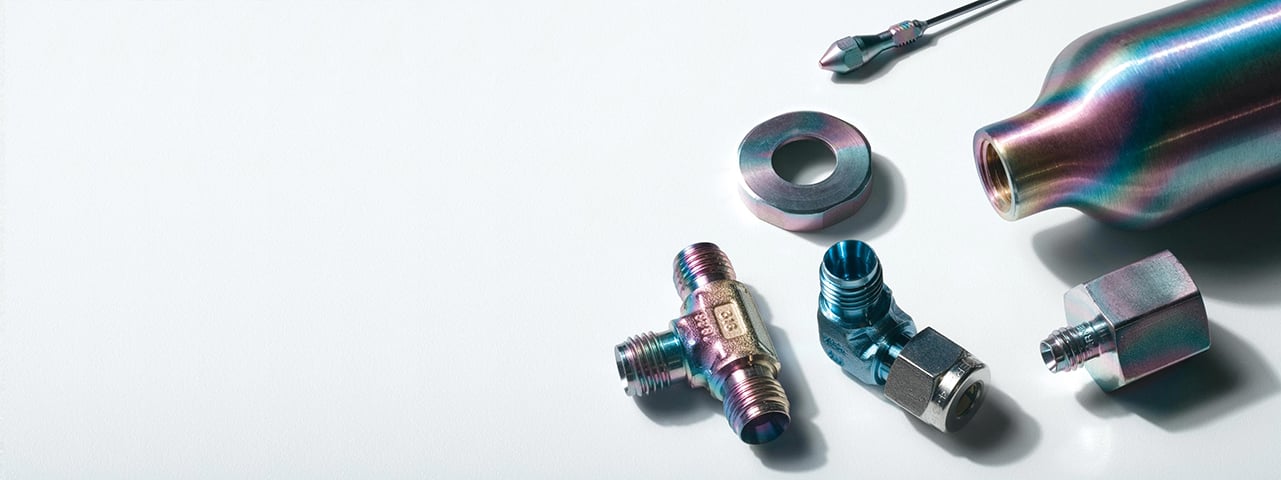
We discuss how to test coatings for corrosion resistance using polarization testing and update our readers on steps SilcoTek is taking to keep our employees and community safe during the COVID-19 pandemic.
Evaluate Corrosion Resistant Coating with Polarization Resistance Scan
We'll be discussing how to test coatings for corrosion resistance using cyclic polarization testing as presented by Dr. Min Yuan. But first we'd like to update readers on our efforts to keep our employees and community safe during the COVID-19 pandemic.
SilcoTek COVID-19 Response
We have been closely monitoring ongoing developments regarding the novel coronavirus (COVID-19) and are actively taking steps to ensure the safety of SilcoTek employees, their families, and our local community. We've increased cleaning, cancelled travel, cancelled meetings, and restricted access to the facility and manufacturing operations in an effort to maintain a safe and healthy work environment.
SilcoTek Remains Open, Supporting COVID-19 Efforts
As you may know, Pennsylvania Governor Tom Wolf ordered all non-life-sustaining businesses to close their physical locations starting Thursday, March 19th in an increased effort to slow the spread of COVID-19. Because of the importance of SilcoTek’s work relating to COVID-19 research and analytical testing, the Pennsylvania Governor’s office confirmed that SilcoTek is classified as a life sustaining business and are authorized to remain operational. According to the Governor’s office, “Life sustaining businesses may remain open, but they must follow, at a minimum, the social distancing practices and other mitigation measures defined by the Centers for Disease Control to protect workers and patrons.”
The game changing properties resulting from SilcoTek's coating are considered essential in the Corona battle and as such SilcoTek has been given approval to maintain operations. The social distancing measures put in place by SilcoTek exceed the criteria established by the Government. The measures we put in place were designed to put the safety of our employees first as we navigate through this pandemic. We will continue to employ best practices and make improvements as we work together to prevent the inadvertent spread of this virus.
SilcoTek is proud to be able to continue serving our customers during these challenging and unprecedented times. We are working as hard as ever to maintain the Plus One service you expect from us. We will continue to expedite and prioritize all coating orders for COVID-19 research and containment efforts. Read the entire SilcoTek COVID-19 update.
Despite this situation, we also understand the importance of meeting delivery commitments to our customers. At this time, you should not expect to see any negative repercussions on orders you currently have in-house at SilcoTek or orders you are planning to send in the coming weeks. We have proactively contacted our critical supply partners to confirm that there should be no changes in our ability to provide game-changing coating services. As usual, SilcoTek employees are prepared to be responsive to emails, web inquiries and phone calls and will continue to deliver Plus-1 service. Our thoughts are with everyone affected by this serious disease.
Sincerely,
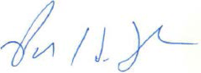
Paul Silvis SilcoTek President, CEO, and Head Coach
Read the complete letter to our customers.
|
How to Evaluate a Corrosion Resistant Coating with a Polarization Resistance Scan?
By Dr. Min Yuan
Background
Multiple methods exist to evaluate corrosion of a metal sample in a corrosive environment. For example, SilcoTek® has used the sample weight loss to calculate corrosion rate in a liquid immersion or salt spray environment, as well as Electrochemical Impedance Spectroscopy (EIS) to assess the stability of coated metal samples exposed to the electrolyte solution under test. These methods and results have been documented in other SilcoTek publications.
