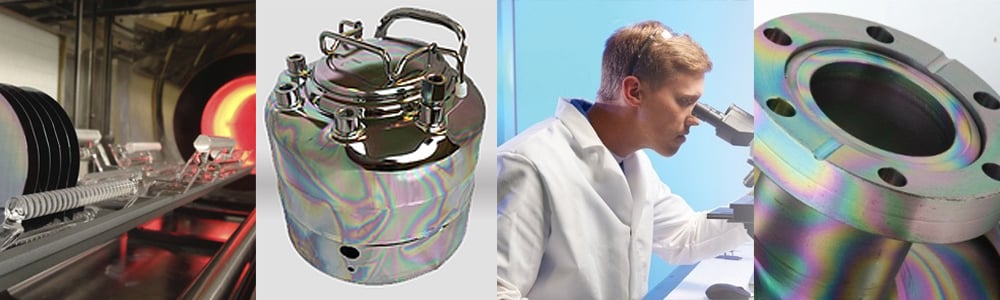
When you place an order with SilcoTek, there are a lot of people working for you; including your own R&D staff. Well not really but that's pretty much what you're getting!
It's Like Having an R&D Scientist Working For You
SilcoTek's R&D team are involved with the customer during every step of the purchasing process. They're dedicated to helping you get the best coating for the application. But why is it that someone from our coating research team are involved with my order? Let's find out why.
In this blog post you will learn:
- How SilcoTek® R&D and Engineering staff support testing and evaluation of your products.
- How our technical staff advise customers on coating test criteria.
- How our staff assist customers in selecting the right coating for their application.
- Get information about the tools we use to evaluate CVD silicon coatings for your products.
|
Full disclaimer: No there isn't an R&D person waiting at the dock for your parts. And not all R&D staff are following every order through every step. But they have either approved or set up the processes that guide decisions and handling of all orders. For new customers, especially customers with complex applications, R&D staff are involved in various parts of the order processes. Let's dig into the details.
Understanding Your Application
For some applications, selecting the right coating that improves your product or application can be challenging. The R&D team is here to help guide customers through the evaluation and selection process in order to get the most benefit out of our CVD coatings. How do they do that? By applying their knowledge and experience to your application and providing you with the best information available so you can make an informed decision about what coating is best for your application. Want some examples of how we worked with customers to improve the performance of their products? Read our case studies.

The coating selection process starts with listening to your needs and developing an understanding of your specific use. Our staff has worked with customers in a wide range of industries and can share some of that knowledge with you, assuring a smooth evaluation process. We'll apply our knowledge and understanding of your needs to help guide customers to the right solution.
Our R&D team can also work with your scientists and engineers to develop a test plan that best fits your application and desired performance results.
Selecting the Right Coating: Buying and Using SilcoTek Barrier Coatings
Customers can also use our coating selector to help determine what's the best coating for their product. The selector was developed with input from our R&D staff to determine the best coating available for more common applications. Give it a try.

For more challenging applications our staff will help customers evaluate and interpret test data to support beta testing and product ramp-up. Our staff of engineers will join in the program to help develop tooling and process methods that optimize efficiency and product quality.
Testing the Coating, the Tools We Use to be Sure Your Parts are up to Snuff
Material surface characterization capabilities serve an essential role in supporting SilcoTek® coating science and R&D efforts. The ability to thoroughly evaluate a surface is key to developing new inert barrier coating products, and plays an essential role in assisting customers with scale up and process troubleshooting.
Various surface characterization techniques enable SilcoTek scientists to study materials, analyze surface bonding mechanisms, and develop a deep understanding of surface properties. SilcoTek® production technicians use material characterization tools in their daily QA/QC process to make sure all our inert, corrosion resistant coatings meet our quality standards and satisfy customer needs. Last but not least, it is not uncommon for customers to work with R&D staff to provide characterization help with their specific substrates or coated parts as part of their product development.

