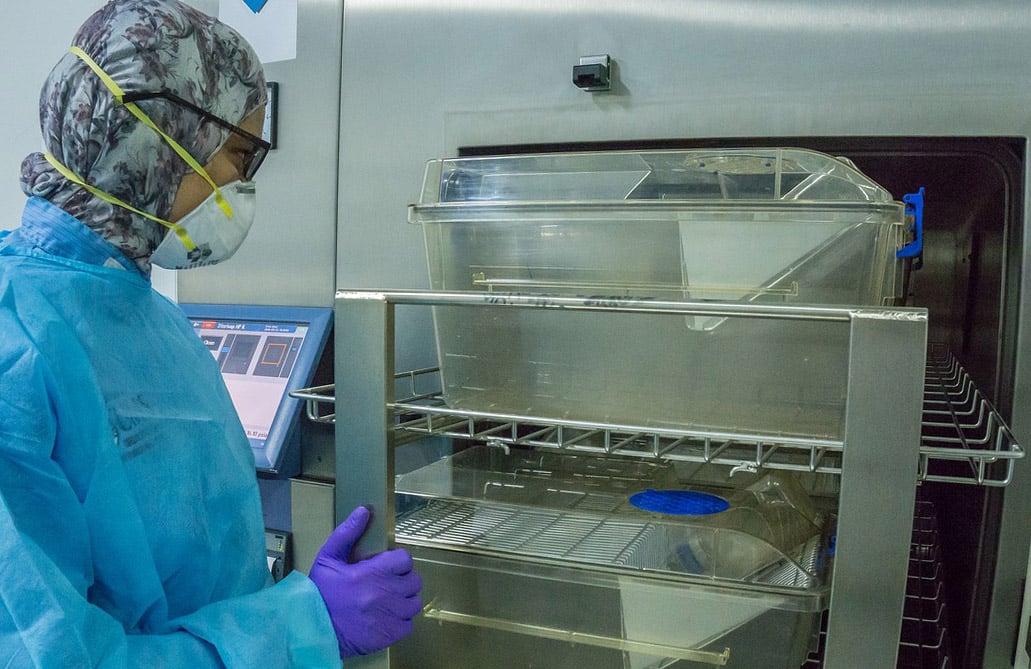
Does steam exposure alter our coating characteristics? We tested our coatings to find out.
Does Steam Exposure Change Silicon Coatings?
Customers asked what is the effect of steam exposure on our coatings. This blog post will report on these effects by measurement of surface thickness, contact angles, and FTIR spectroscopy.
In this blog post you will learn:
- How exposure to steam under autoclave conditions impact our coatings.
- How FTIR measurement techniques can be used to detect changes in thin film coatings.
- How surface contact angle measurement can be used to characterize changes in surface.
- Determine what tools are needed to evaluate a CVD coating for steam exposure.
|
Background
An autoclave is often used to sterilize surfaces by exposing those surfaces to saturated steam over a period of time. Understanding the effect of steam exposure on SilcoTek® surfaces is important since many customers and potential customers may use steam for cleaning and sterilization purposes.
It's also important to note that this evaluation is conducted under high purity, controlled steam environments. Exposing a sample flow path to process steam or steam that contains contaminants or particulates may contaminate the flow path surface or damage the surface. We recommend contacting SilcoTek to discuss your application before exposing your flow path to steam.
In this blog post we'll test our coatings and summarize findings on the effect of autoclave exposure on various surfaces offered by Silcotek. We'll be measuring contact angles, coating thickness, and Fourier-transform infrared spectroscopy (FTIR) as characterization methods to determine how the surface performs under steam exposure. Coated 316 stainless steel coupon samples were used for these characterization methods.
Additional SilcoTek® coated 316L stainless steel coupons were exposed to autoclave conditions and will be evaluated via ASTM G-31 hydrochloric acid corrosion exposure protocol and EIS spectroscopic analysis. Results of those tests will be discussed in a future blog post.
Want to learn more about our coating and how they can improve the performance of your products? Click the box below to subscribe to our email and blog updates.

Experimental
The coatings/treatments evaluated for autoclave exposure were:
6 Coupons of each treatment were prepared per SilcoTek standard processes (or per the latest optimized processes per Research and Development for Notak and RD5).
Tests were conducted using SilcoTek coated 316L stainless steel coupons for a total of 42 samples.
Six (6) 316L corrosion coupons were also coated with each of the following: Dursox, Dursan, Silcolloy and RD5 for a total of 24 corrosion coupons. After treatment, the following baseline measurements were made on all coupons: DI water contact angle, hexadecane contact angle (for Notak coupons only), thickness (via Filmetrics F40 spectrometer) at the general center of the coupon, and FTIR spectroscopy. ASTM G-31 and EIS corrosion characterization will be conducted and evaluated at a later date.
