
Sometimes selecting the right coating can be a real head-scratcher. Here are some tips about things to consider when choosing the right coating for your application.
How to Pick the Right Coating for Your Application
SilcoTek’s technical experts are here to help you get the facts about CVD coatings and select the best coating for your application. Some applications may require specialized treatment, but often one of our standard surface coatings will perform well for you. SilcoTek’s complete platform of coating solutions offer a multitude of surface properties for your most challenging applications:
- Low surface energy
- Oleophobicity
- Corrosion resistance
- Hydrophobicity
- Anti-coking/anti-fouling
|
- Abrasion resistance
- High purity/low outgassing
- Easy cleaning/anti-stick
- Contamination resistance
|
In this blog post you will learn:
- Factors to consider when selecting a coating for industrial and analytical applications
- Common applications for inert CVD coatings
- How a part form factor can impact coating performance
- How environmental factors should always be considered even if the part is not intended for corrosive service
|
The recommendation process involves listening to the customer’s application and need, providing coating samples, testing & evaluation at both customer and SilcoTek® sites, technical consultation regarding coating & process optimization, site visits, and more. The time needed to select a coating can be as short as a few minutes or can involve months of evaluation, depending on customer requirements and the application. The SilcoTek service experience couples technical expertise with coating capability and performance to give customers a solution they (and their customers) can rely on.
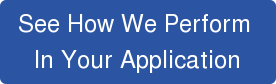
Common Applications
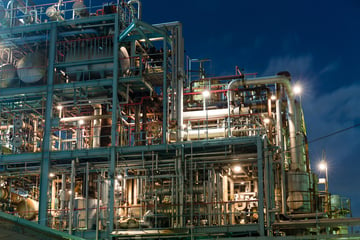
SilcoTek offers a range of coatings developed to solve difficult material problems in a wide variety of industry, analytical, process, and research applications. SilcoTek’s technical staff can also modify an existing coating or develop a new coating technology to meet your needs. Have a question about our coatings? Go to our FAQ page.
Common coating applications include:
- LNG/CNG sampling and testing
- Blue hydrogen analysis
- Refinery, flare, and flue gas
- Process monitoring
- HCl or acid stream analysis
- Air emissions analysis
- NOX and SOX
- Chemical manufacturing
- Mercury
- Semiconductor manufacturing
|
- Power generation (coal and gas fired)
- Ammonia sampling
- Odorant sampling
- Low sulfur regulation compliance
- Moisture analyzers
- Research (reactors, vacuum, etc.)
- Liquid and gas chromatography
- Hydrocarbon analysis
- Stack and flare monitoring
- High purity & contamination prevention
|
What are the benefits to these applications?
Coatings like Dursan® and SilcoNert® prevent interaction of the environment or sample with the part or flow path surface. The coatings make the surface non reactive and can improve corrosion resistance, durability and life of the part. More importantly the coatings can improve response and process control, improving yield and product quality or preventing regulatory compliance issues.

Tips for Selecting the Right Coating
A successful coating solution involves matching the performance environment of both the application and the coating. Our technical experts are here to help you select the right coating for your application. For customers who prefer an online solution we built an online coating selector to help customers pick the right coating. Click on the button below to give it a try.

We also offer an online chat option for those who prefer chat over phone discussions. Regardless of how customers interact with us, there are factors to consider before making a coating selection. Here's a list of a few of the many exposure conditions and other factors to consider when making a coating selection.
1. Chemical exposure and environment
- Is the application exposed to acids or bases?
- What target chemicals are you sampling?
- Duration of exposure
- Operating temperature
- Cleaning solvents and methods used
- Abrasives or other durability concerns
- Previous chemical exposure of the part
Why is this important?
Because chemical exposure can be a source of pitting and surface damage that can lead to chemical adsorption and sample or product cross contamination. Protecting the surface by applying a high durability, inert coating can improve performance but exposure can play a big part in overall life of the coating. Sometimes we'll select a slightly less inert but more durable coating in order to strike a balance between performance, durability and coating life.
2. Form factor of the part
- What areas of the part are sensitive to damage?
- Surface finish of the part
- Wear points of the part
- Metallurgy of the part
- Where can the part be held with a handling fixture?
- Are there seals or o-rings in the part?
- Is the part disassembled?
Why is this important?
Because part metallurgy and surface finish can play a role in coating compatibility and adhesion. We can apply coatings to most metals but there are some (like copper and copper alloys) that react negatively to silicon surface bonding. This can result in poor coating morphology and reactivity. Wear or damage sensitivity can dictate handling and coating selection. We may fixture a part differently depending on the surface and we may select a more durable coating in wear applications. O-rings and part assembly can severely impact coating quality, so we request the part be completely disassembled to assure quality.
3. Performance requirement of the part’s surface
- How do you need the surface to perform? Corrosion resistance, inertness, hydrophobic, etc.
- Are there welded or brazed/soldered joints in the component?
- Are there blind holes or small cavities in the part?
- Overall dimensions and quantity
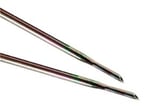
Why is this important?
Desired performance is obvious. We don't want to apply a coating that does not meet performance expectations, but we also want to know about the overall part configuration, it's precision and if there are small flow paths. That's because we often specify special preparation, fixturing or processing for intricate or high precision parts.
That’s a lot to consider! If you don’t know something about a part, our technical staff and production technicians will address any questions or potential issues. If you know lots about your part and application, you may feel comfortable selecting a coating and completing our online quote request form.
Go to our coating applications page to learn more about how SilcoTek® coatings solve material problems, or check out our webinar on selecting the right coating for your application.
To keep up with the latest in coating science, subscribe to our email and blog, or follow us on LinkedIn.
