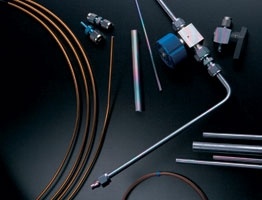
What's it like to work with SilcoTek coated fittings & valves? We tested and prodded inert, corrosion resistant valves and fittings to expose the worst and best of our coatings. Here's what we found.
Last week we discussed the ins and outs of installing and caring for SilcoTek® coated tubing. But what about valves and fittings? We've applied inert or corrosion resistant coatings to the flow path but are there special precautions, problems or potential pitfalls relating to coated fittings? Well no worries, it's all good news here! We'll go through the good and bad of how to install SilcoTek coated fittings and valves.
First, we'll assume you've selected the right coating for the application. Not sure? Here's a handy application guide for selecting the right coating for the job.
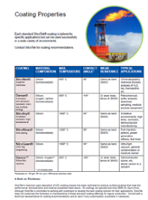
Making the connection
Connecting Dursan®, SilcoNert® or Silcolloy® coated valves or fittings is a pretty standard affair. There's no need to take special precautions for most types of connections but there are a few areas to pay special attention to. So let's discuss some of the more popular connections:
Compression fittings
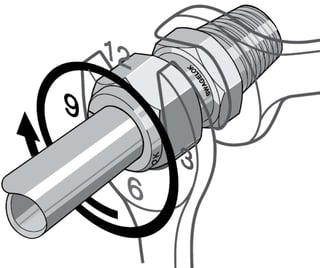
Anything special I need to know about installing fittings?*
To install SilcoTek coated tubing all you need to do is follow the manufacturer recommended fitting make-up procedure. Here's an example from Swagelok®. For analytical and high purity applications avoid using snoop or other liquid leak detection sprays. Use an analytical leak detector, they're available from most chromatography supply houses. Here's an example from Restek®. Fittings should also be coated to assure an inert flow path. You don't need to coat the ferrule or the nut, just the fitting body. Ferrules are not significantly exposed to the flow path in a properly made up fitting and can leak in some applications if coated. Most nuts come with a thread lubricant bonded to the inner thread which will likely be removed during coating. That can result in thread binding, so it's wise to not coat the nut; besides why coat something that's not in the flow path?
Face seal fittings
VCO, VCR, CF and other face seal fittings rely on a durable precision and scratch free seal area to assure a leak free connection. It takes a durable and flexible coating to withstand the stress of compression, especially in conflat knife edge seals. Fortunately SilcoTek inert coatings bond to the fitting surface and actually diffuse into the stainless steel surface, assuring a high quality, leak free connection. How leak free are we talking about? Well SilcoTek coated seals have been tested in UHV applications down to 10-10 Torr!
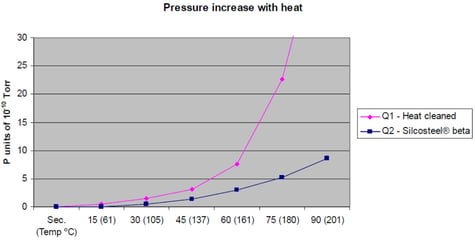
Threaded fittings
Take special precautions when making a coated threaded fitting. If both the male and female threads are coated, the threads can seize because we're dealing with similar materials in the fitting and high shear stress which can cause the coating surface to bind. To avoid galling problems, use thread lubricant or PTFE tape on threads. Note you should apply thread lubricant to any threaded stainless steel fitting regardless of whether it's coated or not. Stainless steel threads are notorious for galling.
Quick connects
Quick connect fittings rely on o-rings or elastomers to make a leak tight seal. SilcoTek coatings don't change the surface roughness of the connector, so if a connector has a smooth precision o-ring seal before coating, it'll be the same after. SilcoTek coatings don't significantly change roughness or tolerance of the seal area.
What about valves?
Well most valves have the same type of connections mentioned above, so follow the manufacturer recommended method for making the connection and you should have no problem with a coated valve connection. However, there are some things worth noting about coating valves. Because valves must internally seal, either by a gate, ball, needle, or diaphragm, to control flow, we'll need to discuss coating internal valve components.
Only coat the flow path. Why coat springs or nuts that aren't in the flow path, it only adds cost. That's our take on coating valve components. Unless you have a specific external corrosion application, it pays to coat on the value added flow path components.
Some valves are harder to coat than others. Because our process heats the surface to around 400ºC, most elastomer seals would not survive the coating process. We hate to damage parts, so to avoid causing pain and suffering to the customer, we ask that valves be shipped to us completely disassembled. Unfortunately some valves have pressed-in components or permanent assembles that don't lend themselves to disassembly. What to do? Fortunately we have relationships with leading valve manufacturers.
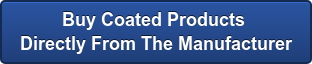
They'll let you order a coated valve through the valve company. Really! All you need to do is purchase the coated valve and they'll ship it to you. The valve company will send valve components to us for coating and then assemble the valve to their specifications.
There are other valves that can be easily disassembled and coated but how can you tell? Well we've got some experience with valves, we get hundreds per month to coat, so we can help. We're not authorities on all valves, but we can offer some general guidelines for the most popular valves. Some valves can be partially coated (most of the flow path components) while others are more difficult or not possible to coat due to pressed in elastomers or not coatable metals. Contact us and we can discuss your valve and how best to coat it. Here a list of a few popular valves and recommendations regarding coating. If your valve is not on the list or even if it is on the list, please contact our customer service team to discuss your valve and application. That way you're assured the best possible coating performance.
Your system is installed, congratulations! Now how do you care for SilcoTek coatings? Watch our webinar to find out.
* Image courtesy of Swagelok®