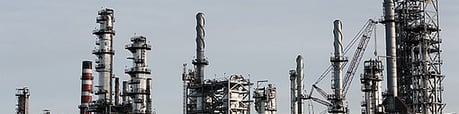
Learn how SilcoNert coated sample paths can improve emissions monitoring of Sulfur, SO2, H2S and VOC detection in refinery, process, stack, CEM, and flare sampling systems.
Reliable Emissions Monitoring and Subpart Ja Flare Sampling
Emissions monitoring regulations mandate chemical process, refinery, flare, and stack detection limits as low as 8ppm. 40 C.F.R. 60.100 Subpart Ja in particular makes reliable and robust sampling and analysis of emissions more essential than ever. Without SilcoNert® 2000 coated sampling components; adsorption into the stainless steel sampling flowpath would make measurement of trace sulfur species, like H2S and SO2, and VOCs nearly impossible.
In this blog post you will learn:
- How silicon coatings, like SilcoNert® and Dursan®, can improve sulfur detection in stack, flare, and chemical process monitoring applications.
- How SilcoTek® coatings can improve volatile organic compound (VOC) detection and improve system reliability.
- How silicon coating can improve both corrosion resistance and trace level detection by making surfaces inert.
|
Refineries for the most part have implemented Subpart Ja compliance programs. Refiners must reduce SO2, NOx, H2S and other emissions significantly in major sources, including:
- Fluid Catalytic Cracking Units
- Fluid Coking Units
- Delayed Coking Units
- Fuel Gas Combustion Devices
- Flares
- Sulfur Recovery Plants
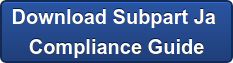
Flare systems are complex, Subpart Ja and associated regulations narrow operating parameters of systems and mandate compliance when existing systems are modified. Modifications include:
- Any new piping from a refinery process unit or fuel gas system physically connected to the flare.
- A flare is physically altered to increase the flow capacity.
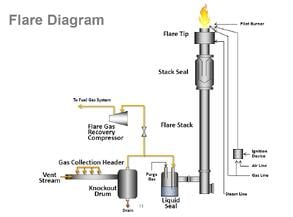
SilcoNert® 2000 coated probes, tubing, valves, fittings and analyzer components assure robust sampling & compliance. SilcoNert 2000 prevents adsorption of Subpart Ja regulated gases like SO2, H2S, NOx, CO and volatile organic compounds (VOCs).
Let's review some data to show how SilcoNert can improve sulfur response.

Sulfur Testing
We compared coated and uncoated sample pathways and measured the signal response and signal stability. The graph below compares the relative response of uncoated stainless steel and SilcoNert coated stainless steel flow paths. The SilcoNert coated pathway offers faster response and dramatically improves signal stability.
Exceptional inertness makes Subpart Ja compliance possible.
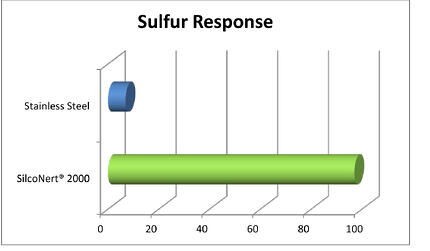
Looking further into absolute response time, the SilcoNert® 2000 dramatically improves sulfur detection and response. Sulfur response in a relatively short 100ft length of tubing (below) can be reduced from hours to seconds by coating wetted flow paths with SilcoNert 2000.
