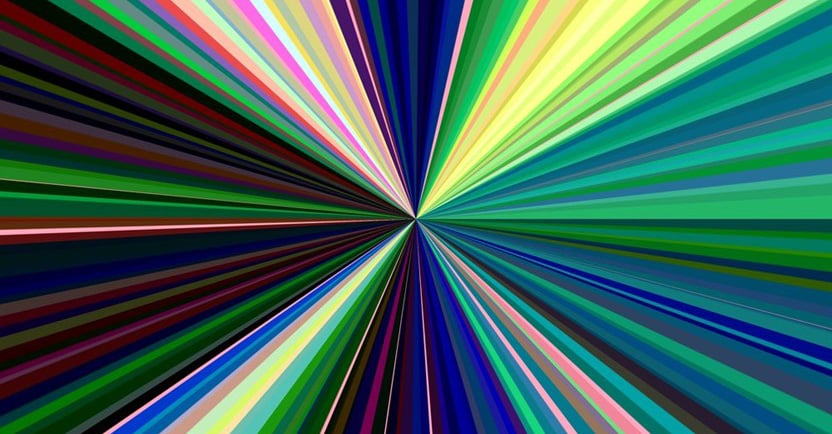
We test our coatings and compare emissivity data. Can coatings reduce the ratio of absorption to emissivity? Read on to find out.
Coatings That Reduce the Ratio of Absorption to Emissivity
Emissivity is a measure of an object’s ability to emit thermal radiation. SilcoTek often gets asked about our coating’s impact on emissivity. In this blog post will discuss how our coatings impact elgiloy (cobalt, chrome, nickel alloy) and its emissivity to solar radiation and compare how our coatings perform.
In this blog post you will learn:
- How emissivity is an important factor in heat flow and thermal calculations
- How SilcoTek coatings performed in emissivity testing.
- How Silcolloy can improve emissivity to adsorption performance.
- How emissivity is measured.
|
About Emissivity
When light hits an object, there are three main mechanisms of interaction:
- Reflection: the light bounces off the surface. In this type of interaction, there is little to no change in the light or the material.
- Transmission: the light goes straight through the material. There is more interaction in this case. The light is often refracted and/or scattered as it passes through the material of interest.
- Absorption: the light is transformed to some other radiant power. Typically, it is transformed into thermal energy or heat. This heat could either be absorbed into the material causing an increase in temperature, or the heat energy could be emitted as visible or IR radiation. Emissivity is a measure of a materials effectiveness in releasing, or emitting, this energy.
Most texts will define emissivity as a number or value (ranging from 0 to 1) given to a material or coating surface when compared to a perfect "black body" at a particular wavelength (emissivity changes with wavelength). A perfect black body has a value of 1, conversely, a surface that is a perfect reflector has a value of 0. For example if a low-e opaque material had an emissivity value of 0.05 at a particular wavelength, the material would reflect 95% of the radiant thermal energy. (Calculated as 1.0- 0.05 = 0.95)
Emissivity is an important variable when looking at heat flow and thermal calculations for materials in a wide variety of industries including aerospace, refining, and electrical work.

Background
Recently a customer was experiencing issues with an elgiloy alloy that was exposed to solar radiation. When in the direct sun, the elgiloy component absorbed much more light energy than it emitted causing it to increase in temperature. When the elgiloy material was not in direct sunlight (such as in the Earth’s shadow), the part would then cool. This heating and cooling were causing expansion and contraction which interfered with the unit’s performance.
Faced with this problem, the customer was left with two options: utilize a very expensive plastic designed to have a coefficient of thermal expansion of zero or find a way to cut the elgiloy’s absorption to emissivity ratio to one, meaning it emits the same amount of energy it absorbs.
Glasses and silicon-based materials are known to increase emissivity due to their relatively broad infrared absorption and emission profiles. Most of SilcoTek’s coatings are silicon-based and should assist in improving emissivity of materials. To confirm our assumption we enlisted Nexolve, a high performance materials provider, to perform experiments on uncoated and coated elgiloy to see the impact of SilcoNert® 1000, Silcolloy® 1000, and Dursan® on the emissivity properties of the metal. This blog will show that all three improved the emissivity of the materials, and Silcolloy was able to reach the goal of an absorption to emissivity ratio of 1.
Interested in testing our coatings in your application? Contact our Technical Service Team to discuss your application. You can test our coatings for free by clicking the box below.

