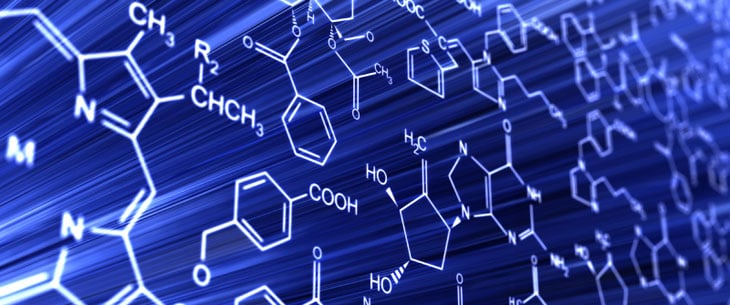
How is it that getting an analytical sample from the source to the analyzer, GC, or LC seems to be just as hard as doing the separation? When things go South there seem to be any number of variables and potential sources of problems. Here are some tips for identifying and fixing sources of junk data.
But before we dive into analytical problems, the SilcoTek team would like to offer our thoughts and prayers to all those impacted by recent hurricanes. Just about everyone knows someone impacted by the storms. We hope friends and family are safe and lives rebuild quickly.
Friday 9/15/17 is also a special day for SilcoTek®. The Cassini mission completed it's Grand Finale by plummeting into Saturn's atmosphere. A spectacular end to a even more spectacular and successful project. Our coatings played a small part in that success. SilcoTek coatings were part of the analytical system on the spacecraft, creating an inert flow path & assuring accurate and reliable data. Read or blog post about Cassini. You can see the mission's last images here. Good by old friend, we shall miss you.
1. Identifying analytical test problems
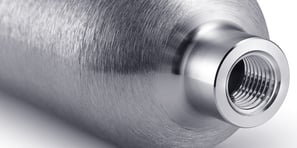
Too small a peak, too many peaks, not enough peaks, inconsistent results, too consistent a result, elevated baseline, crazy looking peaks they all add up to junk data. That junk data can come from all sorts places. Here are just a few sources of bad data (the impact or importance of each variable depends on your application, environment or business):
- Ion contamination from leached metals, corrosion, or sample contamination.
- Bio contaminants
- Plastic contamination (A real pain, especially on glass)
- Cosmetics (not just makeup, it can be hair gel, you know who you are fellas...)
- High molecular weight volatiles
- Hydrocarbons
- Water condensation (can take up sample and form acids, in the case of H2S or Sulfurs)
- Carryover from proteins or other sticky analytes
- Adsorption from active surfaces like glass, stainless steel. ceramics, etc. (Our specialty...)
- Leaks in the system
- Flow problems or plugged flow path.
- And many more!
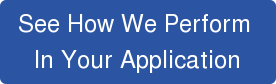
The result? A Squirrel?
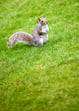
You can get some pretty squirrelly looking results from an under performing sample transfer system. For the scope of this blog post, by sample transfer we're talking every point from the sample origin to the column. Some of the many symptoms include:
- Split peaks (Contamination)
- Tailing (Contamination)
- Irregular or irreproducible response (Contamination)
- Ghost peaks (Carryover)
- Noise (Air leak or Contamination)
- Drift (Variable gas flow rates)
- Baseline elevated (leak in system)
- Baseline offset (Sudden change in baseline position, Contamination)
- Spiking (Particulate matter)
- Retention time shifts (leak in injector)
|
- Baseline Wander / low frequency noise (Contamination or Environmental)
- Waves baseline oscillations (Contamination)
- Reduced peak size (Clogged syringe or flow path, reactive surface or leaks)
- Negative peaks (Hydrocarbon contamination)
- No peaks (Clogging)
- Missing peaks (Activity/Adsorption)
- Added peaks (Carryover or contamination)
- Tailing (Contamination)
|
Ugh, solving this problem will be like eating an elephant! Impossible you say? Nope, you eat an elephant one bite at a time. If eating elephants are your thing... With that in mind here are a few tips for solving analytical test problems.
2: The fix
There are many symptoms but really a systematic troubleshooting method will do wonders for your sanity. If you have no idea where a potential analytical sample system problem is; divide the system into logical troubleshooting areas that can be isolated for leak checking, inertness testing, and visual inspection. We'll start from the sample inlet end and work back toward the analyzer in this example.
Troubleshooting guide for GC
Troubleshooting guide for HPLC
Sample Inlet: This may be a simple auto sampler needle or a complex stack probe. The sample inlet should be inspected for clogging, contamination, rust, and inertness. Yes we'll throw in adsorption issues at the inlet. In the case of our inert coatings like Dursan®, SilcoNert®, or Silcolloy® check the surface for loss of that fancy rainbow color or loss of iridescence. If the surface has lost it's color or brightness, has scratches, particulate build-up, or corrosion that could be the source of adsorption or contamination. Check septa for damage & the needle for bits of septa it could be disrupting flow.
