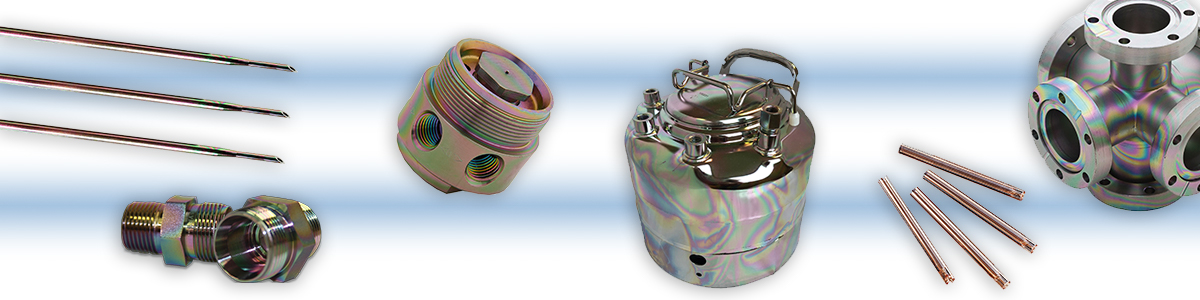
Functionalized, amorphous, bond, lattice, bulk? What do all these confusing terms mean? In this blog we explain common CVD coating terms.
Common CVD Coating Terms Defined
We often describe SilcoNert® 2000 as a: "functionalized, non reactive silicon coating process that prevents adsorption and makes flow paths inert for better process control and provides superior analytical results". We'll also describe the coating application method as: "a chemical vapor deposition (CVD) process that bonds the coating to stainless steel, alloy, ceramic, and glass, making a high tolerance durable coating even under extreme temperatures and pressures".
So what exactly do those descriptions mean? We rather casually throw out a lot of terms that, well, may not speak to the casual reader. I know from my own experience that it took several years working in this industry to feel comfortable using some of the terms thrown about on our website. Here's another example:
We describe Dursan® as: "a process that deposits a chemically protective barrier of
amorphous silicon, oxygen and carbon that is further functionalized to resist adsorption of corrosive, reactive, and otherwise unwanted molecules. Applied via chemical vapor deposition (CVD), the Dursan® process is required when both a robust and chemically inert surface are critical". Again with the functionalized! And what is adsorption? I know what a molecule is but what exactly does inert mean?
In this blog post we'll review some terms and explain in more common language what they mean and what they mean to the coating, you, and your decision on what coating to select.
In this blog post you will learn:
- Understand commonly used terms applied to chemical vapor deposition processes.
- Learn about how those terms apply to coating selection decision making, and chemical vapor deposition benefits and limitations.
- How coatings that don't use these terms may be a red flag in your coating selection process.
|
Let's get started with the term CVD
CVD, what does it stand for and what's the big deal about a CVD coating compared to say a paint?
CVD stands for chemical vapor deposition. Chemical vapor deposition is a process that involves the reaction of gasses (or other chemicals that easily transition to a vapor) to form a thin film that is, in our application, bonded to a substrate (usually stainless steel).
The reaction usually occurs in a chamber under elevated temperature and or pressure. Those starting "reaction" chemicals are called precursors. In our process the chamber is heated to a target temperature (a temperature that results in the breaking of chemical bonds) that causes the precursor gas to react or break down into the desired coating and attach (or bond) to the material surface. Over time the coating material builds on the surface and creates a coating throughout the exposed part surface.
So for example if we wanted to bond silicon to a surface we may want to use a trichlorosilane precursor. When the trichlorosilane is heated in the coating chamber the decomposition and coating reaction may look like this.
SiHCl3 → Si + Cl2 + HCl
The silicon will bond to any exposed surfaces (both internal and external) while the chlorine and hydrochloric acid gas will be vented from the chamber and scrubbed according to appropriate regulatory requirements.

The CVD coating system may look something like the diagram below. In this example the desired coating material is a silicon oxide base coating with a functionalized (R) surface which is intended to cap any remaining active sites on the coating surface. This makes for a superior non reactive surface.
Want to learn more about our coating process? Go to our Coating Technology and Quality page.