Test Data and Discussion
Elgiloy is often heat treated to stiffen the material for use in aerospace. Nexolve provided coupons of heat treated elgiloy for coating. One was coated in Silconert 1000, a thin hydrogenated amorphous silicon coating, one was coated in Silcolloy 1000, a thicker hydrogenated amorphous silicon coating, and one was coated in Dursan, a hybrid silica material. The coupons were then measured for solar absorptance (absorptivity) using a Perkin Elmer Lambda 950 UV/Vis/NIR spectrometer coupled with a 150 mm Spectralon coated integration sphere and IR emittance (emissivity) using an AZ Technology TEMP 2000A portable infrared reflectometer/emissometer.
The solar absorptivity measurement was done by following ASTM E903 standards. Due to the opaque nature of elgiloy, no transmission was reported. The solar absorptance (αs) and solar reflectance (ρs) values can be found in Table 1. Note that the coated materials all showed less absorptance and higher reflectivity values.
Table 1: Solar absorptance values for bare and coated coupons.
Sample identity
|
Solar Absorptance (αs)
|
Solar Reflectance (ρs)
|
Bare heat treated elgiloy
|
0.7189
|
0.2811
|
Dursan coated
|
0.6265
|
0.3735
|
SilcoNert 1000 coated
|
0.4983
|
0.5017
|
Silcolloy 1000 coated
|
0.6712
|
0.3288
|
Infrared emittance was measured in relative mode to yield hemispherical IR emissivity values. The instrument used, AZ Technology TEMP 2000A, measures the total hemispherical IR emittance (ε) integrated over the spectral range of a 300K blackbody (3000nm-30000nm). The results can be found in Table 2. Note that the three coatings all resulted in higher emittance relative to the uncoated sample, but Silcolloy had the largest impact on emissivity of the sample.
Table 2: IR emittance values for bare and coated coupons.
Sample Identity
|
Hemispherical infrared emittance (ε)
|
Bare heat treated elgiloy
|
0.123
|
Dursan coated
|
0.339
|
SilcoNert 1000 coated
|
0.159
|
Silcolloy 1000 coated
|
0.710
|
The four absorptivity and reflection spectra can be seen below.
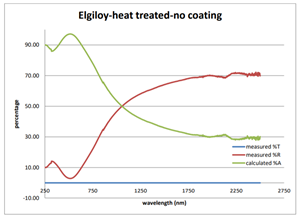
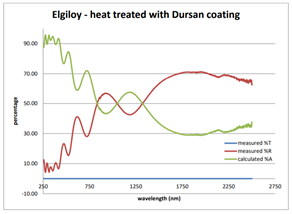
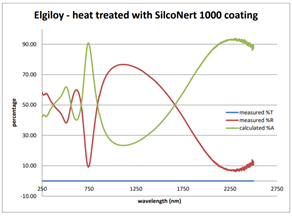
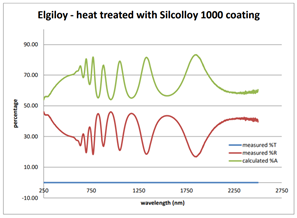
The goal of the coating was to lower the ratio of solar absorption to emittance down to 1 or less. As can be seen in Figure 1, Silcolloy achieved that goal. In any case, the coatings all provided lower absorption, higher reflectance and higher emission of solar radiation which would ease the heating and cooling process these parts might see in space applications.
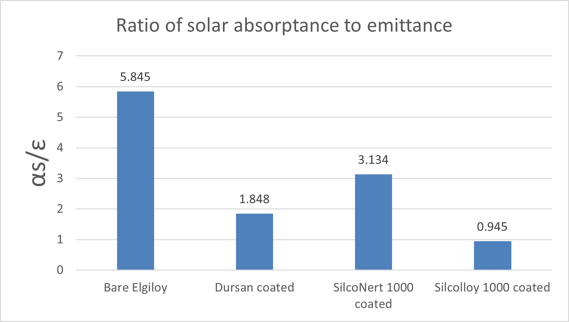
Figure 1: Ratio of solar absorptance to emittance of the bare and coated coupons.
Conclusion
All three coatings can enhance the emissivity to adsorption properties of heat treated elgiloy. One thing to keep in mind when it comes to emissivity of SilcoTek coatings. The substrate they are deposited on will likely play a role in emissivity results. Since our coatings are very thin (Dursan coating was 450 nm, SilcoNert 1000 was 125 nm, and Silcolloy 1000 was 750nm) the solar radiation will penetrate the coatings and interact with the base substrate. These results could be quite different on other metals, such as stainless steel, and it would certainly be different on a ceramic material. In the case of heat treated elgiloy, all three coatings provided a benefit, with Silcolloy 1000 providing the biggest impact to emissivity. To read the entire Emissivity Technical Insight go to our Whitepapers and Technical Insights page or click the link below.

Keep up with the latest in coating technology. Follow us on LinkedIn or subscribe to our emails and blog.
