |
231-237 |
145.6 |
28.9-29.9 |
102 |
Table 1: Hardness, reduced modulus and corresponding Young’s modulus calculated from the reduced modulus for the three SilcoTek CVD coatings and the bare SS substrate
Table 2 (below) summarizes a comparison of the three SilcoTek CVD coatings with a number of literature-reported hard coatings. It shows that SilcoTek’s CVD coatings are generally lower in hardness and modulus values, meaning they are softer and less stiff, than the commonly used hard engineering coatings such as DLC (diamond-like carbon) or titanium-based coatings. Those coatings are usually used in mechanically demanding applications such as metal cutting, tooling, automotive and aerospace where they can help reduce abrasive wear and improve lifetime of the components.
Sample |
Uncoated SS |
Silcolloy |
Dursan |
RD5 |
PECVD silicon oxynitride11 |
PVD TiO2 film13 |
PVD DLC14 |
PVD TiN film16 |
Titanium carbide film17 |
Diamond film14 |
Hardness (GPa) |
4-6 |
12-13 |
4.3-4.4 |
10 |
4.7-9.7 |
4.8-16.1 |
12-30 |
22 |
23-29 |
80 - 100 |
Young’s modulus (GPa) |
231-237 |
145.6 |
28.9-29.9 |
102 |
76.8-89.2 |
114.4-139.3 |
62-213 |
426 |
600 |
500 - 533 |
Table 2: Hardness and Young’s modulus value comparison with a number of literature-reported hard coatings. The broad range of values for some coatings highlight the impact of deposition conditions on coating’s mechanical properties.
Wear Resistance Testing Results
One interesting finding from this study is that Silcolloy®, our hydrogenated amorphous silicon coating, appears to be the hardest coating offered by SilcoTek. This is contradictory to the notion that Dursan® is our most wear-resistant coating. Pin-on-disk tests below indicate that while Silcolloy had similar wear rate as the bare stainless-steel (oxidized steel shown below), Dursan reduced the wear rate by half.12 This indicates that a Dursan coated stainless steel surface is wear resistant, tough, and durable, but not as hard and wear resistant as DLC or other coatings. Read our previous blog post to learn more about durable and tough surfaces.
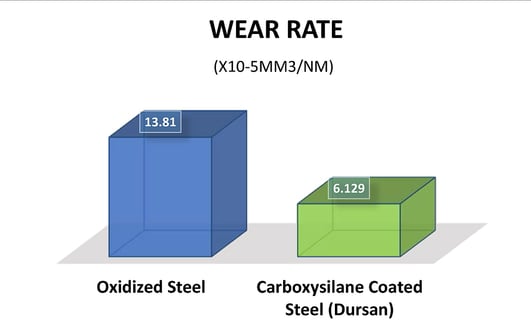
A possible explanation for this may be that in a nanoindentation test (see previous blog post for test details), the force is perpendicular to the surface of the coating and the indenter penetrates directly through the coating material; in a pin-on-disk test, although the force is applied on the pin which is in contact with the coating surface perpendicularly, the coating sample is mounted on a moving stage that creates wear not only in the vertical but also parallel directions to the coating surface. So there are more contributing factors to a pin-on-disk test, such as coating adhesion and coefficient of friction (COF), that are not evaluated in a nanoindentation test.
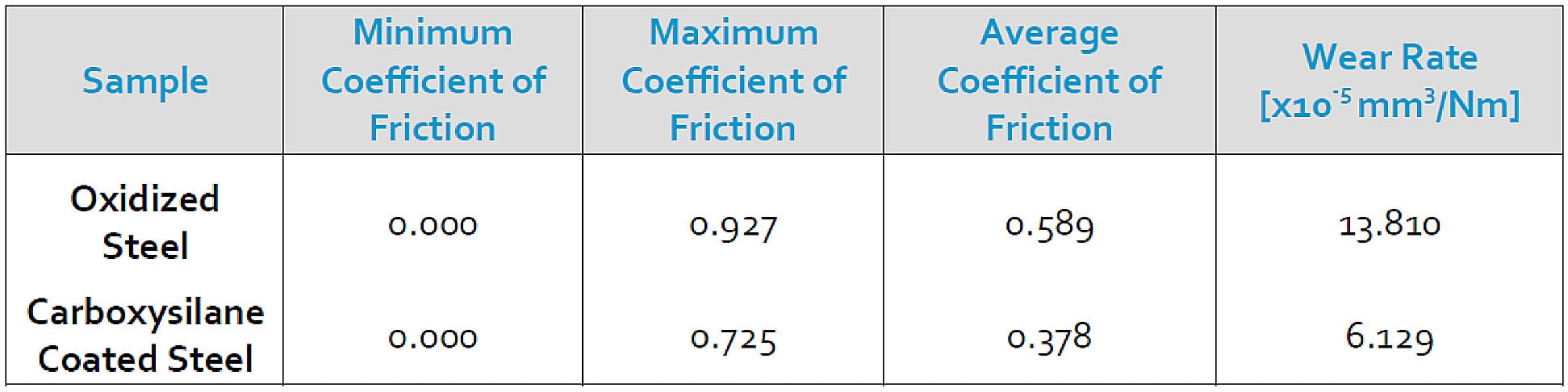
Dursan’s better wear-resistance properties therefore may have more to do with stronger coating adhesion and lower coefficient of friction (perhaps better elasticity too) than Silcolloy, despite that Dursan has lower hardness and Young’s modulus values. Ideally, a coating that combines both high hardness/modulus and strong adhesion/lubrication (such as some DLC coatings) will deliver the best overall anti-wear performance.
