
Metals can leach ions into process streams, contaminating product, impacting yield, and damaging processes. In this blog we discuss metal ion leaching and how to prevent contamination.
Preventing Metal Contamination in Products and Processes
Metal ion leaching is of interest to a variety of industries. Chemical exposure to solutions, such as, organic solvents, deionized water, acids or bleach, can cause a significant amount of metal ions to dissolve into the liquid, causing product contamination, system corrosion, and test problems in analytical and high purity processes including:
- Catalyst protection in oil and gas operations
- Catalyst monitoring and protection in renewable energy applications
- Semiconductor Manufacturing
- Biopharmaceutical Production
- Medical Diagnostics
- Precision Cleaning
- Food and Beverage Processing
- HPLC Analytical Flow Paths
In this blog post we'll briefly review studies we've conducted to evaluate metal contamination in various commonly used chemical environments. We'll also discuss how SilcoTek® coatings act as an inert and corrosion resistant barrier that will prevent metal surface exposure and leaching of metal ions into sensitive processes.
In this blog post you will learn:
- How SilcoTek® coatings prevent metal contamination.
- How various commonly used chemicals can leach metal ions.
- How various metals, like stainless steel, Hastelloy®*, titanium, and more, perform when exposed to solutions that can leach metal ions.
|
SilcoTek Coatings and Preventing Metal Contamination
SilcoTek® offers CVD coating solutions to make your process, analytical testing, and sampling systems perform better. Our chemically inert coatings improve test accuracy and reliability by preventing contamination from metal ion leaching caused by chemical reactions between the sample and flow path surface. The summary below demonstrates how metal ions can be readily leached into flow path solutions and how coated surfaces (right column, green) prevent contamination under all conditions tested.
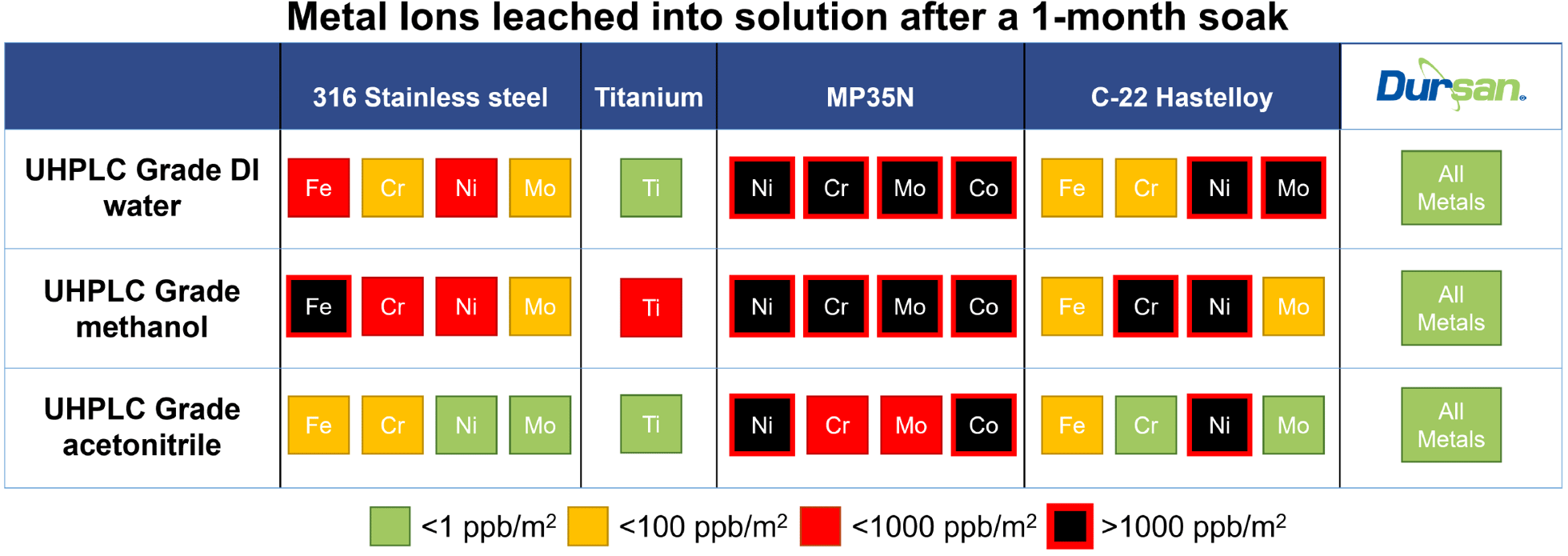
SilcoTek's CVD silicon coating process bonds inert, non-reactive coatings like Dursan®, Silcolloy®, and SilcoNert® to the surface. The chemically inert coatings prevent interaction of the sample with the reactive flow path surface.
SilcoTek has conducted several studies relating to effectiveness of our CVD coatings in preventing metal ion leaching from various surfaces when exposed to organic solvents and deionized water. Read the Technical Insights below to further understand how SilcoTek coatings improve product and test quality.

Metal Contamination in Deionized Water Systems
In this study we investigate DI water’s impact on titanium, Hastelloy®, and stainless steel. Among numerous other uses, DI water is commonly used as a solvent for HPLC analysis, in food and drug production, in high purity ultrasonic cleaning, and as a precursor in semiconductor applications.

