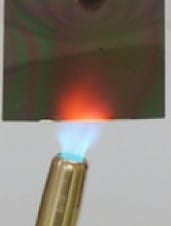
In part 3 our our blog series, we test and compare how Silcolloy® and improved Silcolloy protect stainless steel from oxidation and corrosion after high temperature exposure.
Can Silicon Prevent Stainless Steel Oxidation and Corrosion?
In this blog post you will learn:
- How an enhanced version of Silcolloy improves the oxidation resistance of stainless steel.
- How the heat resistant improved Silcolloy performs under corrosive conditions.
- Can I buy the new Silcolloy?
|
Background
In part 1 and part 2 of our blog series on improving the heat resistance of our Silcolloy coating, we tested and compared the thermal performance of our standard Silcolloy® coating (SOP) and an enhanced version of Silcolloy (called RD15).
The enhanced Silcolloy coating features a primer coating layer that improves heat resistance and prevents catalytic action between the base metal and the top layer of silicon.
In Part 2 of our blog series we compared the visual and EDS testing results of the parts after heat exposure. The results showed a significant improvement in both coating appearance and silicon coverage, see figure 1 below.
Figure 1: Visual evolution of the two coatings going through thermal exposure (all carried out for 6 hours in air)
EDS (Energy Dispersive Spectroscopy) maps of silicon Ka1 line are displayed in Figure 2. EDS can be used as an indicator of coating coverage on the substrate surface. Elemental silicon is represented in blue; the continuity and relative intensity of the blue color reflect the continuity and relative thickness of the coating. A lack of blue signifies a discontinuity in the coating. The EDS results below show that the enhanced Silcolloy (RD15) has significantly more silicon after exposure to 800°C. This indicates that the coating may still be offering significant oxidation and corrosion protection after high temperature exposure.
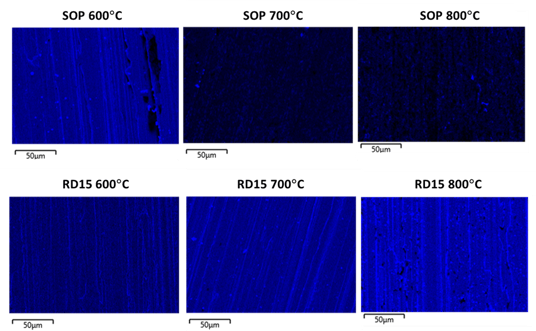
Figure 2: EDS maps of silicon Ka1 line (represented in blue), used as an indication for coating coverage, for the two coatings after thermal exposures to 600, 700 and 800°C for 6 hours in air.
Protection Against Oxidation and Corrosion
Silicon coverage and appearance have improved to be sure but do those improvements translate into better protection of the underlying stainless steel substrate? After all that's the purpose of the coating.
To verify that the enhanced Silcolloy® (called RD15 in this study) does indeed retain good barrier properties after thermal exposure, we designed two experiments:
Test 1) Investigate how much the coating protects the metal substrate from oxidation during the thermal exposure.
Test 2) Evaluate the corrosion-resistance of the coating after thermal exposure.
Oxidation Protection
The first experiment was carried out by chemical stripping of the coating in an alkaline bath after thermal exposure. We then examined the underlying stainless-steel substrate for oxidation.
The samples included a baseline uncoated 316L stainless-steel coupon, an SOP-Silcolloy coated coupon and a RD15-coated coupon for each temperature group (600, 700 and 800°C, respectively). Each group of coupons were first exposed to the said temperature for six hours in air, followed by chemical removal of the coating via an alkaline etch (except for the uncoated baseline samples), and finally for visual inspection and EDS analysis.
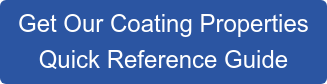
Figure 3 (below) shows the uncoated coupons were all discolored (from purple to blue to brown as the oxide layer gets thicker), and the measured oxygen concentration rises with increasing temperature. The coated, RD15 clearly outperformed SOP in protecting the substrate from oxidation. The substrate metal under RD15 experienced little change in color from the original silver, remaining bright and shiny. The EDS measured oxygen contents (shown below each sample image) were significantly lower than both the uncoated and SOP. It is interesting to see higher oxygen content in SOP than uncoated at 800°C, which may be caused by part of the oxidized silicon coating being fused with the metal surface and not being completely removed.
Figure 3: Visual appearances of three groups of coupons that were thermally exposed to 600, 700 and 800°C for 6 hours in air first, followed by coating strip to reveal the SS substrate (except for the uncoated samples). The oxygen content listed under each sample was obtained via EDS analysis using 15kV acceleration voltage; BDL stands for “below detection limit” which is 0.1% for the EDS analysis
Improved Corrosion Resistance
The second experiment compared 316 stainless-steel square coupons that were coated and thermally exposed. The samples were then immersed in a 5% sodium chloride ( NaCl) solution for seven days at room temperature. At the end of day seven, a linear polarization resistance scan was performed on each sample in the same solution (5% NaCl) to obtain their corrosion rates.
Figure 4 (below) compares the visual appearances and corresponding corrosion rates of the two coatings. RD15 again outperformed the SOP coating by exhibiting better visual integrity as well as lower corrosion rates by two orders of magnitude (as shown below the sample images).
Figure 4: Visual appearances of three pairs of coupons that were thermally exposed to 600, 700 and 800°C for 6 hours in air first, followed by immersion in 5% NaCl solution for seven days. Corrosion rates (CR) were measured via linear polarization resistance scan and reported in 10-3 mpy (mills per year)
Can I Buy Enhanced Silcolloy?
Improved Silcolloy® is still under development and will be available to our customers soon. Contact our Technical Service Team to learn more about the coating and to discuss your application. We'll be happy to provide free coating samples and discuss potential coating opportunities.
Summary
This blog series (click to read about blog post 1 and blog post 2) focused on a recent thermal stability property improvement of SilcoTek’s Silcolloy® coating. The enhanced coating, known as RD15, contains a primer layer that separates the amorphous silicon coating from the metal substrate. The resulting corrosion resistant coating maintained the same surface chemistry as Silcolloy but vastly improved the thermal stability of the coating. The new coating has effectively eliminated metal-induced silicon crystallization below the intrinsic silicon crystallization temperature, as proven by Raman spectroscopy.

In addition, the primer layer also acts as a stabilizing matrix for the silicon coating. Once crystallization does occur the coating limits the degree of structural disruption and damage imposed by the crystallization transition. As a result, the enhanced Silcolloy coating maintains much better structural integrity and oxygen barrier properties through thermal exposures up to 800°C, as demonstrated by comparative SEM, EDS, metal oxidation analysis and corrosion resistance experiments. The combined data led to the conclusion that enhanced Silcolloy provides superior thermal stability than the current Silcolloy coating.
Stay in touch with the latest in coating material science. Subscribe to our blog and email, or follow us on LinkedIn.