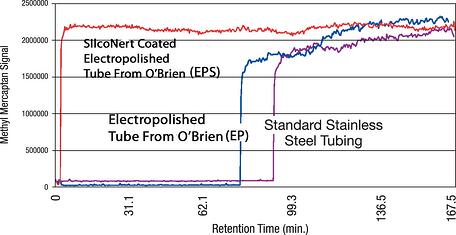
VOC Measurement
Selecting inert and durable materials for sampling critical flowpath surfaces can be a key factor in successful analysis. Mr. Stefan (S.T.) Persijn of VSL, Dutch Meterlogical Society, (in conjunction with the German Meterological Office, DWD) presented a comparative study of adsorptive properties of various materials commonly used in VOC analysis.*
Read The VOC Presentation
The study exposed various tube surfaces to methanol at 50 and 100°C and measured adsorption rate of the surfaces. Results show that an inert coating like SilcoNert® coated stainless steel prevented adsorption and reaction with VOCs in critical flow paths. The study summary, below, highlights the comparative results:**
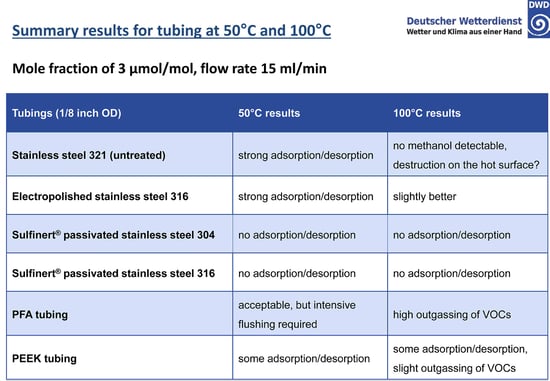
The untreated stainless steel readily adsorbs active compounds with complete loss of methanol. Electropolishing will smooth the surface and reduce overall surface area but adsorption is still significant. PFA and PEEK tubing require careful management of the surface in order to achieve acceptable results. SilcoNert (in this study called by our other trade name, Sulfinert® ) coated stainless steel does not adsorb active compounds because the inert silicon CVD surface bonds to and diffuses into the stainless steel substrate, preventing interaction with reactive sites.
The Key VOCs team completed a major volatile organic compound (VOC) study funded by EURAMET, the Meteorological Observatory Hohenpeissenberg of DWD (the German Meteorological Service) and partnered with the European Metrology Research Programme. Their final report on VOC analysis, "Metrology for VOC Indicators in Air Pollution and Climate Change" is helping to advance the science of trace VOC measurement.**

The team developed test methods to quantify sources of VOC interaction and loss. The project identified suitable materials that prevent adsorption of VOCs and improve measurement techniques. The team also developed sensor based measurement systems for key VOCs in air. The Key VOC team chose SilcoTek® coatings for their study because we offer the expertise, support, and inertness needed to provide an inert sample flow path for highly reliable trace VOC analysis.
Methanol Comparison
The VOC team then compared 10 meter lengths of SilcoNert 2000 coated and uncoated stainless steel tubing (below). The team passed a 180 umol/mol methanol mixture through a bypass (grey areas), then switched to the test tubing. They measured the time to achieve baseline concentration for each tube. The SilcoNert coated tube took less than a minute to stabilize (graph B) compared to over 40 minutes for the stainless steel tube (graph A). The comparison demonstrates the severe adsorption of trace methanol on stainless steel flow path surfaces and highlights potential delays in response that can lead to significant data reliability issues when conducting trace VOC analysis.**
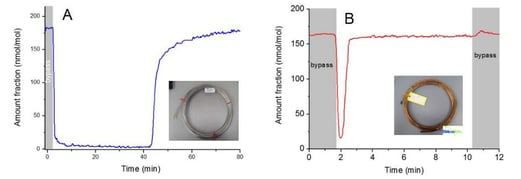
Overall the least methanol adsorption was observed for polymer sampling lines (like PTFE, and FEP) but porosity/permeability, high temperature stability and durability issues limit their effectiveness in the field. It was found that at elevated temperatures (50 to 100c) polymer tubing emitted trace compounds which can lead to unwanted or spurious signal peaks. The SilcoNert coating is stable to 450C and emits no trace compounds during heating.

The study stated: "The adsorption by most polymers such as PTFE and FEP is extremely low, while for uncoated metals it is very high. Coated stainless steel with Silconert-2000 and Sulfinert are the preferred choice, as they also have the benefit of being robust non-permeating materials."
Corrosion Resistance
SP12 is a special process for SilcoNert® 2000 that was developed for aluminum substrates. It has the same external surface chemistry as standard SilcoNert, but with an additional treatment underneath to overcome the undesirable reactions induced by aluminum. The SP12 process can also be applied to stainless steel substrates successfully.
On aluminum substrates, the primer layer in SP12 not only made a visible improvement in the coating’s cosmetic appearance, but also enabled superior corrosion performance in diluted HCl and salt water environments for both aluminum and stainless steel substrates. This is because the primer layer effectively suppresses abnormal silicon growth on aluminum and promotes a smooth conformal coating, leading to greater bonding strengths and higher surface coverage.
On stainless steel substrates, both SOP and SP12 coating processes form nice conformal coatings and there is no visual disparity between the two versions. Several corrosion tests were carried out to probe any potential differences. Figure 5 illustrates EIS (Electrochemical Impedance Spectroscopy) data over 27 days for coated stainless steel coupons exposed to 5% NaCl solution.
Want to learn more about how SilcoTek can improve the corrosion resistance of your products?