Conveyance:
By conveyance I'm talking about whatever is used to get the sample from the source to the instrument, that could involve heat trace tubing, a sample cylinder, or transfer tube. Check for leaks, avoid using Snoop or soap solutions, that stuff can be sucked into the sample system and cause more contamination problems. Use a leak detector to check for leaks. Be sure fritted filters are not clogged or contaminated. Filters should be protected with an inert coating. The surface area in a small fritted filter is immense, so it makes sense to minimize potential adsorption, corrosion and sample loss by making the filter inert.
Is the heat trace or transfer tubing inert and free of corrosion or particulates? Don't think that because the tube is PTFE that you're in the clear. PTFE can cold flow, or degrade with heat, causing restrictions in flow that can lead to clogging. Also PTFE is porous which can provide great places for particulates and sample to hide and later contaminate the system.
- Check fittings for inert coating, if the fittings have lost their color or appear to be damaged, it's a good bet that the tube could have lost it's inert coating as well.
- Check disassemble and check sample cylinder valves, filters, and interior surface. Pay special attention to threads and the shoulder area of the sample cylinder. Check for rust and particulates that can adsorb analytes.
- Look for signs of moisture contamination throughout the system if you notice droplets/contamination heat the system and purge with nitrogen to remove moisture. Refiners should avoid using steam to blow out systems. Steam can damage inert surfaces and deposit particulates in the flow path.
- Be sure ampules are precleaned and not exposed to plastics or contaminants that can be leached into the sample. If testing reactive compounds, be sure the ampule is inert.
- Check injector needles in auto samplers for clogging. Septa can clog needles and cause flow problems. Check needles for corrosion and pitting, some auto sampling cleaning solutions can corrode/pit surfaces which can lead to carryover and analyte sticking problems and cross contamination.
- Instrument flow path components like weldments, sample loops, liners should be inert and contaminant free. Exposed, untreated stainless steel surfaces can be adsorptive to alcohols, diols, amines, sulfurs and other reactive analytes. Be sure instrument flow paths are coated with and inert coating like SilcoNert® or Dursan® to be sure activity is minimized.
Don't forget the calibration system!
- Cal gas is specified pure, but the flow path is not. So be sure valves, filters, regulators, tubing and fittings are SilcoNert or Dursan coated to avoid misleading calibration problems.
By now you've probably found the problem. If not contact the instrument company, column company or other sources for troubleshooting help.
3: Prevent analytical test problems
The building blocks of good process analytical management and prevention of analytical test problems lie in developing an understanding of how your system performs under your plant, environmental and lab conditions and then designing quality solutions into the process. Key factors are:
- Understanding failure mechanisms and tailoring system design to facilitate management of failure mechanisms.
- Managing adsorption of analyte
- Product component effect on quality
- Understanding and managing the sources of variability
A well thought out analytical system that designs quality into the process from the start will save the plant operators and lab managers time and money. Quality designed in from the start encompasses all factors from material selection, system design/layout, component selection, installation, and data management.
Material selection
Good sample transport system design incorporates multiple factors in material selection including corrosion resistance, surface inertness/adsorption, functionality, workability, durability, and cost. Stainless steel is the go-to material for sampling transport systems because it checks most but not all of the design boxes. Stainless is relatively cheap, durable, it's a workable metal, plentiful, and every machine shop knows how to work with it. Unfortunately stainless steel can corrode and adsorb test analyte, causing inertness issues, contamination and premature system failure.
Inert coatings are used as a backstop to stainless steel's weak points. The result? Improved process measurement quality and durability. Start by selecting the right coating for the application. Select the coating based on:
- System exposure/environment
- Target performance (ie. corrosion, ppm or ppb inertness, etc.)
- Cleaning method/exposure to cleaners
- Analyte
- Maintainability
- Expected life of the sample system
Use our quick guide to help select the right coating material for the application.
Make Your System Perform
Get Our Coating Selection Guide
Manage corrosion
To assure corrosion resistance and inertness coat analytical flow paths with inert materials that will not interact with analyte or cleaning materials and will act as a barrier to corrosive effects. Comparative immersion tests of Dursan® and stainless steel in 6M hydrochloric acid demonstrate the high corrosion potential of stainless steel.
Get Our Latest Corrosion
Solutions Presentation
Corroded stainless steel surfaces can produce adsorptive particulates as well as damage system operating integrity, inert coatings like Dursan coated flow paths prevent corrosive attack by orders of magnitude.
