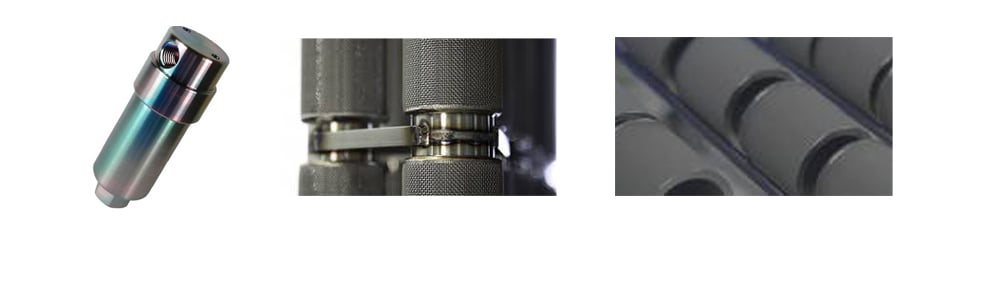
We put metal filters to the test to see if our coatings improve corrosion resistance.
Can SilcoTek Change the Corrosion Game in Metal Filters?
Powder metallurgy offers a variety of advantages over traditional wrought or cast materials. One such advantage, often used in filtration, is the ability to produce materials of controlled and uniform porosity. Corrosion and mechanical properties of sintered materials are typically worse than their wrought counterparts. In the case of stainless steels, corrosion rates can be two or more orders of magnitude worse for sintered materials.1-4
In this blog post you will learn:
- How corrosion rates compare in Hastelloy® sintered and fiber metal filters
- How silicon coatings change the corrosion rate in metal filter material
- How Silcolloy® performed under hydrochloric acid exposure.
|
Background:
Hastelloy® is a specialty alloy developed by Haynes® International that exhibits excellent corrosion resistance in a variety of severe environments. Its superior resistance to halides makes it an attractive material to use in the semiconductor, and other industries where corrosive gases can attack materials such as stainless steel.
This blog will evaluate Hastelloy fritted materials for their corrosion resistance to hydrochloric acid. It was found that the sintering of Hastelloy results in lowered corrosion resistance; however, coating them with Silcolloy can recover the corrosion resistance, and even exceed the performance of wrought material.
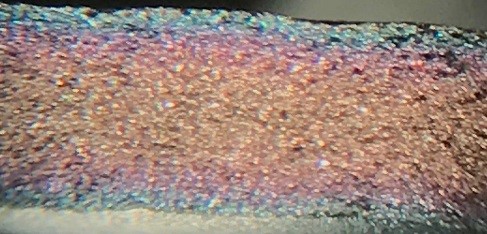
Figure 1: Sectioned photo of a coated fritted stainless steel filter. Hastelloy filter media will have a similar appearance.5
Corrosion Resistant Coating Discussion and Data:
A previous study was conducted by Restek and O’Brien/Cardinal UHP to evaluate the room temperature corrosion of Hastelloy and stainless steel tubing in a 6M HCl environment. They found that tubing made from Hastelloy C-22 had a corrosion rate of 0.673 MPY. For comparison’s sake, O’Brein’s electropolished stainless steel tubing had a corrosion rate of 16.753 MPY.
Read more about how SilcoTek® coating improve corrosion resistance.
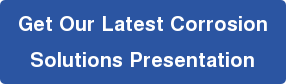
Two sets of sintered C-22 materials were similarly evaluated for room temperature corrosion resistance in 6M HCl. One set is traditional sintered powder media and the other is sintered fiber media. A baseline analysis was conducted of the uncoated filter media. The test was planned for 72 hours to match the tubing study; however, after 24 hours, the colorless HCl solution for both the powder and fiber media turned a dark green, as seen in Figure 2, indicating there were large amounts of metal ions in the solution. This suggests there was an appreciable amount corrosion and weight loss, so the study was stopped after 24 hours.

Figure 2: 6M HCl solution with the uncoated Hastelloy metal filters after 24 hours of exposure. The dark green color indicates a significant amount of corrosion.
The mass loss of the frits was a significant percentage of the starting mass as seen in Table 1. Due to the relatively high surface area of the filter products it was expected to see a higher percentage of mass lost when compared to typical corrosion coupons. The calculation for corrosion rate takes surface area into account:
Corrosion Rate = K*W / A*D*T
Where K is a constant, W is the weight loss, A is the exposed surface area, D is the density of the material, and T is the time of exposure.
Filter media type
|
Percent mass lost
|
Surface Area (m2)
|
Corrosion rate (MPY)
|
Powder
|
1.9%
|
0.187
|
1.4
|
Fiber
|
9.5%
|
0.055**
|
7.1
|
Table 1: Results of the 24-hour 6M HCl exposure of uncoated C-22 Hastelloy sintered filters.
