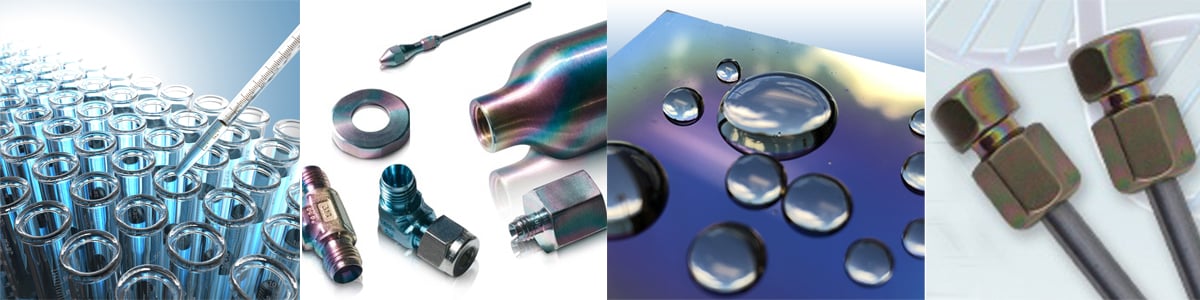
Dursan non-reactive coating passed the demanding USP class VI testing. So what? We discuss why USP Class VI compliance is important.
Dursan Passes USP Class VI Testing. Why is That Important?
In this blog post you will learn:
- Get details about how surfaces are tested for bio-toxicity.
- How Dursan® performed under USP Class VI test conditions.
- Why it's important for silicon CVD coatings to be USP Class VI compliant.
|
About USP Class VI
The United States Pharmacopeia and National Formulary (USP-NF) is a non-profit organization responsible for testing materials (usually single use plastics) for bio-toxicity. The goal of the testing is to be sure no toxic materials will be extracted when a product comes in contact with human tissue or injectable drugs or other products manufactured relating to healthcare, pharmaceuticals, or medical devices.
Class VI testing has the most stringent criteria and involves 3 tests that evaluate reactions for toxicity in tissue. Passing the test means the material is not toxic and does not leach potentially harmful substances into fluids or tissue.
How Dursan Performed
Dursan® passed all toxicity tests while maintaining superior inertness, durability, and corrosion resistance. Dursan exhibited no additional reaction or toxicity when compared to an inert blank sample. You can view the results and Class VI certification by going to our Certification and Compliance page. Or you can click on the box below:

Why is USP Class VI Certification Important?
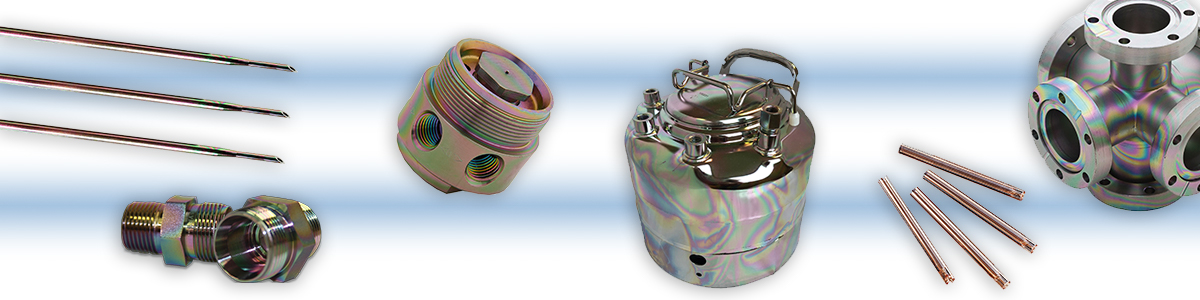
There are plenty of silicone products and other medical grade plastics that are USP Class VI compliant. There's even a silicon carbide surface that's compliant and various release agents used in the manufacture of silicone plastics are compliant. But Dursan® is one of the first CVD silicon coatings to achieve USP Class VI compliance.

Why is that important? Because silicon (think semiconductor chip material) applied by chemical vapor deposition (CVD) allows complete coverage of surfaces both internally and externally. CVD coatings can be economically applied to components like fittings, tubing, fritted filters, needles, and most complex or small bore components. The result is a non-toxic bio-inert surface that is USP Class VI compliant.
Coating Benefits
Coatings like Dursan prevent protein binding and carryover in analytical systems and prevent system cross contamination while improving corrosion resistance and durability. Dursan can be applied to more durable base materials (like stainless steel) to improve inertness performance over less durable materials like PTFE.