Results of the tests show that titanium alloys do not suffer metal ion leaching in DI water, while both stainless steel and Hastelloy show large amounts of metal ion leaching, specifically an abnormally large amount of nickel leached into DI water when compared to the methanol leaching studies.
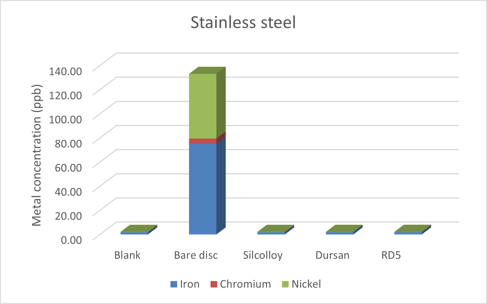
Methanol and Stainless Steel Metal Contamination
This Technical Insight investigated whether Dursan® and other SilcoTek® coatings can prevent metal ions from leaching into pure organic solvents.

The study showed that high purity organic solvents like methanol can cause contamination and corrosion in stainless steel flow paths. Coated stainless steel surfaces prevent ion leaching, corrosion, and contamination of analytical test and process streams.
Hastelloy Metal Contamination
In this study we find that a bare C-22 sintered disc when exposed to pure methanol can leach over 1 ppm total metal into solution, where the same discs coated with Silcolloy®, Dursan®, and a test coating, RD5, showed no measurable loss of metal ions, indicating only baseline levels of leaching relative to experimental controls.

SilcoTek® coatings prevent Hastelloy ion contamination when the surface is exposed to organic solvents like methanol. SilcoTek coated surfaces show a significant improvement in purity, with very low ion contamination.
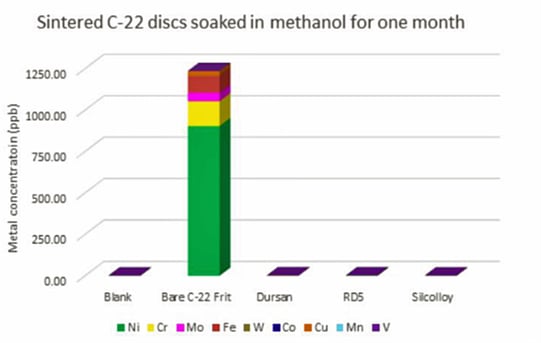
Titanium Metal Contamination
In this study titanium is investigated as a substrate for SilcoTek’s coating protection. Titanium is commonly used as an alternative to stainless steel due to it being lighter, strong, and biocompatible. We find that Silcolloy performs well as a barrier, but Dursan and a test coating,RD5, do not provide adequate protection.

Test results showed the Silcolloy® coated titanium sample improved the resistance to ion contamination in methanol.
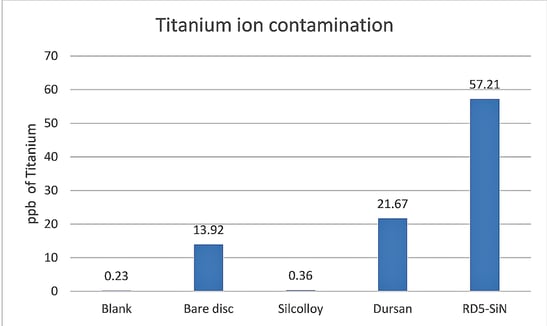
Alloy MP35N Leaching
In this Technical Insight, we investigate MP35N exposed to ultrapure HPLC grade methanol, acetonitrile, and DI water. MP35N is a nickel-cobalt based alloy which has been growing in popularity among HPLC and medical instrument OEMs. It is marketed for the alloy’s high strength, corrosion resistance, and biocompatibility. The study evaluates metal ion leaching in the three most common solvents used in HPLC applications: methanol, acetonitrile, and water.

The results of the study indicate acetonitrile is the most benign solvent. The MP35N alloy seems to follow the trend of another nickel based alloy, Hastelloy, in that water shows the most metal ion leaching of any solvent.
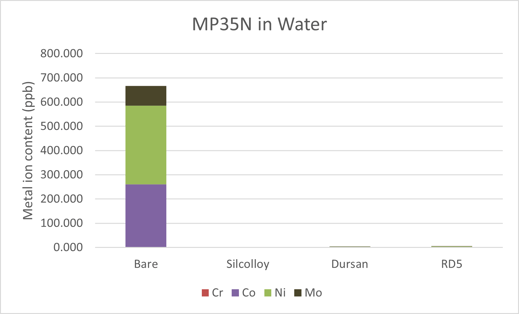
Conclusion
Our immersion studies show that commonly used metals can leach significant amounts of metals into process streams. SilcoTek® coatings act as an inert barrier, preventing fluid interaction with the base metal. This prevents metal contamination in many applications including:
- Catalyst protection in oil and gas production and renewable energy
- Semiconductor etch operations
- HPLC systems
- Food flavors and fragrance production
- Pharmaceutical production
- Bio medical
To learn more about how our coatings improve corrosion resistance, system purity, and inertness in your industry go to our Applications page.
Have questions about how to prevent metal contamination, improve the purity of your products or processes or want to improve the corrosion resistance of your products? Contact our Technical Service Team to discuss your application. Or follow us on LinkedIn and subscribe to our blog to stay in touch with the latest in advanced coating technology.

*Hastelloy® is a trademark of Haynes® International