After our baseline testing, half of the coupons, three from each process for a total of 33, were sent to Namsa in Northwood, Ohio for autoclave exposure. All coupons were treated simultaneously in one chamber with the following conditions of exposure:
- Cycle Type: Gravity
- Exposure Pressure Range: 16.4-17.8 psig
- Conditioning Time: 10 minutes, 7 seconds
- Exposure Temperature Range: 121.0-123.2°C
- Exposure Time: 60 minutes
- Total Cycle Time: 1 hour 10 minutes 40 seconds
The treated coupons were returned to SilcoTek and recharacterized using the same measurement evaluation techniques prior to autoclave exposure.
Data and Discussion
Contact angle evaluation
Table 1 illustrates changes in contact angles of seven different SilcoTek surfaces after exposure to standard autoclave conditions. Silcolloy, which is an unfunctionalized amorphous silicon deposition had the most dramatic change, with a water contact angle before exposure of 70° to a post exposure contact angle of 29°. The degree of change is not surprising, since Silcolloy has a silicon hydrides at the surface that can be surface oxidized to create Si-O-Si hydrophilic functional groups (moieties), as confirmed in the FTIR data discussed below (Silcolloy is, however, very stable against bulk oxidation).
Table 1: Average contact angle differences, before and after autoclave exposure, with deionized water and hexadecane (Notak only).
Surface
|
DI Water before
|
DI Water after
|
Decrease
|
Hxdcn before
|
Hxdcn after
|
Notak
|
120°
|
120°
|
0°
|
83°
|
82°
|
Silcolloy
|
70°
|
29°
|
41°
|
|
|
Dursox
|
51°
|
40°
|
11°
|
|
|
Dursan
|
88°
|
78°
|
10°
|
|
|
SN2000
|
82°
|
70°
|
12°
|
|
|
SK1000
|
84°
|
75°
|
9°
|
|
|
RD5
|
25°
|
22°
|
3°
|
|
|
On the other end of the scale is Notak. Notak is not a silicon deposition, but a direct functionalization of the substrate surface (316 stainless steel in this case) with organofluoro molecules to provide a stable, low-energy surface which is hydrophobic and oleophobic. (No other SilcoTek surfaces are oleophobic and therefore only Notak was analyzed for hexadecane contact angles.)

For hydrophobicity, the Notak coupons showed no change in contact angle after autoclave exposure. For oleophobicity, the Notak coupons had an average loss of 1 degree after autoclave exposure.
The test coating, RD5, is significantly hydrophilic and showed a slight decrease in hydrophilicity after autoclave exposure. The spread of hydrophilic contact angle measurement values was rather large (13°), however, so the slight decrease after exposure is marginally significant.
The other surfaces, Dursox, Dursan, SilcoNert 2000 and SilcoKlean 1000 all showed similar decreases in water contact angle of 9-12°. For those depositions, there was a small degree of hydroxylation as illustrated in the FTIR data discussed below.
Film thickness evaluation
Table 2: Average thickness (nm) differences, before and after autoclave exposure.
Surface
|
Thickness before
|
Thickness after
|
Variance
|
Silcolloy
|
400
|
380
|
-20
|
Dursox
|
664
|
667
|
3
|
Dursan
|
486
|
506
|
20
|
SN2000
|
215
|
219
|
4
|
SK1000
|
211
|
214
|
3
|
RD5
|
839
|
824
|
-15
|
The measurement of coating thicknesses was accomplished with a Filmetrics F40 instrument. The F40 measures light photon absorbance through the thin film. The absorbance data is compared to known absorbance of various substances in the coating to determine the thickness of the film. The F40 uses spectrophotometric absorbance data to non-destructively measure and compare coating thickness to a sensitivity of 4nm-40um.
Get free evaluation coating test coupons to see how our coatings perform in your application. Click the box below to get your test coupons.

The spot size of the instrument is 10um and is difficult to train on to the exact same spot with repeated measurements. Therefore, measurements before and after autoclave exposure on the exact same spot is unlikely and some variation should be expected since the coating itself may have a significant thickness variance throughout due to thermal uniformity and proximity to other parts and fixturing during deposition. Accordingly, the measurement variances in Table 2 are not considered significant. There was no visible loss under magnification during measurement and the differences listed are considered within the expected variance of the instrument and technique.
Grazing angle FTIR evaluation
Fourier Transform Infrared Spectroscopy (FTIR) spectra were obtained with a Thermo/Nicolet 380 FTIR equipped with a Smart SAGA grazing angle attachment, allowing FTIR spectra of thin films and surfaces on reflective substrates. The following spectra provide FTIR data before and after autoclave exposure for each surface.
During the FTIR test, infrared radiation is passed through the sample. During exposure, some of the IR radiation is absorbed by the coating and other parts of the IR spectrum pass through the coating. The reflected IR spectrum is specific to each coating, making a sort of coating composition fingerprint that is unique to the coating. A change in the FTIR spectra plot from pre and post steam exposure would indicate a change in the coating composition.
Notak FTIR Results
Notak FTIR analysis: There was no significant change in spectra between before and after autoclave exposure for the Notak surface, indicating that Notak is stable under the autoclave exposure conditions used.
Silcolloy FTIR Results
Silcolloy FTIR analysis: Exposure to the autoclave conditions created Si-O-Si molecular characteristics (moieties) visible in the 1050-1250 cm-1 region. This verifies the cause of loss of water contact angle mentioned above.
