SilcoTek inert, corrosion resistant, hydrophobic and icephobic CVD coatings benefit hydrogen use and production by improving trace detection of sulfurs, ammonia, and other reactive compounds. They allow hydrogen process facilities, transport systems, and downstream users to reliably detect potentially catastrophic and damaging contaminants. SilcoTek coatings also enable users to detect emissions of target contaminants at trace levels, which improves emission compliance. SilcoTek coatings can also boost the water repelling and ice removal properties of flow path surfaces, improving moisture management, minimizing water retention, and mitigating ice formation and removal problems.
Why test hydrogen fuel quality?
A passivated surface will reduce surface reactivity and adsorption. This improves test accuracy and overall test reliability. But what are the consequences of an inaccurate test? Contaminated fuel can damage fuel cells and engines as well as damage catalysts. Not to mention that off-spec fuels can can be a real liability for the supplier. So, it's in everyone's best interest to test as accurately as possible.
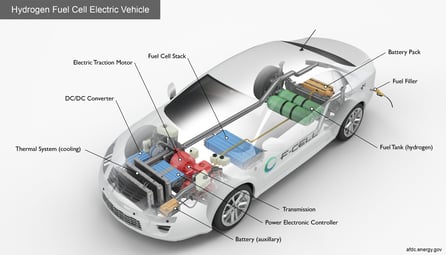
The consequences of inaccurate hydrogen fuel testing in fuel cells:
- Fuel cell damage due to poisoning
- Reduced fuel cell performance
- Increased maintenance
- Cell failure
Trace level contaminants can have a real effect on overall system performance. A reactive flow path can adsorb many trace contaminants, which will lead detection failures. Without precise testing, hydrogen contamination will continue and ultimately lead to system failures. That's why it's important to select flow path materials that prevent adsorption of hydrogen contaminants.
Trace Sulfur and Sulfur Compound Detection
Stainless steel is a material commonly used in hydrogen production and transport systems. Unfortunately, sulfur (one of those natural gas contaminants) is readily adsorbed onto stainless steel flow path surfaces, which makes detecting and managing sulfur poisoning more challenging. Sulfur detection is generally a manageable problem when testing at higher concentrations, usually at higher percent levels but at trace levels, detection is much more difficult.
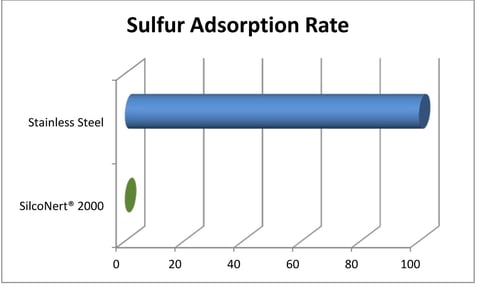
Unfortunately, hydrogen catalysts are vulnerable to trace level sulfur poisoning. The damage from sulfur can add up quickly, resulting in reduced efficiency and shorter catalyst life, which are both very expensive results. This makes testing for even trace level sulfur essential to cost efficient hydrogen production and use.
When testing for sulfur using materials like stainless steel, metal alloys, or even glass, the sulfur is adsorbed in the flow path and never reaches the sulfur detector. This results in reduced sulfur response at the detector and a false negative test, when in fact the feedstock stream may be poisoning the catalyst.
The flow test plot below demonstrates how various surfaces perform in trace sulfur analysis. The coated surfaces provide a fast response and result in a higher detection signal when compared to uncoated stainless steel.