The results show that the powder media is a superior product for corrosion resistance when compared to the fiber. This is not surprising as the processing and production of powder sintered materials is a more mature technology. The other result of note is that the corrosion rates are higher than the corrosion rates of wrought C-22 Hastelloy material from the 72-hour study done by Restek® and O’Brien of 0.673 MPY.
These filters are intended for use in the semiconductor industry for gas delivery applications. Due to the need for little to no carbon contamination, Silcolloy is the preferred coating in that market. Dursan® would be another corrosion resistant coating option for other applications such as sample transport, process sampling, GC analytical, HPLC, or petrochemical/refining applications.
Read more about how SilcoTek coating improve corrosion resistance. Get our Corrosion Application Guide.
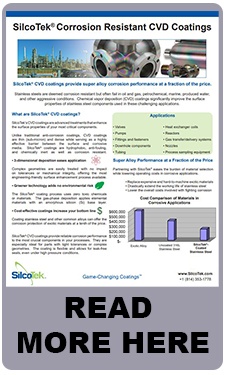
The same filter media were coated with Silcolloy® and again exposed to the 6M HCl for 24 hours. The acid showed no signs of color change over the 24-hour period which suggests little to no corrosion took place. The results can be seen in Table 2. The Silcolloy coating enhanced the corrosion resistance of the powder material 175-fold, and the fiber media by 645x.
Filter media type
|
Percent mass lost
|
Surface Area (m2)
|
Corrosion rate (MPY)
|
Powder
|
0.011%
|
0.187
|
0.008
|
Fiber
|
0.015%
|
0.055**
|
0.011
|
Table 2: Results of the 24-hour 6M HCl exposure of Silcolloy coated C-22 Hastelloy sintered filters.
Conclusion:
The corrosion resistance of sintered materials can be inferior to their wrought or cast counterparts. The need for corrosion resistant sintered materials is important, especially in contamination sensitive applications like analytical, semiconductor, or specialized chemical process and specialty gas delivery systems. Silcolloy coating can dramatically improve the corrosion resistance of C-22 Hastelloy sintered materials. Both powder media and fibrous media showed dramatic performance improvement when coated.
The corrosion values for the coated media are so low that they are close to being within the error of experimental measurement.
SilcoTek has plans to repeat this type of experiment with stainless steel sintered materials. The sintering of stainless steel is a more mature technology, so the corrosion issues may have been solved by adjusting the sintering process, but it will be interesting to see the effect that coating a high surface area porous material such as a frit may have on corrosion resistance. Additionally, there are other industries that utilize sintered materials beyond the semiconductor industry where Dursan would be the preferred coating. Therfore, Dursan will be evaluated alongside Silcolloy for comparative performance results.
Have an idea for a blog post or coating application test? Contact our Technical Service Team or click on our chat box to discuss your idea.
Follow our team on LinkedIn as we explore how our game changing coatings can improve your products.

References:
- E. Otero, A. Pardo, E. Saenz, M.V. Utrilla, P. Hierro, A study of the influence of nitric acid concentration on the corrosion resistance of sintered austenitic stainless steel, Corros. Sci. 38 (1996) 1485–1493.
- T. Raghu, S.N. Malholtra, P. Ramakrisnan, Corrosion behavior of sintered austenitic stainless steel filters in sulphuric acid solutions, Br. Corros. J. 33 (1988) 109–116.
- E. Otero, A. Pardo, E. Saenz, M.V. Utrilla, P. Hierro, A study of the influence of nitric acid concentration on the corrosion resistance of sintered austenitic stainless steel, Corros. Sci. 38 (1996) 1485–1493.
- T. Raghu, S.N. Malholtra, P. Ramakrisnan, Corrosion behavior of sintered austenitic stainless steel filters in sulphuric acid solutions, Br. Corros. J. 33 (1988) 109–116.
- E. Angelini, P. Bianco, F. Rosalbino, M. Rosso, G. Scavino, Sintered austenitic stainless steels: corrosion behavior in sulphate and chloride media, Werst. Korr. 45 (1994) 392–401.
- E. Otero, A. Pardo, E. Saenz, M.V. Utrilla, F.J. Álvarez, Corrosion behavior of AISI 304L and 316L stainless steels prepared by powder metallurgy in the presence of sulphuric and phosphoric acid, Corros. Sci. 40 (1998) 1421-1434.
- R. Omrani, B. Shabani, Gas Diffusion Layers in Fuel Cells and Electrolysers: A Novel Semi-Empirical Model to Predict Electrical Conductivity of Sintered Metal Fibers, Energies. 12 (2019) 855.
**- The surface area of 0.022 m2/g was used for this study. This is a measured surface area for the powder sample, and the surface area for the fiber media has not yet been measured.