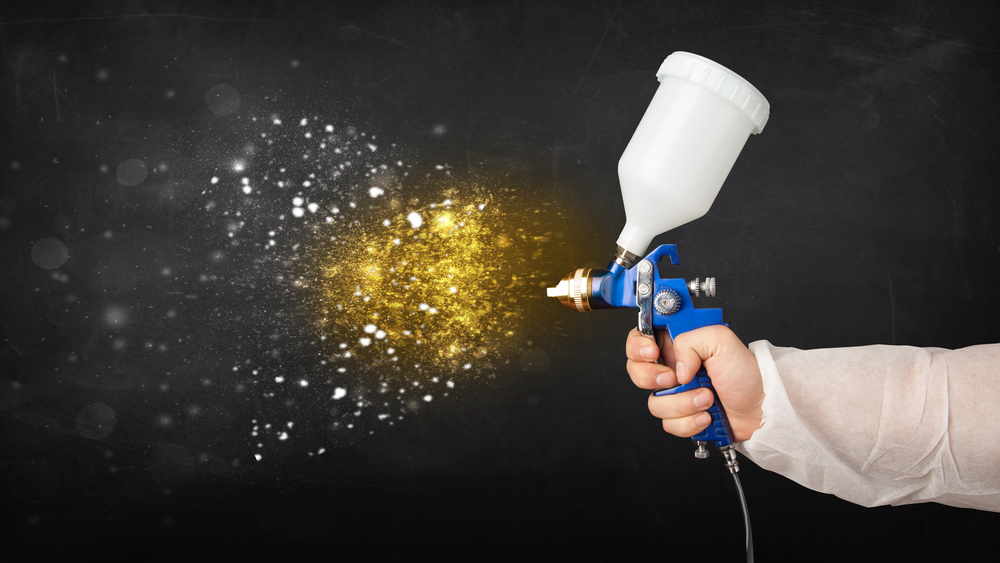
We get this question a lot. Customers have a large part and they want it coated with one of our CVD coatings. They wonder " why can't I spray SilcoTek coatings on my parts at my facility "? Well we'd really like to do that but unfortunately chemistry gets in the way.
We coat your parts at our US facility for lots of reasons but primarily because our process is not particularly mobile. Here's why it's difficult to coat a surface at your location. Here's a hypothetical situation. If you really wanted to apply a silicon coating onto your part I suppose you could go to your local paint store (let's call it Bob's Discount Silicon Paint) and buy a gallon or two of silicon (dusty gray is the color of choice) . After lugging the cans of silicon home and setting up the sprayer you're ready to go to work. You open the can only to discover you purchased a can of rocks! That's because naturally occurring silicon is a brittle crystalline solid. You'll have no luck spraying those onto your parts today. Now you could grind up the silicon into a powder (wear a mask and ear protection) and then mix it with a binder and spray the stuff on a part but all you'd get is a grey paint. The coating would not be inert, nor would it stick to the stainless steel surface particularly well. In fact the coating would likely peel off with minimal abuse. So how is it that SilcoTek® coatings stick so well to a part and remain inert? That's where chemical vapor deposition comes in handy and why parts should be coated at our facility. Have more questions about our CVD coatings? Go to our Frequently Asked Questions page.

First some chemistry review from a previous blog post. Ugh....
In this blog post you will learn:
- Why parts can't be coated remotely at your facility.
- Why CVD coatings are not sprayed on like a paint
- What's the chemistry behind applying CVD coatings.
|
About CVD Coatings: What is Chemical Vapor Deposition?
Chemical vapor deposition is a process that involves the reaction of a volatile gas precursor which is injected into a chamber (typically under vacuum). The chamber is heated to a reaction temperature that causes the precursor gas to react or break down into the desired coating and bond to the material surface. Over time the coating material builds on the surface and creates a coating throughout the exposed part's surface. So for example if we wanted to bond silicon to a surface we may want to use a trichlorosilane precursor. When the trichlorosilane is heated in the coating chamber the decomposition and coating reaction may look like this.