Currently we do not have any pin-on-disk data on the research coating RD5, but the SilcoTek Research and Development team plans to conduct more tribological tests on our coatings in 2021 to better understand the mechanical properties that are most needed by SilcoTek’s customers.
High hardness and Young’s modulus are recognized and desirable characteristics for coatings used in mechanically demanding applications. On the other hand, we learned from this study that hardness and Young’s modulus alone do not translate to better wear-resistance. Other factors such as coating adhesion and coefficient of friction also play important roles. As noted in our previous blog post, in some applications a soft but flexible coating material like rubber may fit the needs better than a hard but brittle material like glass.
Summary:
This blog reported the hardness and Young’s modulus values for three SilcoTek CVD coatings: Silcolloy, Dursan and a research coating RD5. The values for uncoated 316 stainless steel substrate were measured and reported here too. Silcolloy, the hydrogenated amorphous silicon coating produced by SilcoTek, exhibits the highest hardness and modulus values among the three coatings. This is contradictory to previous pin-on-disk test that showed Dursan to be more wear-resistant than Silcolloy.
The wear vs. hardness performance difference may be explained by stronger coating adhesion and lower coefficient of friction of Dursan when compared to Silcolloy. More tribological studies are planned for the future. The Marketing team will listen to our customers in order to define the desired properties for the next generation of SilcoTek coatings.
Have a question about how our coatings can improve the material performance of your products? Contact our Technical Service Team or ask our experts on LinkedIn.

References:
- Fischer-Cripps, A. C. “Nanoindentation” 3rd edition, 2011.
- https://en.wikipedia.org/wiki/Berkovich_tip
- https://www.bruker.com/products/surface-and-dimensional-analysis/nanomechanical-test-instruments/nanomechanical-upgrade-options/test-probes.html
- https://www.nanoscience.com/products/nanoindenters/
- Hess, A. E. “Integration of process-incompatible materials for microfabricated polymer-based neural interfaces” Ph.D. thesis, Case Western Reserve University 2011
- Broitman, E. “Indentation hardness measurements at macro-, micro-, and nanoscale: a critical overview” Tribol. Lett. 2017, 65:23
- https://www.azom.com/properties.aspx?ArticleID=863
- Kuschnereit, R. et al. “Mechanical and elastic properties of amorphous hydrogenated silicon films studied by broadband surface acoustic wave spectroscopy” Appl. Phys. A 1995, 61, 269.
- Guo, S. et al. “Internal stress, thermal expansion coefficient and bi-elastic modulus of photochemically vapor deposited hydrogenated amorphous silicon films” Thin Solid Films 1992, 219, 135.
- Li, H. et al. “Determining the elastic modulus and hardness of an ultra-thin film on a substrate using nanoindentation” J. Mater. Res. 2009, 24 (3), 1114.
- Gan, Z. et al. “Material structure and mechanical properties of silicon nitride and silicon oxynitride thin films deposited by plasma enhanced chemical vapor deposition” Surfaces 2018, 1, 59.
- https://www.silcotek.com/blog/wear-resistant-cvd-coating-tests-put-dursan-on-top
- Wiatrowski, A. et al. “Comparison of the physicochemical properties of TiO2 thin films obtained by magnetron sputtering with continuous and pulsed gas flow” Coatings 2018, 8, 412.
- Savvides, N. et al. “Hardness and elastic modulus of diamond and diamond-like carbon films” Thin Solid Films 1993, 228, 289.
- https://www.entegris.com/shop/en/USD/Products/Specialty-Materials/Coatings/Plasma-Enhanced-Chemical-Vapor-Deposition-%28PECVD%29-Coatings/c/plasmaenhancedchemicalvapordepositionpecvdcoatings
- Wu, S. et al. “Hardness and elastic modulus of titanium nitride coatings prepared by PIRAC method” Surface Review and Letters 2018, 25 (4), 1850040.
- Fieandt, L. V. “Cutting edge titianum-based CVD hard coatings” Ph. D. thesis, Uppsala University 2018.