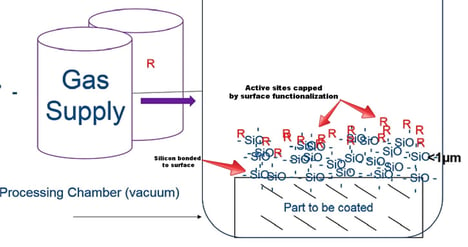
CVD is an important process because it makes very thin coatings that are securely bonded to the part surface. That means part tolerances remain stable while the surface is enhanced to improve inertness (made non reactive), improve corrosion resistance or enhance other performance criteria. That's an ideal combination for applications like precision instrumentation, analytical components, or sampling system flow paths.
Application of coatings by CVD can be more costly and involve limits on part size but other coating application methods don't bond as well or are line of site application only (meaning unseen areas of the part may not be coated).
Functionalization
The discussion above used the term "functionalization". Functionalization can be thought of as a process of changing or enhancing the surface of a coating by changing the chemistry or characteristics of the coating surface.
In the case of the SilcoNert 2000 process, silicon with some oxygen (Si-O) is bonded to say a stainless steel part (a substrate). Now that part is fairly resistant to reactions with other chemicals (what we call inert) but the nature of the coating chemical makeup will still have a few areas where chemicals can bond to the surface (called active sites). Here's where functionalization comes into play. We'll add a layer of a non reactive substance that will occupy or bond to those active sites. Because the actives sites are now occupied, no space is left for other chemicals to come along and bond to the surface. Adding that chemical enhanced the surface by changing the chemical composition of the coating surface to make it more inert or non-reactive. What we call functionalized. From a food perspective (my favorite!), when I add ketchup to my French fries I'm functionalizing the surface to enhance the flavor (but without all that bonding stuff..).
Functionalized surfaces give coatings a boost but they do have drawbacks. If the functionalization is removed (either chemically, by heat, or abrasion) then the bulk coating below is exposed and may result in those active sites being exposed and consequently increased adsorption can result.
About Adsorption and Sample Loss
First let's sort out the difference between adsorption and absorption. Absorption is an effect where a material, liquid, or gas is taken up into the bulk material. Think of a sponge soaking up water.
Adsorption is an effect where the chemical or test analyte sticks to the bulk material either by chemically bonding (chemisorption which is a molecular bond via valance forces) or physically bonding (physisorption, basically by attraction of molecules to the surface without chemically bonding, ie. Van der Waals forces).
The image below graphically depicts the surface interaction of adsorption.*
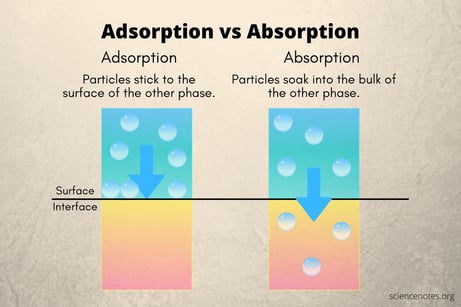
During the analysis of trace active compounds, those compounds that readily attach to surfaces or can easily react with other substances or oxides found on stainless steel. The adsorption reduces the sample concentration, resulting in a distorted test result. If the bond between the stainless steel oxide surface is somewhat weak, the chemical that is sticking to the stainless steel will later release from the surface (desorb) and cause an artificially high test result or cross contamination. The overall effect of adsorption is a change in the accuracy or reliability of the test. Chemicals to watch for adsorption effects include:
- Sulfur and sulfur compounds like H2S, mercaptans, or COS
- Volatile organic compounds (VOCs) like methanol
- Mercury
- Ammonia
- NOx
- Proteins
- Bacteria like Listeria
In the case of proteins, the stainless steel reaction may come from both physisorption or chemisorption. Making it important to have a coating that addresses both adsorptive effects. Next we'll discuss how non reactive coatings stop adsorption.
Breaking the Bond
Chemical bonds are basically attractions between atoms, ions, or molecules. Those attractions make chemical compounds. Bonds can either be ionic (electrostatic attraction between ions) or covalent (sharing electrons between 2 atoms).
Relating bonds to adsorption, that chemical bond or physical surface attraction that causes adsorption can be broken by either changing the surface metallurgy (reduce iron content and promote an oxide layer) by passivation techniques (often not effective) or by applying a secondary treatment or coating that is not reactive and acts as a barrier between the stainless steel and the test analyte. Inert coatings can be applied to either rough or smooth electropolished surfaces (EP) as seen in the graphic below.

