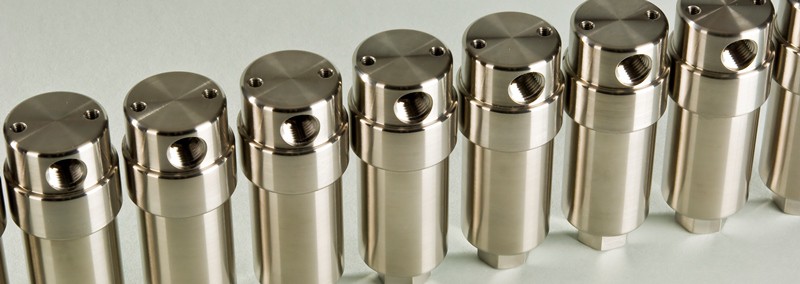
Sintered metal filters and alloy filter media are popular for their high temperature capability and durability, but they're prone to corrosive attack which can shorten filter life and lead to process fluid contamination. In this blog post we discuss how to improve metal filter corrosion resistance.
Industrial filter applications often utilize metal filters because of environmental conditions (extreme heat or cold), extreme shock and vibration, and for added resistance to solvents, corrosives, and other industrial fluids. However, even alloy filters can fall prey to corrosive attack. In this blog post we'll focus on how to improve the corrosion resistance of metal filters.
In this blog post you will learn:
- How CVD coatings can improve corrosion resistance without significantly impacting filter tolerance.
- How SilcoTek® coatings perform under severe corrosive conditions
- How the SilcoTek coating process penetrates metal filter elements without fouling the filter.
- Steps to take in order to improve filter corrosion resistance.
|
Filter background: 3 Things that can kill a filter.
In a previous blog, we discussed 3 factors that can kill a filter. Frequent filter replacement, contaminated product, analytical test failures, and sub par flow performance are all symptoms of 3 basic filter problems.
1. Corrosion
Corrosive fluids may attack the filter, causing damage and eventual failure of the filter element. Corrosion will not only compromise the function of the filter, but will also contaminate the stream passing through the filter. For some applications, metal ion contamination from a metallic filter is a major concern, whether or not there is measurable corrosion.
2. Surface interaction and contamination
If the media passing through the filter can react with the filter substrate, there can be chemical adsorption and/or catalytic activity that would be detrimental to the process stream. Chemical adsorption by the filter element can result in product quality problems and analytical test failures.
3. Filter occlusion
Finally, and most obviously, all filtration media can eventually suffer from pore occlusion and flow restriction as media builds up within the filter. This would progressively reduce the filtration efficiency and eventually require filter replacement.
Identifying the filtration problem is the easy part. Finding a solution to poor filter performance can be a more difficult, costly, and time consuming problem. Operators usually deal with filtration issues by taking the following steps:
- Replace the filter. Frequent filter element replacement can be expensive and can lead to significant downtime.
- Installing a back flush, reheat, or some other type of particulate mitigation system in an attempt to remove particulates (this can require high capital expense and may not offer a significant benefit)
- Installing an element made of a more corrosion resistant material (this can be a more expensive solution as well because users are forced to use costly corrosion resistant super alloys)
- Installing a filter element made of an inert, non-reactive material to prevent product adsorption or analyte adsorption (this can also be an expensive solution and may not offer the durability needed in a filter element).
Learn how the experts prevent filter fouling problems and manage filter surface energy.