This Technical Insight focuses on using an electrochemical method, namely potentiodynamic polarization resistance scan, to gain corrosion rate information needed to evaluate a corrosion resistant coating. Polarization resistance is a quick, mostly nondestructive testing technique commonly used in material corrosion studies to obtain corrosion rate information. Read the complete Technical Insight.

The material to be tested is polarized in the immediate vicinity (±10mV) of its Open Circuit Potential (OCP), the potential measured when no net current is flowing. As the potential of the material is changed, a current will be induced to flow between the working and counter electrodes, and the material’s resistance to polarization can be found by taking the slope of the potential versus current curve. This resistance can be related to the rate of general corrosion for metals at or near their OCP using the Stern-Geary equation1. ASTM G59-97 (2014) states these measurements provide an accurate and rapid way to measure the general corrosion rate and are often used in real-time corrosion monitoring, as well as in ranking alloys and inhibitors in order of resistance to general corrosion2. A good introduction to the theory behind this method can be found here.
The goal of this test is to evaluate the corrosion performance of SilcoTek-coated versus uncoated stainless steel samples in hydrochloric acid using polarization resistance. This test is a good way to check coating quality and coverage as well as to catch holidays, pinholes or defects in the coating that will allow leakage current through and be reflected in the scan results. Have a question about testing your parts? Contact our Technical Service Team.
Have a Question? Contact Our Technical Service Team
Testing Corrosion Resistant Coatings for Stainless Steel
The polarization scan experiment was carried out using a Gamry paint test cell, shown in Figure 1. It consists of a saturated calomel reference electrode, a graphite rod counter electrode, and a working electrode made of the investigated specimen with an exposed area of 14.6 cm2. The sample is exposed to an electrolyte of 5% hydrochloric acid solution.
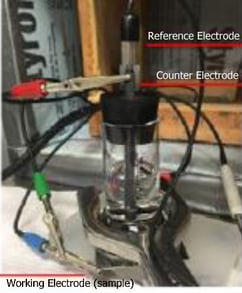
Figure 1: The polarization resistance scan experiment setup
The first set of samples are electropolished and chemically passivated 304 stainless steel. Figure 2 shows the comparison scan results of uncoated substrates versus SilcoTek’s Silcolloy®-coated samples. The results indicate that the Silcolloy coating provided complete coverage of the sample surface and insulated the underlying metal from any noticeable corrosion pathways, so that a corrosion current by 3 orders of magnitude lower was achieved in coated samples. The results are reproducible, and no detectable pinhole or coating defect was present to introduce enough leakage current to be seen in the scan results.
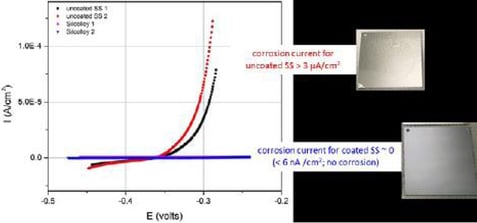
Figure 2:
Polarization resistance scan shows that the Silcolloy® coating reduces corrosion by 3 orders
of magnitude in 5% HCl. Corrosion current was estimated from the slope in the linear polarization scan (not shown here).
The second set of samples to be investigated are 304 stainless steel samples that are mechanically polished to a mirror-like finish. As can be expected, the substrate difference caused significant difference in the magnitude of the corrosion current in comparison to the first set of samples, as seen in Figure 3 below. Three coatings, Silcolloy®, Dursan® and Dursox®, were evaluated here. All coatings were found to improve the corrosion performance of the 304 SS by 2~3 orders of magnitude in 5% HCl. The pictures taken after the scan showed that while the uncoated 304 SS was visibly corroded in the exposed area, all coated samples exhibited no sign of corrosion, as was suggested from the scan results. The tests were repeated and the results were reproducible.
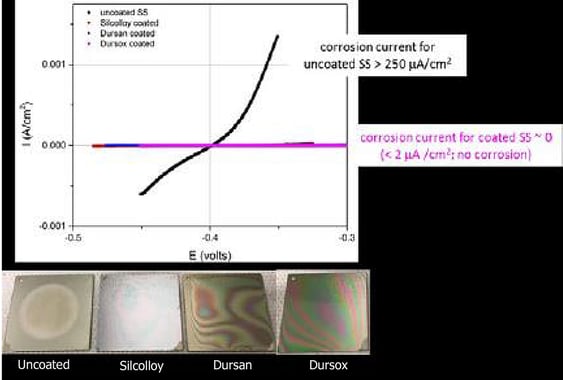
Figure 3:
Polarization resistance scan shows that Silcolloy®, Dursan®, and Dursox™ coatings are all effective in reducing corrosion in 5% HCl. Corrosion current was estimated from the slope in the linear polarization scan (not shown here).
Conclusion
SilcoTek’s CVD coatings are effective barriers against corrosion on stainless steel substrate. This test used potentiodynamic polarization scan as a quick and accurate method to evaluate the benefits of coatings in comparison to the uncoated counterparts. results confirmed that SilcoTek’s CVD coatings provide complete coverage to the metal surface and reduce corrosion current in 5% HCl by 2~3 orders of magnitude.
Want to stay in tune with the latest in coating technology? Follow us on LinkedIn.

References
1. Gamry “Polarization Resistance Tutorial – Getting Started”
2. ASTM G59-97 “Standard Test Method for Conducting Potentiodynamic Polarization Resistance Measurements”