SilcoTek® coatings offer major improvements to inertness in sampling systems. But keeping your flow path inert may not be the only issue to consider. If the sample or sample environment is corrosive, abrasive, or otherwise extreme you'll want to consider other benefits our coatings offer.
Bio-Inertness:
Medical device manufacturers, diagnostic equipment and LC instrumentation used for protein analysis benefit from the durability and unmatched chemical inertness of Dursan® coated stainless steel and glass. Inert silicon surfaces allow for improved recovery of compounds over standard deactivation methods as seen in the test results below.
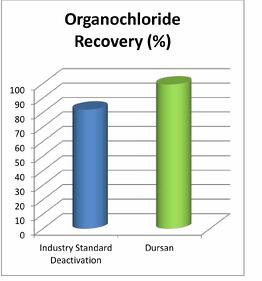
For bio-compatibility, confidence, and consistency, use Dursan® on new or existing components.
The protein-resistant properties of Dursan were studied using quartz crystal microbalance with dissipation monitoring (QCM-D), and compared to that of bare stainless steel and a Teflon-like fluoropolymer coating (AF1600).
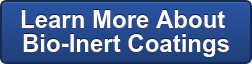
With the assistance of a nonionic surfactant-containing wash solution, Dursan® was found to facilitate 100% removal of adsorbed proteins (BSA, mouse IgG and NHP), whereas these proteins remain adsorbed on the bare stainless steel surface under the same conditions.
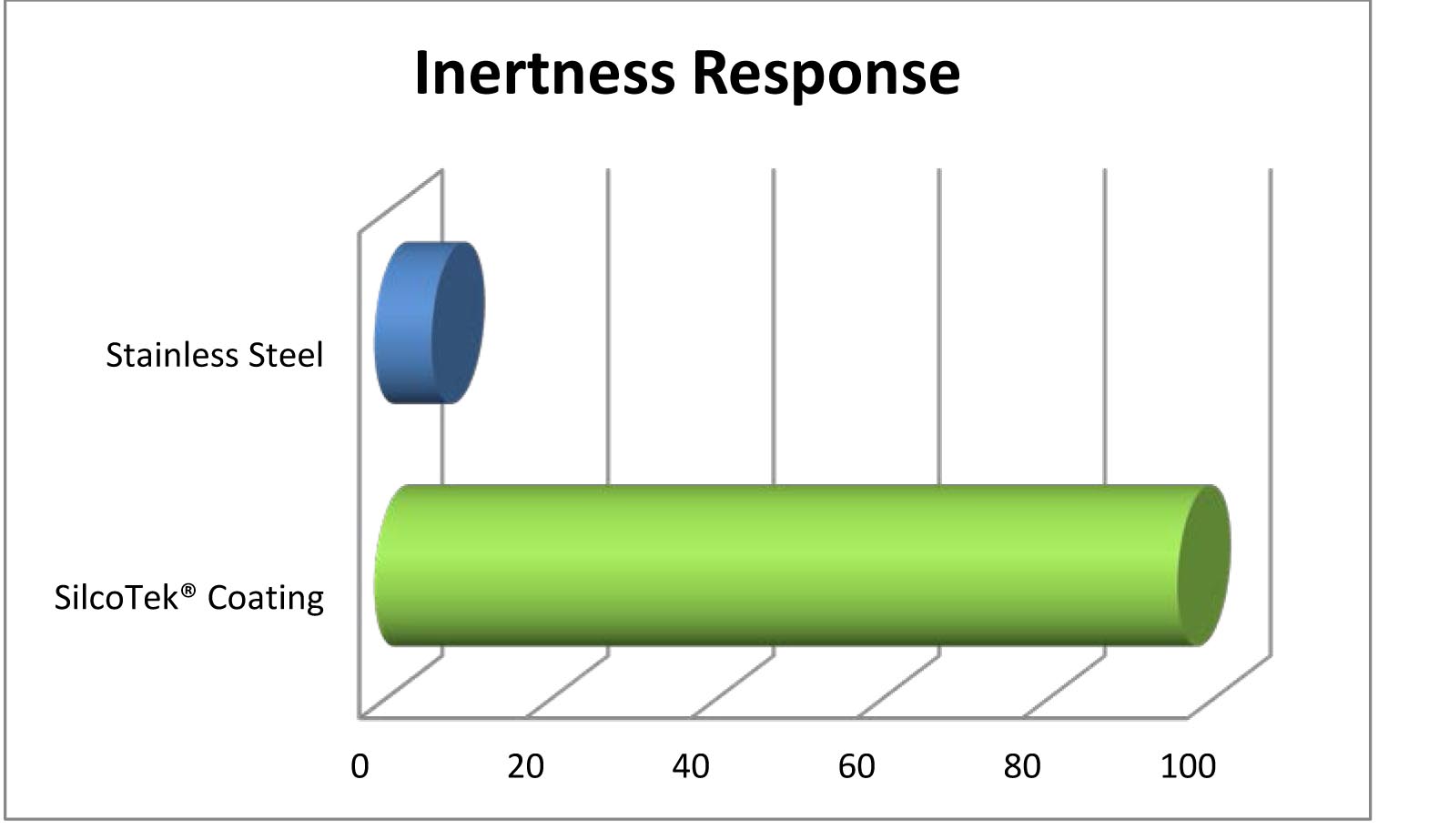
Use Dursan® on a wide range of biotechnology equipment:
- HPLC columns and hardware
- Medical diagnostic equipment
- Biomedical devices
- Needles
|
Corrosion resistance:
Coating the entire sample flow path with an inert silicon coating like Dursan®, helps to prevent formation of adsorptive instrument corrosion particles and increase the life of the sample system. Rust particles can be tremendously adsorptive, the presence of even a small amount of rust can reduce sampling accuracy, increase calibration failures, and distort peaks. All of which will require more analyst time and money to resolve. The Dursan coating technology improves corrosion resistance by orders of magnitude compared to uncoated stainless steel.
