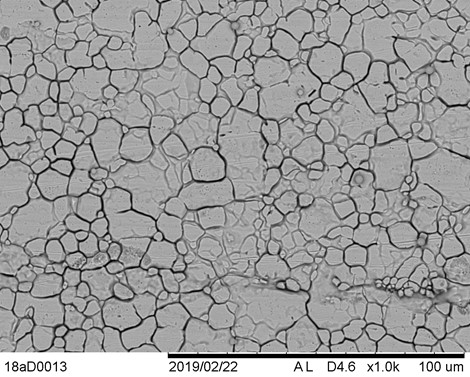
If you've ever taken a really close look at our coatings they may appear to be cracked. Looks can be deceiving so why does the coating appear cracked? We do some sleuthing and solve the mystery of the cracked coupon.
Recently, a customer reached out to SilcoTek® to share a curious observation they made on the SilcoNert® coated evaluation coupons. These were flat 316 stainless steel coupons that we provide to customers for free coating evaluation. The customer examined the coating under the SEM (scanning electron microscope), and saw what appeared to be coating cracks (Figure 1). Could SilcoTek coatings be cracking? Metallurgists will find something very familiar looking in the "cracked" surface.
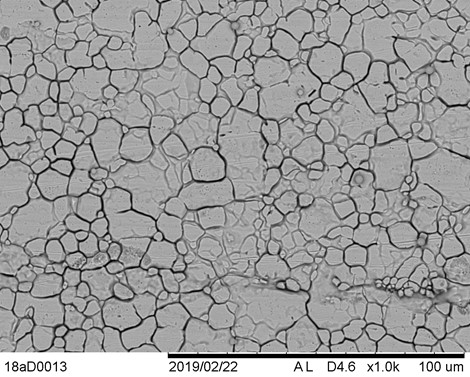
Figure 1) SEM image (1000x) of a SN2000-coated 316SS evaluation coupon shared by a SilcoTek customer
In this blog post you will learn:
How surface morphology & SEM analysis solved a customer "cracking" problem.
How precision CVD coatings can highlight metal grain boundaries.
How metal finishing can play an important role in coating surface appearance but may not impact corrosion performance.
|
The Investigation About CVD Coatings
Upon receiving the customer’s feedback, SilcoTek’s R&D team started an investigation into the evaluation coupons. Samples from different production batches were pulled from the coupon stock for SEM inspection. We also asked the customer to ship the “cracked” coupon back to SilcoTek for further examination.
Get the Report
The initial examination of stock coupons did not find any coupon that exhibited the same “cracked” pattern observed by the customer. Even the coupon returned from the customer did not reproduce the SEM results. Meanwhile, the customer received two replacement coupons for evaluation, and reported similar cracks seen in the SEM of these coupons. What’s going on?
It turns out that the two sides of the evaluation coupons are not equivalent; one side has a mirror-polished finish, whereas the back side has a standard machine-finish (see Figure 2 below). With the coating applied to the surface, it is not always immediately obvious by visual inspection which side has the polished finish. We eventually discovered that observing one’s own reflection in the coupon is the easiest way to identify the two sides.
The SilcoTek internal investigation focused on the mirror side, as the polished side works better for most surface analysis techniques, and has become the “default” side for our characterizations. The customer, on the other hand, looked at the machine-finished side under the SEM. The differences in the finishes of the metal are responsible for this discrepancy.
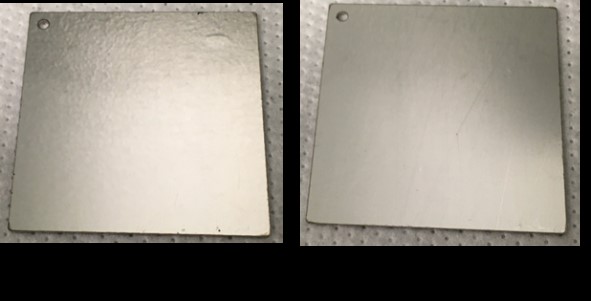
Figure 2) the two sides of an uncoated evaluation coupon
The Discovery
After realizing this, the unpolished side of the return coupon was examined under the SEM by SilcoTek, which revealed the “cracks” described by the customer. These “cracks” are in fact the stainless steel metal grains that become visible under high magnification, and after a mirror polish, are smoothed out and no longer show up under the SEM. Figures 3 and 4 below show both sides under the SEM (1000x) with coating on. To confirm that the “cracks” are indeed from the metal itself, uncoated as-received coupons were also examined under optical microscope, to demonstrate the differences of the two finishes on the two sides. We then conducted corrosion tests to be sure the coating integrity remained intact. Want to learn more about how SilcoTek coatings improve corrosion resistance?
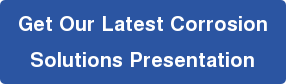
Linear polarization resistance scans using 5% HCl solution as the electrolyte were also performed on both sides of a coated coupon. Actual coating cracks would inevitably lead to poor corrosion performance and would be detected by this test. The measured corrosion currents for both sides were comparable, further confirming the integrity of the coating itself on the non-polished side.
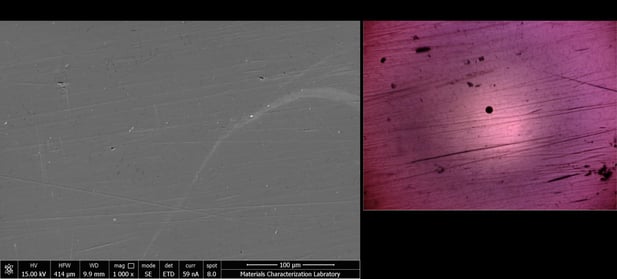
Figure 3) SEM (left) and optical microscope (right) images of the mirror-polished side of an evaluation coupon
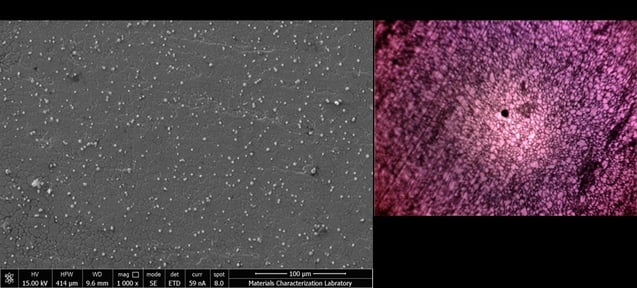
Figure 4) SEM (left) and optical microscope (right) images of the unpolished side of an evaluation coupon
Conclusion:
The reported cracks in the coating observed by the customer in SEM were confirmed to be in fact stainless steel metal grains, as a result of the unpolished surface finish. SilcoTek’s CVD coating is very thin (sub-micron) and in general will not mask the microstructures of the underneath substrate. The features of the metal itself will show up in SEM examinations, and to minimize this, polished surfaces are usually preferred if one wishes to evaluate the surface morphology of the coating itself.
Have a burning question about our coating. Go to our FAQ page, or ask the experts.