The image below shows how Dursan®, which can be applied to stainless steel, other alloys, glass, or ceramics, prevents chemical interaction with the steel and does not attract reactive molecules. Inert coatings, like Dursan® and SilcoNert®, have relatively low binding surface energy and are engineered to have few open bonds that can promote chemisorption. Learn more about inert coatings by watching our webinar.
Watch Our Inert Coating Webinar
Coatings with a low surface energy have less attraction and adhesion to the surface, allowing easy removal of reactive compounds with rinsing or product flow. The result is no adsorption or sample loss and more accurate and reliable testing without cross contamination or desorption.
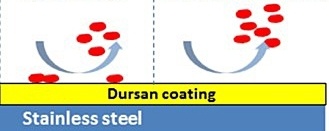
Minimizing Interaction
Let's look at some test data to show how inert coatings perform. In the test below a mix of several reactive compounds were injected onto a gas chromatograph. The sample flowed through stainless steel tubing and GC components (coating GC and GC-MS flow paths) including a separation column. The resulting peaks indicate the presence of the various chemicals. The chromatograph below is an example of what the resulting test should look like. Notice the sharp peaks. You can count each of the test chemical peaks.
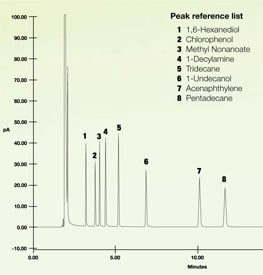
Now let's look at how the gas chromatograph looks like when the sample is exposed to an untreated stainless steel flow path. The same chemical mix is used but now there are fewer peaks! And what peaks are visible show a lot of distortion and tailing (a). The surface is so adsorptive that there are several chemicals that don't even show up on the graph (b).
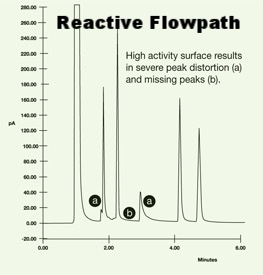
Now let's repeat the experiment, only this time we'll coat the stainless steel flow path with SilcoNert® 2000. Notice how clear and sharp the peaks are and how all the chemicals tested are visible and resolved. The inert coating dramatically improved test results.
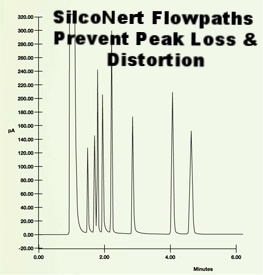
In general an inert coating will improve test quality by a significant margin. Results show that a non reactive surface will perform at levels similar to the ideal control sample and will out perform competitor or passivation techniques by nearly twice the margin.
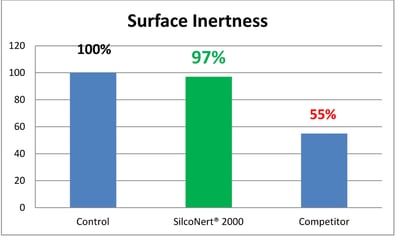
Lattice
We sometimes reference the term lattice when discussing the nature of our coating or other coatings. A lattice can be thought of as an ordered arrangement of a material structure. An ordered structure is described as crystalline in nature. If the order is more random than the structure is described as amorphous. Crystalline structures tend to be more brittle and resistant to bending with a part. That's why ceramic or glass coatings tend to not perform well under stress when the metal substrate is bent. Amorphous structures, like our coatings, tend to be more flexible and resistant to failure when the metal substrate (or underlying surface) is bent.
About Bulk
We also reference the word bulk from time to time in our literature and webinars. Bulk is a term we use to reference the greater mass of a substance. If we talk about a coating on a stainless steel surface bulk would reference the stainless steel (greater mass). If we're talking about a coating only and functionalizing a surface we may think of the base coating as the bulk (again greater mass).
Coating companies that don't reference, or measure coating performance indicators like adsorption or don't take the time to understand how their coatings are structured may not offer real benefits to the end user. Take the time to read and understand how a coating is structured, applied and performs under your conditions.
If you have questions about our coatings, need help understanding terms used, or need help with a coating selection for your application, contact our Technical Service Team. To keep in touch with the latest in coating technology, subscribe to our email and blog or follow us on Linkedin.

* image credit Science Notes .Org. https://sciencenotes.org/adsorption-vs-absorption-differences-and-examples/