Improving Filter Corrosion Resistance
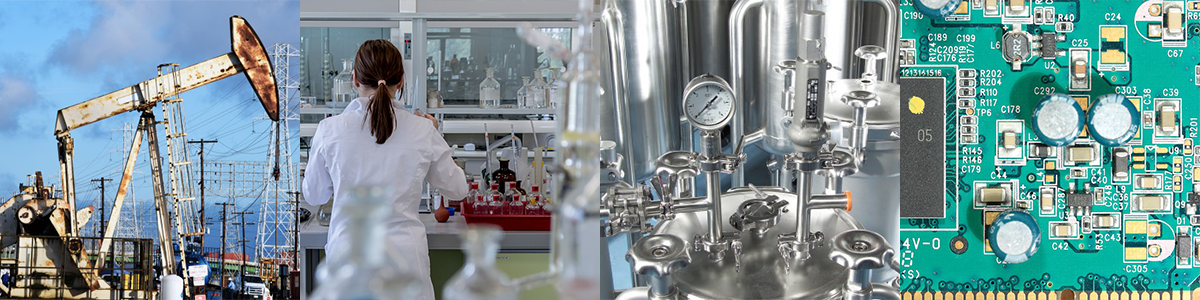
Now that we've discussed some of the issues that can lead to filter failure, let's discuss in detail how to manage metal filter corrosion. 304 or 316 stainless steel is the go-to material for metal filters but if they're rusting out quickly you're faced with some unattractive options to address the corrosion problem:
1. Frequent replacement. As noted above this can disrupt operations and become costly pretty quickly
2. Frequent flushing. Adding a rinse cycle to the filter purge cycle may extend the life of the filter element. I wouldn't get my hopes up too much with this option. Rinsing may only slightly extend the filter life if the system is in continual use.
3. Replace with a corrosion resistant filter made of a super alloy. A great option if you're made of money.
4. Replace with a polymeric filter. This may not be an option if the system operates under a high pressure differential, is exposed to high temperature, or is exposed to extreme shock and vibration.
5. Coat the filter element and filter body with a high durability corrosion resistant coating. You're thinking "won't that plug the filter"? Some coatings will, but a precision CVD silicon coating will stand up to difficult industrial environments and maintain filter tolerance.
How SilcoTek® coatings change the material properties to solve filtration problems
SilcoTek employs a process called chemical vapor deposition (CVD) to apply anti fouling, inert or corrosion resistant coatings to stainless steel, ceramic, or alloy filter surfaces. The benefit of a CVD coating is that the process will allow the coating vapor to penetrate the filter media and coat the internal surfaces of the filter. Because the deposition is so thin, coated filter media aren't clogged or restricted by the coating.

The coated fritted filter cross section below shows how the filter surface is penetrated by the silicon CVD coating. The outer coating layer has the thickest coating which is indicated by a green surface color. The interior surfaces are also coated but with a thinner layer (pink and gold colors). The thinner coating continues to be an effective barrier while allowing the filter to perform without a significant increase in back pressure. SilcoTek applies its coatings via chemical vapor deposition (CVD), which allows all of the filter surface to be covered throughout the entire turbulent flow path. We have performed cross-sectional SEM/EDS analysis of SilcoTek coated metal frits to prove this.
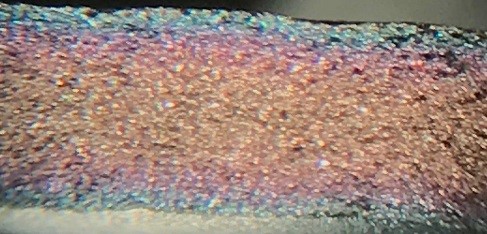
Learn more about how our coating process works and how we coat filters. Read our blog post:
A Dursan coated filter will significantly extend the life of the filter and help to reduce the differential pressure of the filter. The comparative graph below demonstrates how the Dursan coated filter (bottom plot) significantly outperformed the uncoated filters and had less than 1/2 the differential pressure of the uncoated filters after over 10,000 hours of operation.
Corrosion Data for High Temperature Corrosion Resistant Coatings
Dursan® and Silcolloy® are both proven to improve filter corrosion resistance. Silcolloy is a multilayer amorphous silicon deposition that is highly effective at preventing acid corrosion, as well as providing a pure silicon barrier coating, thereby reducing interaction between the metallic filter substrate and the media flowing through the filter. This improves product quality while reducing filter replacement cost.