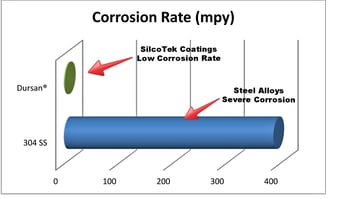
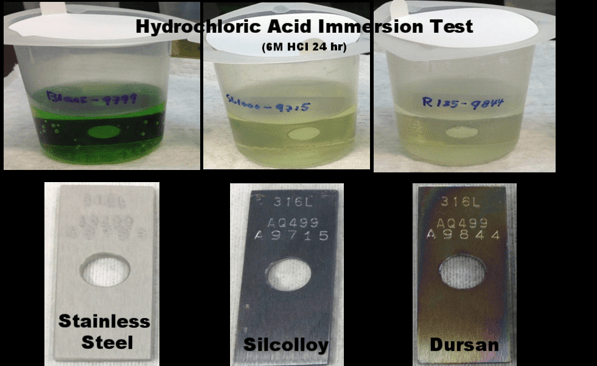
Manage inertness
Sticky compounds like H2S, mercaptans, even protein molecules can adhere or be adsorbed by stainless steel. Even in high velocity flow paths, compounds can stick to the surface; causing inaccurate results. Inert coatings like Dursan® and SilcoNert® prevent surface interaction with stainless steel allowing all the sample to reach the analytical instrument.
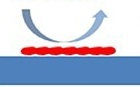
Compounds can stick to stainless steel
even in high velocity flow paths
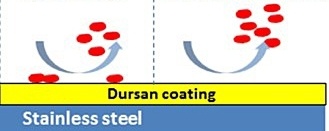
Dursan coated flow paths prevent adsorption and sticking;
offering part-per-million inertness even under extreme conditions.
Manage adsorption/desorption effects
Adsorption and subsequent release of active compounds in the sample transport system can severely distort analyzer results. Failure to manage adsorption can cause seemingly random spikes and dips in analyzer readings. Sample flow through uncoated stainless steel tubing can result in delays in response or false negative results. Delays of 90 minutes or more can result from adsorption of the sample.
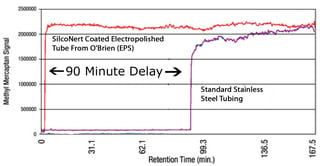
After the delay in response, sulfur and other sticky compounds can desorb or release from the surface; causing spikes in analyzer readings.*
Design factors For Improved Process Analytical Performance
A recent paper by Phil Harris, Haritek, and O'Brien Analytical highlight how common sample transport design issues could distort analytical results. More importantly the paper recommends ways to improve sample system reliability.
Read How To Improve
Sample Transport Systems
Robust sample transport design
The Harris study notes key factors when specifying the sample flow path. Factors to consider are:
- Species to be analyzed,
- Sample gas composition and dew point / phase behavior,
- Length of the sample line run,
- Operating pressure and temperatures,
- Required gas velocities and response times
- Material compatibility.
Proper flow path design will avoid common sampling system failures like:
- False analyzer readings
- Slow calibration or inability to calibrate system
- Variable readings
- No results, then spikes in readings
- Frequent maintenance and component replacement
- Poor system durability and wear resistance
Read About Dursan
Wear Resistance
Manage moisture
Adsorptive water molecules can bond to stainless steel surfaces, especially oxidized stainless steel. An inert hydrophobic surface like Dursan® will repel moisture and prevent water from adsorbing analytes.
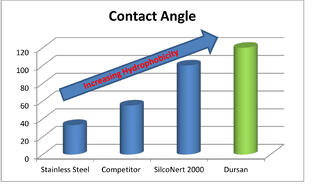
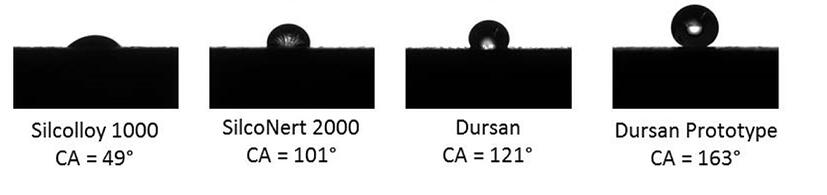
Product component selection and minimizing variability
Understand system component functionality and performance thoroughly. Is that cheap regulator made with low quality stainless steel? What is the optimum performance envelop of the component. Can the plant maintenance and engineering staff install and maintain the component? Can the component be installed properly in a repeatable fashion? These questions apply to complex continuous emission monitors but also to seemingly simple components like fittings or tubing. A sample transport system is only as effective as it's weakest link. A single adsorptive fitting or filter can impact system performance for years if not properly identified and controlled.
Build Quality Into The Process: Coat the entire sample flow path
Coat all surfaces with an inert coating like SilcoNert® or Dursan® to prevent common sample transport issues like corrosion, adsorption, moisture contamination and slow response. Coat the following flow path components:
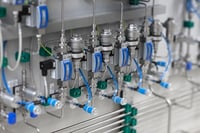
|
Filters
Regulators
Tubing
Valves
|
Fittings
Sample Cylinders
Dip Tubes
Probes
|
It's easy to buy inert coated sample system components, just ask your supplier or go to our Buy Coated Products page to learn more. Building quality in to your process analytical system has never been easier!
Buy Coated Products
Directly From The Manufacturer
*Data courtesy of Shell Research and Technology Centre, Amsterdam and O'Brien Analytical