Dursox FTIR Results
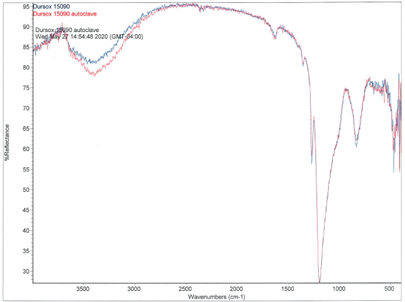
Dursox FTIR analysis: There was little significant change observable via FTIR between before and after autoclave exposure for the Dursox surface. There was a slight increase in Si-OH functional groups (moieties) (a part or functional group of a molecule) in the broad 3400 cm-1 region, accounting for the slight decrease in water contact angle mentioned above.
Dursan FTIR Results
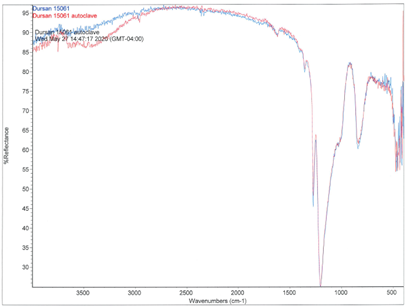
Dursan FTIR analysis: There was little significant change observable via FTIR between before and after autoclave exposure for the Dursan surface. There was a slight increase in Si-OH functional groups (moieties) in the broad 3400 cm-1 region, accounting for the slight decrease in water contact angle mentioned above.
SilcoNert 2000 FTIR Results
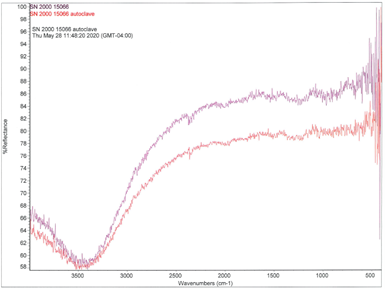
SilcoNert 2000 FTIR analysis: There was little significant change observable via FTIR between before and after autoclave exposure for the SilcoNert 2000 surface. There was a slight increase in Si-OH functional groups (moieties) in the broad 3400 cm-1 region, accounting for the slight decrease in water contact angle mentioned above.
SilcoKlean 1000 FTIR Results
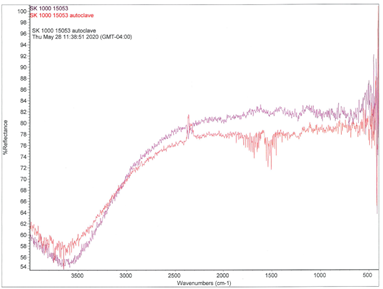
SilcoKlean 1000 FTIR analysis: There was little significant change observable via FTIR between before and after autoclave exposure for the SilcoKlean 1000 surface. There was a slight increase in Si-OH functional groups (moieties) in the broad 3400 cm-1 region, accounting for the slight decrease in water contact angle mentioned above.
RD5 FTIR Results
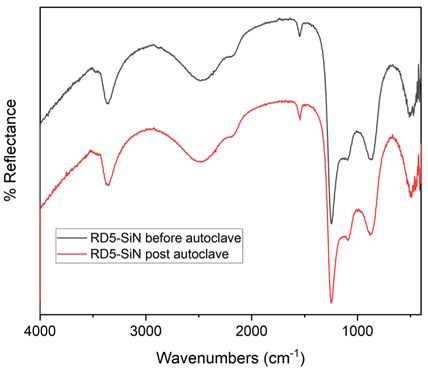
A test coating, RD5, FTIR analysis: There was no significant change observable via FT-IR between before and after autoclave exposure for the RD5 surface, showing RD5 to be stable under the autoclave exposure conditions used.
Conclusions
The exposure of several SilcoTek® surfaces to autoclave conditions revealed the following:
- Notak® surface energy measurements and FTIR spectra were unaffected, signifying excellent resilience to autoclave conditions
- The test coating, RD5, surface energy measurements and FTIR spectra were unaffected, signifying excellent resilience to autoclave conditions
- Dursan®, SilcoNert® 2000, SilcoKlean® and Dursox® showed some sign of surface hydroxylation via autoclave exposure via slight decreases in water contact angle and slight increases in Si-OH functionality via FTIR
- Silcolloy® 1000 was significantly surface-oxidized by autoclave exposure, with a substantial decrease in water contact angle and a measurable increase in Si-O-Si absorbance via FTIR data.
- None of the SilcoTek depositions revealed any significant loss of coating thickness after autoclave exposure.
Further testing on the effect of autoclave exposure on the corrosion resistance of Silcolloy, Dursan, Dursox and RD5 coatings will be reported at a later date.
Have a question about our coatings or want to evaluate a coating? Get a free consultation with one of our coating experts. Just email us by clicking the link below.
Want to learn more about our coatings? Go to our Frequently Asked Questions page, read our informative coating e-books, or follow us on LinkedIn.