SiHCl3 → Si + Cl2 + HCl
The silicon will bond to any exposed surfaces (both internal and external) while the chlorine and hydrochloric acid gas will be vented from the chamber and scrubbed according to appropriate regulatory requirements. The CVD coating system may look something like the diagram below. In this example the desired coating material is a silicon oxide base coating with a functionalized (R) surface which is intended to cap any remaining active sites on the coating surface. This makes for a superior non reactive surface. Want to learn more about our coating process? Go to our Coating Technology and Quality page.
Materials used in CVD coating systems range from silicon compounds to carbon, to fluorocarbons or organofluorine, and nitrides like titanium nitride. Some materials like silicon can be further enhanced by doping the surface with other materials to functionalize the surface for a specific performance goal (as noted above). Surface preparation, process control and material quality (both the part material and precursor) play a major role in the coating quality.
OK so why can't I just get some of that magic gas mixture and spray it onto my part?
As we mentioned, silicon comes in a solid form. But you can buy gases that contain silicon that can be broken down into their elemental parts. You could deposit the silicon from the gas onto your part but there's a catch. The gas formulations tend to be rather unstable and can be pyrophoric, meaning they may explode or burst into flame when exposed to air. A bit of a bummer if you ask me. That makes for great fireworks but leads much to be desired from a safety standpoint. Plus when the gas is exposed to air, the silicon will immediately bond to the air molecules and create silica (SiO2) which is basically sand. Back to a solid again after all that effort! So spraying in air won't work.
How about we shoot this gas onto the part in a vacuum? Yep you can do that but there'd be no reaction to speak of. That's because there's nothing to drive the reaction nor is there any other element to combine with, like oxygen. So you can spray the gas onto the part but still not get a coating.
To get a coating you'll need some heat or a catalyst, or both to make the silicon containing gas break apart and form a coating. The easiest method to get a coating is to simply heat the part in a chamber containing the silicon containing gas. The heat does the work and causes the unstable silicon gas to break apart, shed the silicon, and coat the part. The silicon then sticks to the part, making a silicon coated surface. Because the part is heated, the silicon will diffuse into the surface making a tough coating bond.
So to coat a part you'll need a gas delivery system, a reactor/container, a vacuum system, heat, and the silicon process gas. Then you'll need combine all that stuff into a consistent process to make a high quality coating. To get it all to work smoothly and safely, that sort of process is best left to the pros and a controlled environment. But you can license our technology and apply our coatings using SilcoTek approved CVD systems. So there is a way to coat parts in house, no spray can needed.
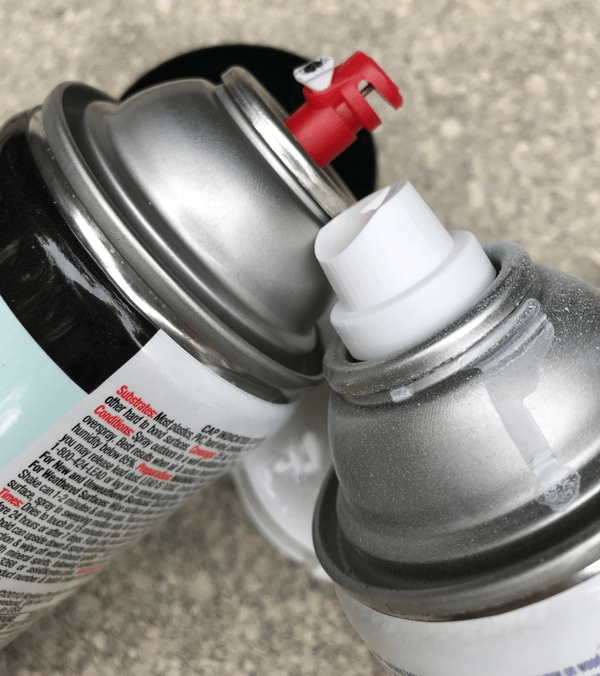
Have a question about a specification or application?
Ask the experts.
Our Technical Service Team is here to help you select the best coating for your application.
Our team can:
Want more in-depth information about our coatings and learn how they improve the performance of products and processes in challenging applications?
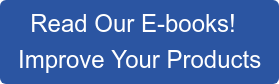