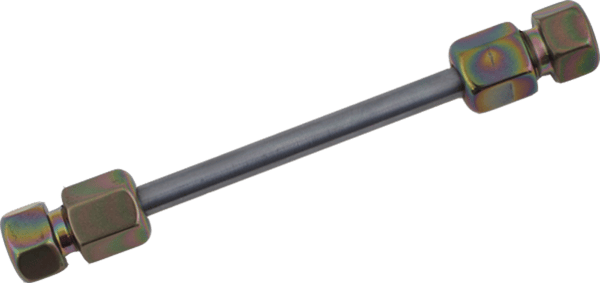
We asked some basic questions about the role bio-inert coatings play in improving HPLC test results. We got some interesting answers.
AZoM, the materials science online publication, recently discussed the role bio-inert materials play in HPLC testing with one of our leading scientists, Dr. Jesse Bischof. Here are some interesting segments of that discussion. You can read the entire article in AZoM.
What role does bio-inert coating play in HPLC applications?
HPLC is all about getting analytes separated as quickly and efficiently as possible. In the case of protein and other biomolecule analysis, the difficulty lies in the interaction between the analyte and then the components that make up the flow path of the system. Any exposure to metals or other active sites may cause the proteins to stick to the surface of that flow path.
This leads to peak tailing and potential carryover issues in subsequent analyses. For example the peak shape and quality of a 50ppm tetracycline when tested through an uncoated flow path shows poor peak resolution and tailing. The Dursan coated flow path shows improved peak shape, and improved resolution.
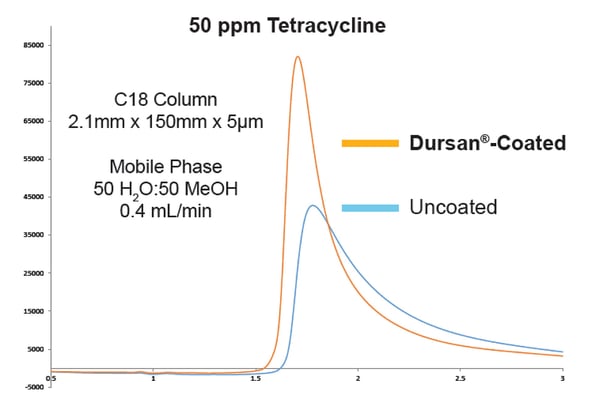
There are also times where the adsorption is irreversible, and when scientists are attempting to do quantitative analysis of these proteins and molecules, that adsorption can have a massive impact on the results. By making the flow path bio-inert, these problems no longer need to be addressed.
What difficulties does the coating eliminate in HPLC applications?
The coating acts as a barrier coating between the flow path and the sample while still allowing the instrument to be constructed from stainless steel. With the coating in place, you now have the robustness of the stainless steel, along with the bio-inertness of the Dursan coating. It’s the best of both worlds. Dursan can even be applied to sintered metal fits to improve inertness while maintaining filter efficiency and making a bio inert flow path.
Is Dursan® a corrosion resistant HPLC coating? Why is this important?
Dursan is corrosion resistant. In our immersion testing, a Dursan coated stainless steel coupon will have similar corrosion resistance to alloys such as Hastelloy®, an alloy specifically designed for corrosive environments. For example ASTM G31 comparative immersion testing shows that after 24 hours of exposure to 6M hydrochloric acid the Dursan® coated test coupon demonstrated similar performance to the Hastelloy® coupon.
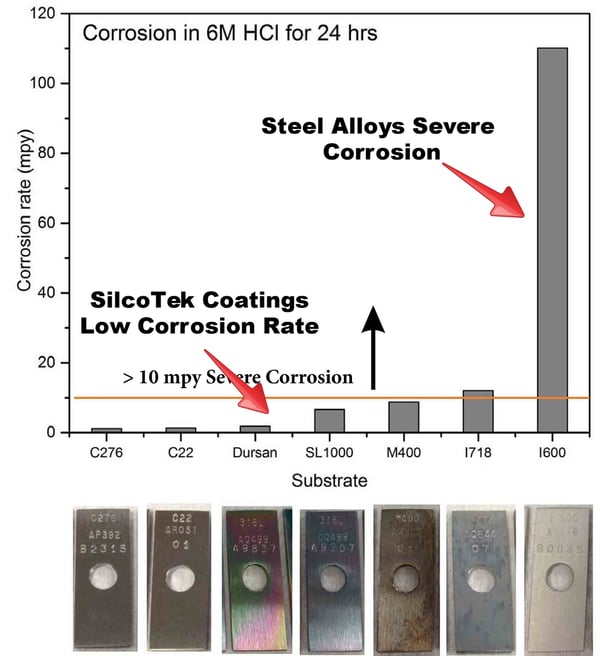
Improving corrosion resistance is important for two reasons. First, it improves the lifetime of the equipment, and may open up options for scientists to utilize solvent systems they may not have considered trying in the past.