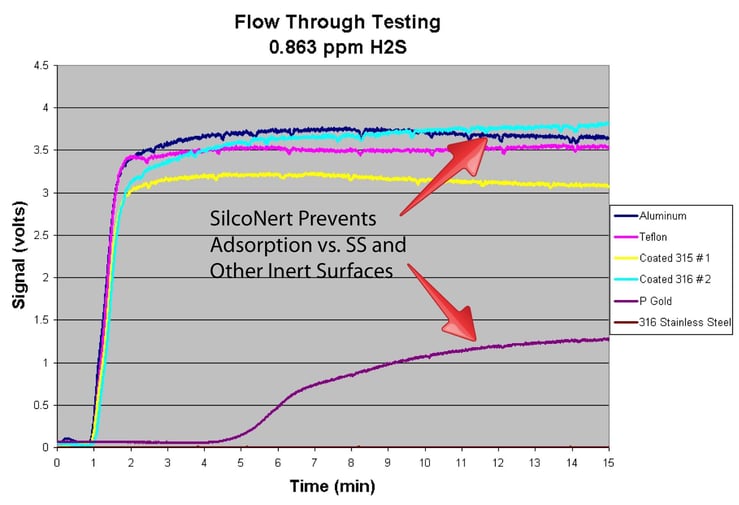
SilcoNert® coating radically improves sulfur response over uncoated stainless steel in analytical systems. This helps to maintain consistent and reliable detection, keeping hydrogen processing and fuel cell catalysts safe from poisoning.
/Sn2k%20v%20ss%20sulfur%20response.png?width=369&name=Sn2k%20v%20ss%20sulfur%20response.png)
Ammonia Detection
Like sulfur contamination detection, improved ammonia detection can also contribute to preventing damage to catalysts. SilcoNert improves test reliability and lowers the detection limit of ammonia, helping to detect ammonia contamination before catalysts are damaged.
A University of Helsinki study found that SilcoNert improves the trace detection of ammonia by 95% when compared to uncoated 316L stainless steel. Improved detection will enable refiners and users to better manage hydrogen fuel quality and maintain high efficiency in production and use.
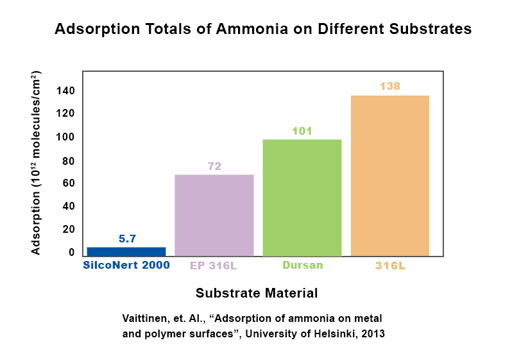
Inert Gas Detection
Some gases may not physically harm production, transport, or use, but can reduce the energy density of hydrogen fuels. Reliable detection of nitrogen, N2, or other contaminants assures hydrogen powered systems run at peak efficiency.
Emissions Detection
Advances in instrumentation and test procedures help, but inert surfaces like SilcoNert® and Dursan® enable testing agencies to repeatedly detect part-per-million and part-per-billion levels of NOx, sulfurs and other emissions.
The California Energy Commission conducted a study comparing SilcoNert (noted as Silcosteel® in the study) to other materials commonly used in sampling systems. The results show the SilcoNert coated surface reduces surface reactivity with NOx, sulfurs and other common emissions, enabling more reliable testing of trace emissions.

Water and Ice Management
Hydrophobic coatings, like Notak®, repel water and ice to help to maintain a water free surface. This helps to control moisture contamination in hydrogen production, fuel delivery, and use. Notak prevents moisture carryover by preventing trace water from attaching to hydrogen flow path surfaces and hydrogen sampling flow paths. This allows the user to detect moisture before it becomes a problem in hydrogen manufacturing and transport flow paths.
The goniometer water contact evaluation below compares hydrophobicity data of various SilcoTek coatings. The water repelling properties of Notak, evident in the water droplet and 143° contact angle, prevent wetting and water retention of the stainless steel substrate. For reference, an uncoated stainless steel water droplet surface contact angle ranges from 30° to 40°, making stainless steel a wettable surface that can retain water in tubing, valves, filters, and other flow path surfaces.
