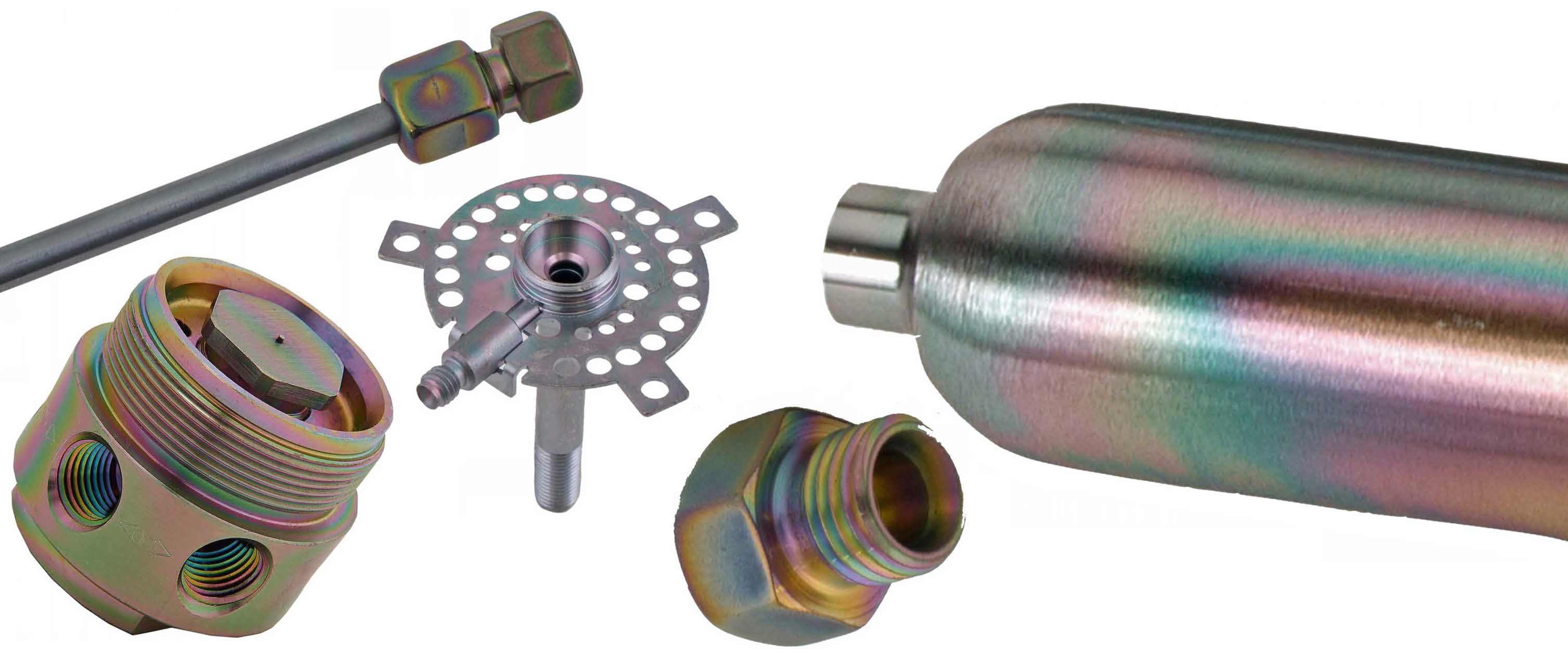
Dursan®? SilcoNert®? Silcolloy®? And what the heck is Notak™? What's with all the coatings? Why does SilcoTek® offer so many CVD coatings? Let's dissect where each coating is used.
Think of our coatings as tools. Only our tools are used to improve the performance of your products or processes. Think of it this way, you finally buckle down and do that bathroom remodel. The job entails replacing fixtures, replacing tile and painting that '70's olive green wall (you know who you are....). You've got all the materials, knowledge, and motivation to do the job. You reach into the trusted tool bag only to find a single screwdriver. But you'll need a hammer, saw, tile trowel, drill and that Sawzall® you've always wanted. Do you really need a Sawzall®? No but nothing says home professional than owning a Sawzall®..* Anyway I digress. You need lots of tools but all you've got is a screwdriver. Can you get the job done? Nope. You'll need lots of tools designed and optimized to do specialized tasks. That's exactly what our coatings are, tools designed to do specific tasks.
In this blog post you will learn:
- How to grade and score a coating for desired performance in your applications.
- Get a summary of applications for each of our coatings.
- Get the material composition of each coating.
- Do some math...ugh...
|
Want to get the low down on our products? Download our introduction to coatings, SilcoTek 101.
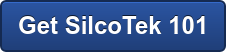
So each coating has specific uses and applications but there are so many. How can I be sure I'm getting the right coating for my application?