In addition to the in-house characterization capabilities, SilcoTek® also enjoys convenient access to a wide variety of characterization techniques at the Pennsylvania State University (PSU), thanks to our physical proximity to the University’s main campus, and an established academic/industry relationship between PSU and SilcoTek®. SilcoTek’s R&D scientists are certified users of many characterization instruments located at the Materials Characterization Lab (MCL) at Penn State University. Here are some of the tools we use to support our customer, products and processes.
What Tools Are Needed To Characterize A Surface?
Coating surface characterization starts with a capable and knowledgeable R&D team. Tools to help analyze the surface vary with application and need but here are a few tools we use to understand CVD coatings and surfaces.
X-ray Fluorescence (XRF) Analyzer
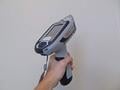
In order to avoid process disruptions caused by incompatible substrates, SilcoTek uses a Thermo Scientific X-ray fluorescence (XRF) analyzer, a non-destructive elemental analysis tool, to identify any unfamiliar incoming metal substrates. Why is this important? Because the substrate material affects the coating quality, surface bond, and ultimate product performance. Knowing the base material enables our process technicians to use the most appropriate processing methods to get the best coating results possible.
FTIR
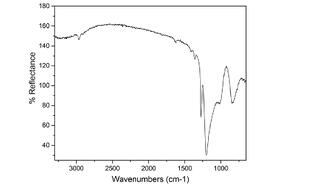
Fourier Transform Infrared Spectroscopy (FTIR) uses broad band infrared radiation as the excitation source to probe molecular structures of various chemical species in gas, liquid or solid state. The FTIR technique is used by SilcoTek’s technicians on a regular basis to perform select QA/QC duties, as well as by SilcoTek’s scientists to assist in their R&D projects. Why is this important? Because FTIR can be used to determine surface quality on a molecular level and can be used as an additional tool in combination with visual inspection criteria to better assess coating quality.
F20 Thin-film Analyzer
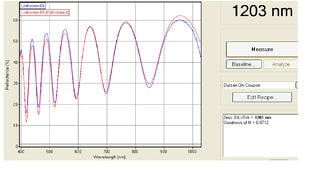
SilcoTek’s F20 thin-film analyzer is a bench top tool that can be configured to measure thin film thicknesses (30Å to 350 mm), optical constants such as refractive index, extinction coefficient and transmittance. It is primarily used by SilcoTek as a quick, accurate and non-destructive way to measure surface thicknesses and to assure consistent coating quality.
Surface contact angle measurement
Contact angle is the angle that a drop of liquid makes to its (usually solid phase) contacting surface. It is measured through the droplet, with the angle formed between the solid surface and the liquid meniscus near the line of contact. The contact angle gives an indication of the wettability of a surface to a liquid (usually water).
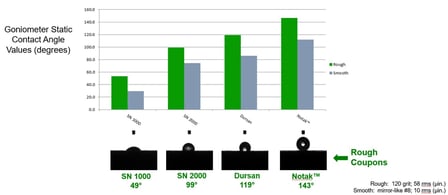
SilcoTek scientists rely heavily on the contact angle measurement in their research of hydrophobic and superhydrophobic surface development, where properly designed surface energy can bring out the extreme water-repellent property in a surface or can prevent surface fouling or enhance mold release.
Contact angle measurement us used to benefit SilcoTek’s customers by ensuring the anticipated surface energy (hydrophobicity/hydrophilicity) as required by application is achieved.
Electrochemical Impedance Spectroscopy (EIS)
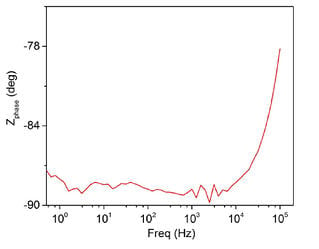
Electrochemical impedance spectroscopy (EIS) is a mostly non-destructive and very useful tool to study and evaluate the performance of protective coatings on metal substrates. The measurement gives information such as resistance, capacitance, double layer capacitance and Faradaic impedance which are related to the performance and failure process of coatings especially during corrosion resistance testing. EIS helps SilcoTek Engineers and Scientists to identify coating pinholes and to develop better, more uniform coatings.
Read More About How
SilcoTek Scientists Improve Coatings
What if Something Goes Wrong? Technical Support for Quality.
Hey it happens. Despite everyone's best effort things can go wrong. That's when having an R&D and Engineering team dedicated to supporting your product really pays off, not only by applying analytical skills but also by applying the research tools used to develop the coating to evaluate and discover any issues in the production process or in the customer supply chain. Learn more about our quality systems and certifications, go to our Quality Page.
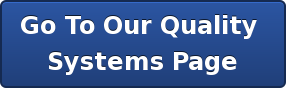
Conclusion
Our R&D and Engineering staff are here to help our customers understand the scope and capability of SilcoTek’s R&D activities, as well as to demonstrate how different tools can be used to facilitate SilcoTek in the development of more innovative solutions, and to help our customers solve application challenges. Easy availability of these tools also allows SilcoTek’s manufacturing team to achieve the highest quality control on our inert coating products, thereby providing consistent and reliable products to all our customers. It's like having an R&D scientist working for you!
Join us in the conversation. Follow our team on LinkedIn!