Second, when a part starts to corrode, it will introduce metal ions into the system. Proteins and biomolecules are very sensitive to metal ions, so keeping the two away from one another will help with consistent analysis.
Protein carry-over and false readings are common problems while improving instrument durability. Is this something Dursan® can improve? How?
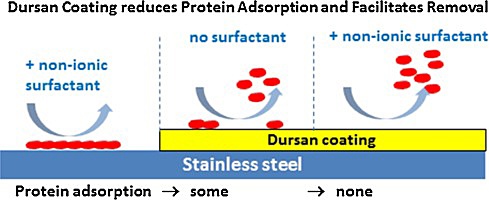
These are common problems, especially when an instrument is utilizing an autosampler. The needle that is used for the injection is dipped into sample after sample, and any carryover may lead to false readings. I actually experienced this issue when my daughter was born. She and a few other children tested positive for a high level of a particular protein at birth. The pediatrician told us that she had never seen so many children test positive in such a short window. It turned out that there were about 3 or 4 other children that had a false positive due to this protein carryover issue.
Dursan could have solved this problem by having a surface that proteins cannot stick to and during a rinse cycle, all of the proteins are removed from the autosampler. For example a recent Abbott study found significant reduction in protein binding and carryover. The graph below shows almost no Mouse igG protein sticking to a Dursan coated surface while the stainless steel surface retained a significant amount of protein.
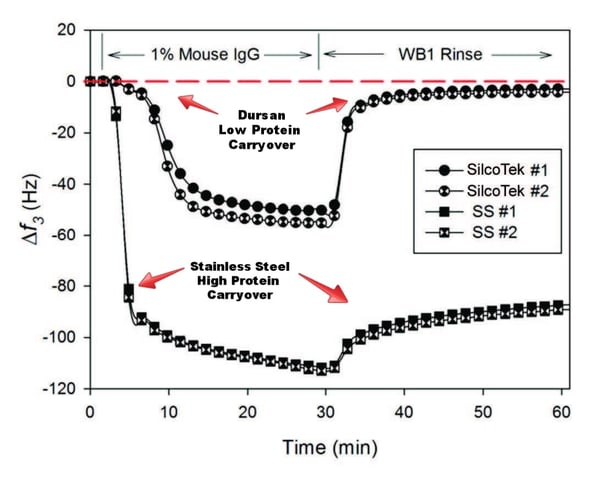
Can Dursan® improve bio-analytical and LC system corrosion resistance? How? Why is this important?
The application of Dursan to any system that may see chemicals that are corrosive to steel such as chlorides, bleach, or certain acids would be a benefit to the longevity of the system. As stated before, this helps to keep the instrument in proper operating condition and also keeps metal ions out of the solution that is being analyzed. Comparative 72 hour immersion of Dursan, Silcolloy, and uncoated stainless steel shows the Dursan surface prevents corrosive attack while the stainless steel surface is subject to pitting and corrosive attack. 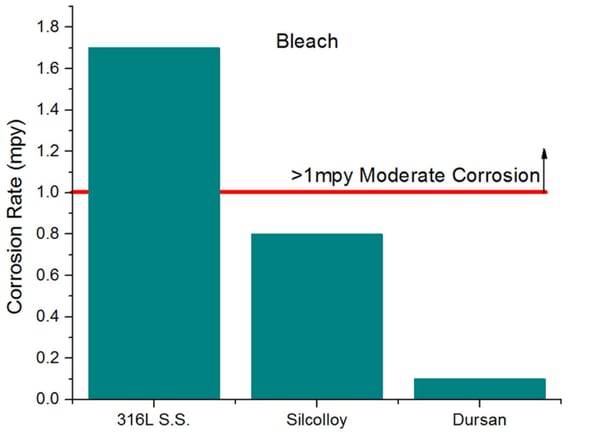
What does SilcoTek’s bio-inert coatings mean for the future of HPLC applications? Are there other applications that can benefit from it?
SilcoTek saw one of its other coatings, SicoNert® 2000 (formerly Sulfinert®), get adopted into the GC world and provide inertness at levels that were previously unattainable. We hope to see the same thing happen with Dursan® in the HPLC community. We believe it will lead to better analysis across the board including much lower detection levels, faster analyses, more reliable results.
There are numerous applications of Dursan outside of the HPLC world. It was originally developed for oil and natural gas downhole sampling, it shows great release properties in the plastic extrusion and mold release community, and with its anti-corrosive properties, it has found a home in numerous industries including automotive, aerospace, food and beverage, as well as offshore and marine environments.
About Dr. Jesse Bischof

Jesse received his Ph.D. in chemistry from Penn State University studying high-pressure chemistry. Jesse's current work involves developing new coatings, improving our existing selection of coatings, and finding new and interesting markets where Silcotek's coating technology can help solve customer problems. You can contact Jesse or any of our technical experts by emailing our Tech Service Team.