No worries, we have a team of specialists, engineers and scientists who's job it is to help you select the right coating for the job. But since knowledge is good, we've put together a quick reference guide to help customers understand the use of each coating. The guide is not totally comprehensive, since each application is different it's always best to chat with one of our experts to be sure of your application. In the extreme, some applications can require customization. We can do that too.
Have other questions about our CVD coatings?
Go to our Frequently Asked Questions page
A summary of coating performance.
Check out the coating performance guide below. It scores the performance of each of our coatings in a variety of applications and environments. Need an inert coating for use below 400c? SilcoNert® 2000 should fit the bill. But what if surface will be exposed to acid and bases? Then Dursan® would be the better choice. It's a good all-round performer, much like that Sawzall®.
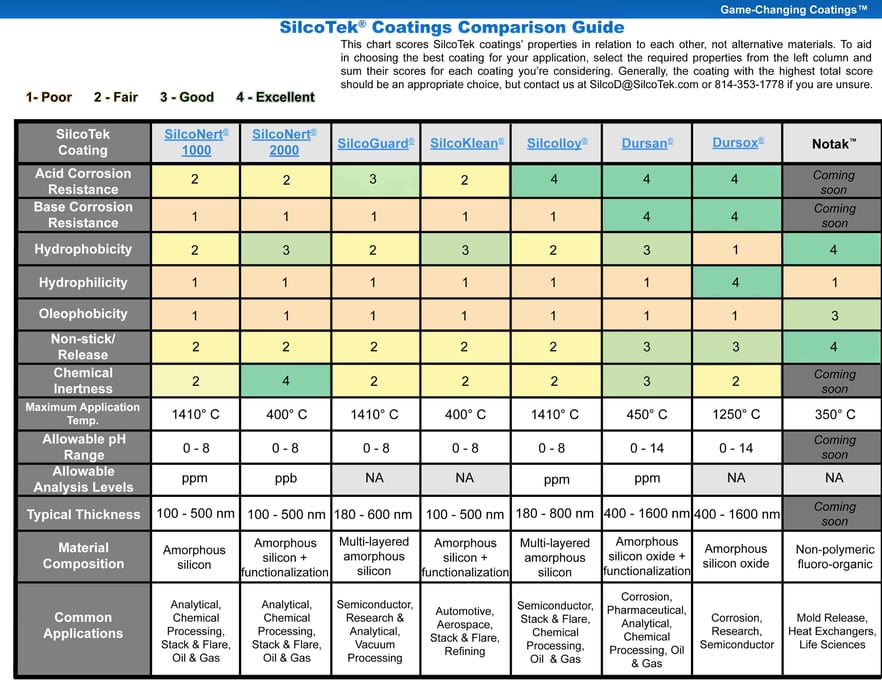
How do I use this selection guide?
Ask the following questions regarding the intended application:
1. What surface properties are required?
2. What is the maximum application temperature?
3. What is the allowable pH range for the application?
Using this information, sum the given values for the properties to find the most effective coating for the application. Here is an
example:
1. The application requires surface properties of Chemical Inertness, Hydrophobicity, and Acid Corrosion Resistance.
2. The application is prone to acid corrosion and needs an allowable pH range up to 14.
Using this information, each coating would receive the following scores.
Scoring the coatings:
SilcoNert 1000: (Chemical Inertness, 2) (Hydrophobicity, 2) (Acid Corrosion Resistance, 2) = 6 SilcoNert 2000: (Chemical Inertness, 4) (Hydrophobicity, 3) (Acid Corrosion Resistance, 2) = 9 SilcoGuard: (Chemical Inertness, 2) (Hydrophobicity, 2) (Acid Corrosion Resistance, 3) = 7 SilcoKlean: (Chemical Inertness, 2) (Hydrophobicity, 3) (Acid Corrosion Resistance, 2) = 7 Silcolloy: (Chemical Inertness, 2) (Hydrophobicity, 2) (Acid Corrosion Resistance, 4) = 8 Dursan: (Chemical Inertness, 3) (Hydrophobicity, 3) (Acid Corrosion Resistance, 4) = 10 Dursox: Chemical Inertness, 2) (Hydrophobicity, 1) (Acid Corrosion Resistance, 4) = 7
|
According to the sums, Dursan® is the best option and SilcoNert® 2000 is the second best option. Because the application
indicated a need for acid corrosion resistance and a wide pH range, Dursan is the best choice for this application. Congratulations! You passed the math test!
Want more in-depth information about our coatings and applications? Go to our coating page to learn more.
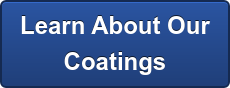
*Sawzall® is a registered trademark of Milwaukee® Electric Tool Corporation