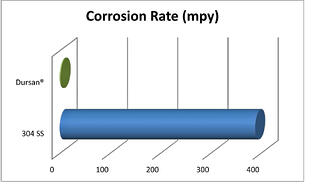
Instrument probes, tubing, fittings, filters, and regulators exposed to corrosive sampling streams can be made both inert and corrosion resistant by coating the wetted surfaces with Dursan®.
Dursan® prevents sampling component damage and contamination throughout the analytical flow path. Dursan can coat the ID of the smallest needles, improving durability and preventing protein binding to stainless steel surfaces. Bleach immersion testing below demonstrates the superior corrosion resistance of Dursan over uncoated or other coating surfaces.
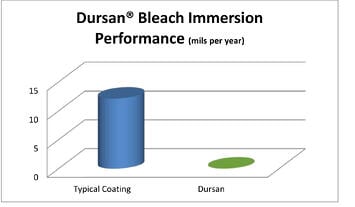
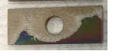 |
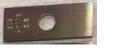 |
Typical coating after bleach exposure |
Dursan after bleach exposure |
Wear and lubricity:
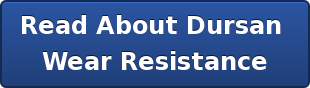
Applications like needles, slider valves or rotating valves can bind under stress; damaging the sampling tool and exposing potentially active sites to your sample and reducing sample accuracy. Dursan® significantly reduces sliding friction and binding, preventing binding or damage to flow path surfaces.
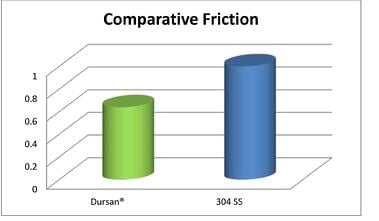
Wear resistance is also improved. Stainless steel surfaces are relatively soft and can erode over time. Erosion can expose potential active sites and reduce system life. SilcoTek's chemical vapor deposition process incorporates a durable coating into the stainless steel surface, enhancing both inertness and durability. While Dursan is not suitable for extremely abrasive environments, the coating will improve durability in particulate rich environments.
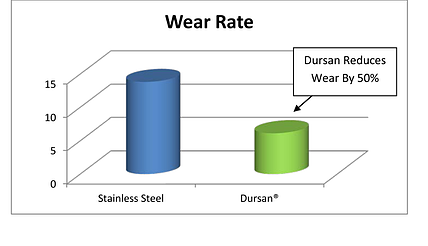
Extreme Temperatures:
Inert surfaces like PTFE can quickly degrade when exposed to temperatures above 250°c and will become brittle in cryogenic environments. Sampling cryogenic liquids or exposure in high temp reactors can easily exceed the capabilities of PTFE and other coatings. SilcoTek® offers inert coating solutions for environments ranging from -270°c to 1000°c, allowing accurate sampling without damaging the sampling pathway.
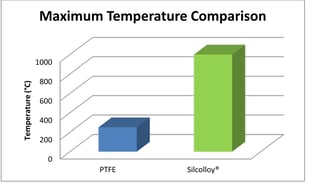
Watch our freeze test video:
Have a bio-inert coating question? To learn more about how Dursan can improve bio-inertness contact our Technical Service Team or follow us on LinkedIn.