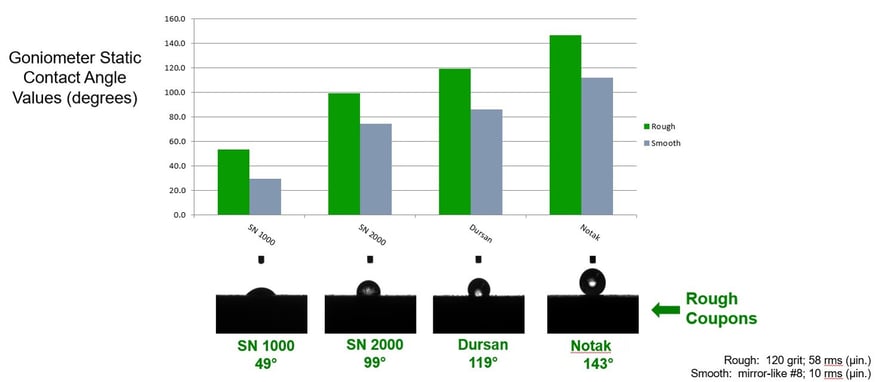
Ice formation and removal is also a problem in hydrogen storage and transport. Surfaces with ice repelling or icephobic properties help operators to manage the accumulation and removal of ice. The ice repelling and removal properties of Notak® coated stainless steel are compared in the photo and table below. The frozen Notak droplet has the highest contact angle when compared to other coated and uncoated surfaces, indicating an icephobic surface.
Need help finding the right coating for your application? Check out the coating selector guide below.

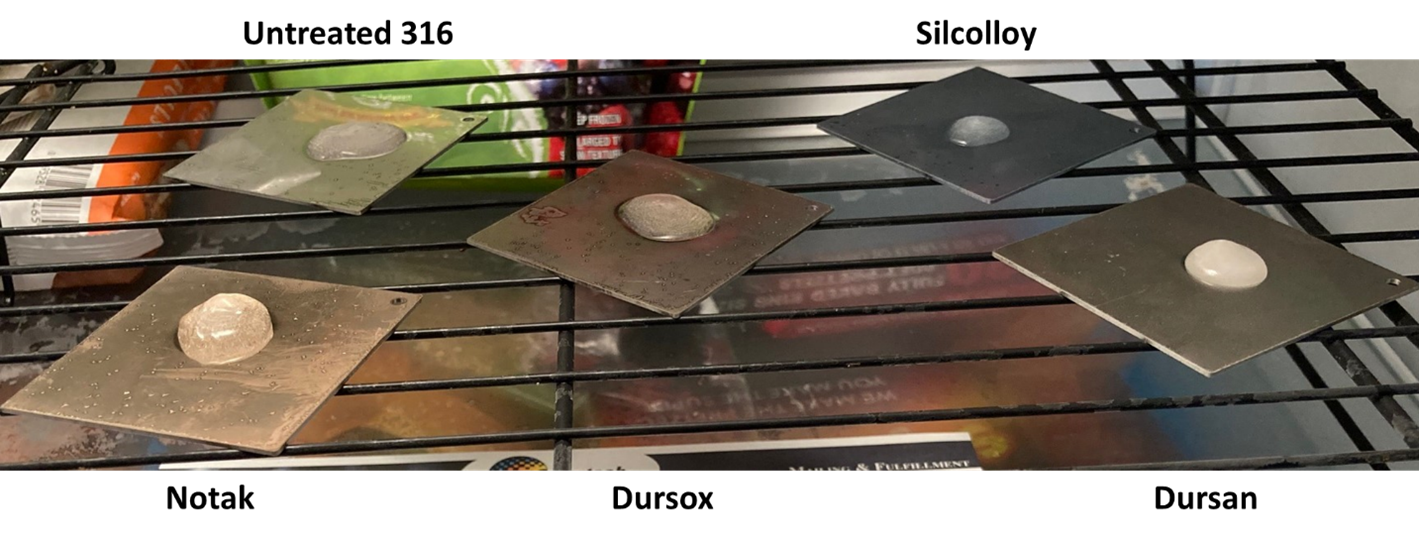
Notak also made ice removal easier. After freezing coated and uncoated metal coupon samples, a metal pick was inserted at the point of ice attachment to the coupon. Gradual increasing force was applied laterally to the ice sample until the ice dislodged from the surface. The effort required (1 = easy, 10 = difficult) to remove the ice and associated observations are listed in the table below.