Dursan is a high durability coating that offers both acid and base corrosion resistance. Both coatings can withstand extreme temperatures and "industrial scale" abuse without failure.
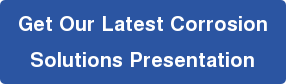
316 stainless steel, Silcolloy coated stainless steel, and Dursan coated stainless steel coupons were immersed into various corrosive liquids for 24 hours. The corrosion rate in mils per year (mpy) was then measured and compared. The Dursan and Silcolloy coated coupons dramatically improved corrosion performance and prevented contamination of the acid. The photo below compares the appearance of the test coupons and acid after immersion. The coated coupons (below center and right) show very little pitting and corrosion and the acid remains clear and uncontaminated.
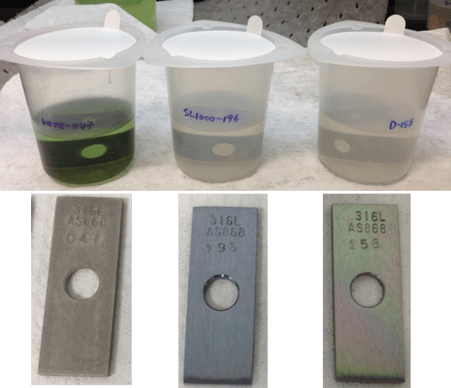
Comparative Data
Corrosion data shows improvement in corrosion resistance by orders of magnitude. We recommend testing our coatings in your application to best assess how our coatings will perform in your application and to apply the best corrosion solution to your problem.
HCL Corrosion Comparison (50C 24 hr immersion per ASTM G31)
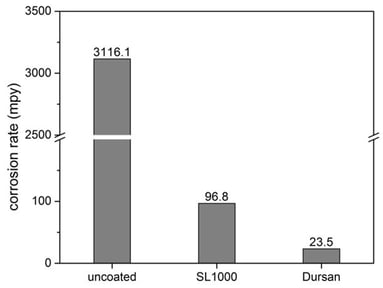
Sulfuric Acid Corrosion Resistance (24 hr ASTM G31)
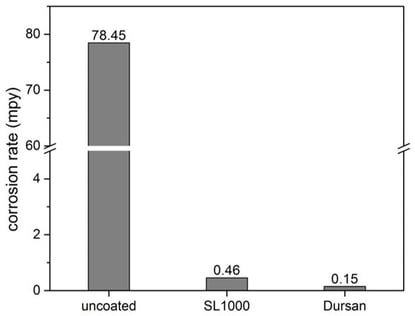
Bleach Corrosion Resistance (per ASTM G31)
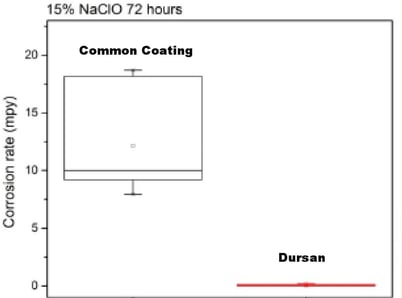
What kind of filters can SilcoTek coat?
The SilcoTek® coating process can accommodate small sintered frits up to filter lengths of approximately 6 feet long in varying diameters. If you have large filters or have large quantities of filters, you'll need to contact our Technical Service staff to discuss the application, dimensions and quantity in order for us to specify the most efficient process parameters for your application.
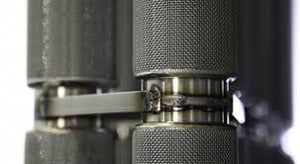 |
SilcoTek is able to coat a wide range of filters and materials including:
- Metal or ceramic filter plates
- Stainless steel and alloy filter housings
|
Summary
A precision CVD coating will improve the corrosion performance of a metal filter anywhere from 2x to 50x or more (depending on application and coating). Environmental factors like filtrate concentration, temperature and vibration can significantly impact the ultimate corrosion resistance of a coated filter. Contact our Technical Service Team to discuss your application. Or join us on LinkedIn to ask the experts about your coating needs.
