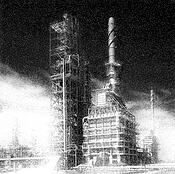
Sulfur in the plant feedstock stream!
My testing protocol didn’t detect sulfur in my plant feedstock, now the catalyst is poisoned! Dead!
This Halloween mystery didn’t have to happen. Compounds like hydrogen sulfide (H2S), carbonyl sulfide (COS), and methylmercaptan (CH3SH) are all too common in natural gas feedstock. Unfortunately these toxic suspects can be difficult to detect. They hide by adsorbing onto the surface of tubing, fittings/valves, regulators, sample cylinders and other sampling surfaces.
Catalyst killers, like H2S, often go undetected in sampling streams because of adsorption to stainless steel, metal alloy, and glass surfaces. Here’s the really scary part of the tale; if undetected H2S, COS, and mercaptans can prematurely deplete catalyst beds, and can cost refiners and olefin plants many millions of dollars in lost productivity and catalyst replacement material.
Unprotected sampling surfaces cannot police lurking sulfurs; like Dracula, they lurk in the shadows and attack their unsuspecting prey without warning.
Drive a stake in the heart of sulfur contamination by coating all sampling surfaces with inert coatings like SilcoNert® 2000 and Dursan®.

SilcoNert® 2000 can improve detection limits by orders of magnitude.
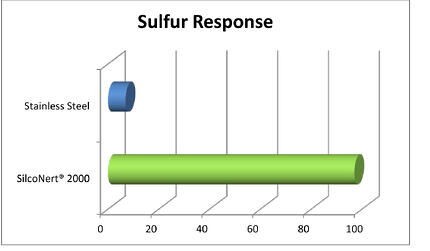
Coat the entire sample surface:
- Tubing
- Fittings
- Regulators
- CEMS GC/detector components
- Sample cylinders
- Valves
|
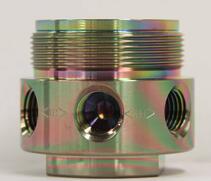 |
Coating sample surfaces will also drive away the evil spirits, corrosion and moisture. Like a poltergeist, corrosion and moisture will shake the foundation of a sample system and cast a shadow over a robust sample system. SilcoTek® coatings improve corrosion resistance and repel water, driving away those spirits.
.jpg?width=398&name=corrosion_comparison_in_HCl_(4).jpg)
Hydrochloric acid immersion demonstrate significant corrosion improvement of Dursan® and Silcolloy® coating over steel and steel alloys. Protecting refining and olefin sulfur sampling systems and catalysts.
Learn more about how SilcoTek® coatings improve performance in refining and petrochemical operations.
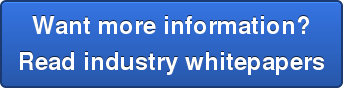
Happy Halloween!
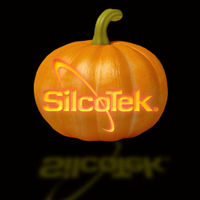.png)