316 SS Coupon Surface
|
Effort (1-10)
|
Observations
|
Notak®
|
2
|
complete removal with little effort
|
Dursan®
|
6
|
partial removal from surface with effort
|
Silcolloy® 1000
|
7
|
partial removal from surface with greater effort
|
Dursox®
|
8
|
difficult, bulk chipped with minimal surface separation
|
Uncoated
|
8
|
difficult, bulk chipped with minimal surface separation
|
The ice and water repelling property tests demonstrate how SilcoTek coatings can improve moisture detection, reduce accumulation of water in flow paths, and help to make ice removal from surfaces easier.
Corrosion Resistance
SilcoTek corrosion resistant barrier coatings prevent flow path surface interaction with corrosives, effectively extending component life while preventing hydrogen contamination. Our corrosion resistant coatings, Silcolloy®, Dursox® and Dursan®, are particularly useful for fighting corrosion in high purity or otherwise sensitive processes fou
nd in hydrogen production, transport, and use.
In addition to extending the usable life of precision stainless steel parts, SilcoTek coatings prevent nano-scale corrosive reactions that can cause metal ion leaching and contamination, ultimately increasing process yield and reducing failure rates.
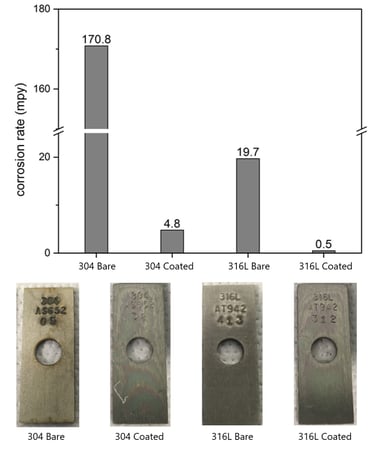
Because hydrogen reacts with most elements, hydride formation may be a concern in hydrogen production, transport, and in downstream power systems. Our coatings act as a barrier to reduce or prevent ion leaching and interaction of flow path substances with the metal substrate. In the example graph below, methanol (CH3OH) extracted metal ions from uncoated alloy surfaces. Metal ion extraction can contaminate flow path fluids and may result in system corrosion.
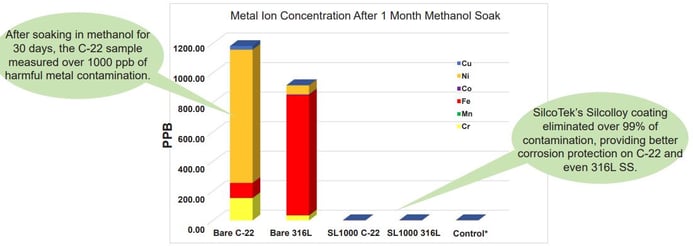
Conclusion
SilcoTek coatings contribute to the hydrogen economy by enhancing contaminant detection, improving system reliability, and better system operation. Overall coating contributions to the hydrogen economy include:
- Detection
- Detecting impurities in hydrogen fuel samples.
- Hydrogen quality monitoring.
- Accurately detecting emissions from current hydrogen production methods in refineries.
- Permeation barrier / purity
- Stability of hydrogen in storage; reducing contamination from storage materials.
- Maintaining purity of hydrogen by preventing corrosion of storage and processing components – electrolysis, marine/salty environments, etc.
- Slowing/preventing hydrogen embrittlement of metals.
- Improved dielectric properties.
- Potential benefit to tritium permeation.
- Production
- Contribute to the control desired/undesired catalysis and improved detection of catalyst poisoning.
- Environmentally-friendly hydrogen
- Our coatings complement the “green” hydrogen effort; our coatings are inert and do not introduce additional contaminants or potentially harmful substances into the hydrogen process while enhancing the performance of components and flow paths used to produce, transport, and use hydrogen energy.
- Physical improvements
- In some applications, SilcoTek coatings improve friction and durability properties. Sliding Rings, pistons, sliding valves and other components used in compressors or other process components could benefit from using SilcoTek coatings. Improve water detection and icephobicity in hydrogen flow paths.
The overall value of using our coatings in the hydrogen economy results in reduced cost and improved efficiency of hydrogen use and production.
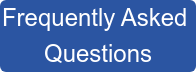