Get Our Latest Corrosion
Solutions Presentation
EIS is a largely non-destructive tool to study and evaluate the performance of protective coatings on metal substrates. A good barrier coating usually displays excellent linearity of increasing impedance vs. deceasing frequency and a very high impedance value at low frequencies (i.e. the higher the impedance value, the more resistance by the coating to the solution permeation). While both coatings showed good stability over 27 days and minimal EIS changes, the primer layer in SP12-SN2000 does appear to contribute to better linearity and higher impedance values, correlating with superior barrier properties.
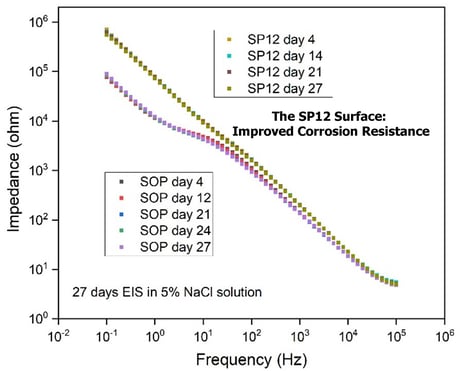
Figure 5: EIS comparison of SOP vs. SP12-SN2000 coatings on stainless steel over 27 days of exposure to 5% NaCl solution
Potentiodynamic polarization resistance scan is another accurate and rapid testing technique commonly used in real time corrosion monitoring of metallic samples. This test can report the corrosion rate of the system at the time of the measurement.
Figure 6 shows a comparison between the two coatings on 304 stainless steel substrates after immersion in a 5% hydrochloric acid (HCl) solution. The data shows performance at the start of the test and after 48 hours of immersion. The primer layer in the SP12-coating again appears to have some benefit in reducing the corrosion rate and slowing down the degradation over 48 hours of HCl exposure. The same test was performed on coated 316 stainless steel substrate as well, and similar results were observed.
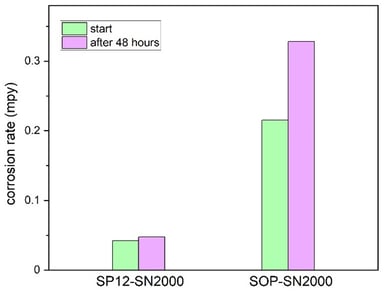
Figure 6: Polarization resistance comparison of SOP vs. SP12-SN2000 coatings over 48 hours of exposure to 5% HCl solution
A more aggressive corrosion test was carried out by immersing testing coupons in 6M (18.5%) HCl solution for one week (168 hours) per ASTM G31 protocol. Figure 7 shows that although both coatings reduced the corrosion rate by about 4x in comparison to the uncoated control coupons, they performed similarly to each other in this test. The primer layer that showed benefits in slower and milder corrosion environments previously (i.e. 5% NaCl solution and 5% HCl solution) did not seem to make a significant impact in a more aggressive environment.
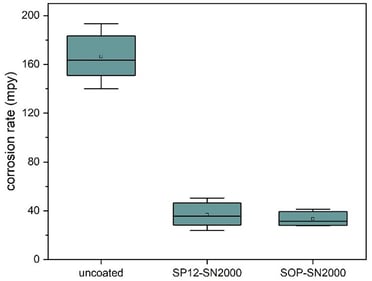
Figure 7: Corrosion rate comparison of uncoated 316L SS corrosion coupons vs. SOP and SP12-SN2000-coated 316L SS corrosion coupons over 168 hours of exposure in 18.5% HCl solution
To make sense of this, an analogy may be made between the primer layer and a very thin but dense barrier wall. When the corrosion force is small and gradual like water permeation, the wall adds measurable protection to the substrate underneath it. However, when the corrosion force is heavy and vigorous, like a hammer or tide pounding on the wall, the wall is simply too thin to hold up and will break and succumb at some point, showing negligible impact under these conditions. For this reason, we recommend Silcolloy® or Dursan® for aggressive corrosion applications such as this.
Want to learn more about how SilcoTek can improve environmental sampling, stack, and flare analysis? Follow us on LinkedIn or subscribe to our email and blog.

*Gierschner, P., Kuntzel, A., Reinhold, P., Kohler, H., Schubert, J.K., Miekisch, W. Journal of Breath Research. 2019. 13, 046006.
**Images and data courtesy of The Dutch Metrology Institute (VSL) and the German Meteorological Office (DWD) presented at the Key VOC joint project April 21st 2016, in Paris, France.