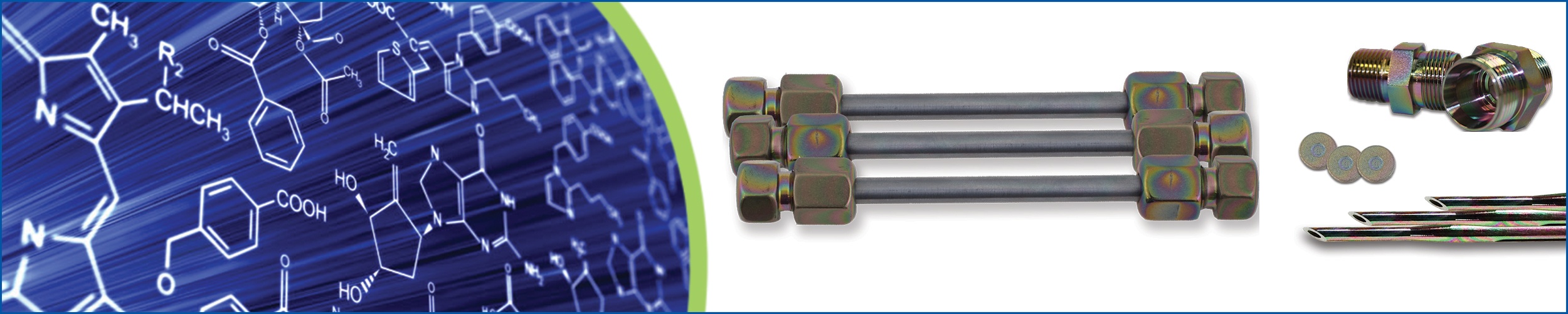
In part 6 of our ion leaching series, we discuss how alloy MP35N performs in high purity organic solvents and DI water, with surprising results!
Metal Ion Leaching Alloy MP35N
MP35N is an alloy that is increasing in popularity among the medical diagnostic and HPLC community. It is often used as a bio-inert solution for replacing stainless steel as its iron content is very low. While it may be bio-inert in the sense of it does not have any cytotoxic or deleterious effects on biological analytes, it is still made of metal. More and more HPLC users are finding that bio-inertness by replacing one metal alloy with another does not fix their issue of metal ion leaching into their flow path. Here we investigate the metal ion leaching of MP35N in pure methanol, water, and acetonitrile.
In this blog post you will learn:
How alloy MP35N performs when exposed to high purity organic solvents.
How DI water will leach metal ions from MP35N.
How a silicon barrier coating can prevent metal contamination and corrosion.
|
Background:
Previous Technical Insights have investigated metal contamination from common alloys for HPLC and other applications and pure solvent systems. So far, we have investigated water, acetonitrile, and methanol’s impact on stainless steel, titanium, and Hastelloy. Part one through five of this study can be found here:

In this blog post, we investigate MP35N exposed to ultrapure HPLC grade methanol, acetonitrile, and DI water. MP35N is a nickel-cobalt based alloy (see Table 1 for the composition of this alloy) which has been growing in popularity among HPLC and medical instrument OEMs. It is marketed for the alloy’s high strength, corrosion resistance, and biocompatibility. Here we investigate metal ion leaching in the three most common solvents used in HPLC applications: methanol, acetonitrile, and water. As seen in Part 5 of this series, acetonitrile is the most benign solvent. Additionally, the MP35N seems to follow the trend of another nickel based alloy, Hastelloy, in that water shows the most metal ion leaching of any solvent.
Table 1: Weight percentage of MP35N alloy. “Other” elements include iron, titanium, silicon, and manganese.
|
Nickel
|
Cobalt
|
Chromium
|
Molybdenum
|
Others
|
MP35N Weight %
|
33-37
|
Balance (29-36.5)
|
19-21
|
9-10.5
|
2.5 max
|
Data and Discussion Metal Ion leaching Alloy MP35N:
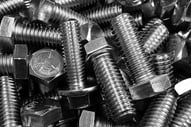
Previous experiments were done with sintered discs due to the high surface area of a porous material. After checking with numerous sintered filtration companies, it seems as though MP35N sintered materials are not common or available yet. Since sintered discs were not available, MP35N bolts were purchased and cut into half inch cylinders.
The sectioned pieces were cleaned via SilcoTek’s standard surface preparation process. The pieces were then left bare or coated with Dursan®, Silcolloy®, or RD5. Each coated and bare cylinder were placed in separate polypropylene containers with 50 mL of HPLC grade methanol, acetonitrile, or DI water purchased from MilliporeSigma.
After one month of soak time, the cylinders were removed from the solvents and those liquid samples were delivered to the Energy and Environmental Sustainability Laboratories at Penn State University. Methanol and acetonitrile samples were then prepared by evaporating the solvent and redissolving the remnants in dilute nitric acid. The water samples simply had nitric acid added to the correct pH for analysis. These samples were then analyzed using a Thermo Fisher iCap RQ ICP-MS.
Interested in learning more about how to improve the corrosion resistance of your products?

The metal ion content leached into methanol can be seen in Figure 1. Roughly 12 ppb of metal ions were released into the methanol after one month of the coupons soaking in solution. Nickel and cobalt were the major contributors to these contaminants. The coated versions all showed low counts, all on similar levels to the methanol from the bottle itself. For instance, Silcolloy, Dursan, and RD5 showed 0.796 ppb, 0.815 ppb, and 0.988 ppb of nickel, respectively. The methanol with no coupon soaked in it for a month showed 0.824 ppb. This shows that all three coatings block the corrosion of MP35N in methanol.
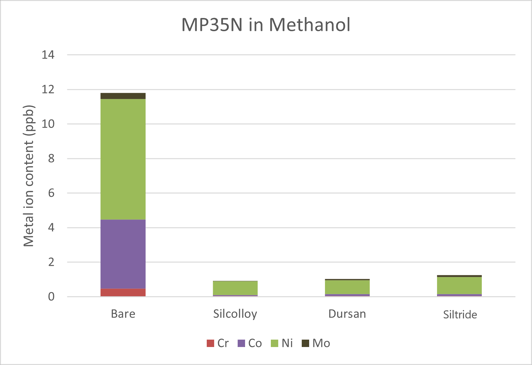
Figure 1: Metal ions leached into methanol solution after one month of soak time. The coated samples were all at or near baseline levels of the methanol in the bottle.
Table 2 shows a comparison of the four alloys that have been tested to this point in methanol. The alloys were all different sizes, weights, and the MP35N samples were solid materials rather than porous material. Most corrosion calculations take surface area into consideration (see ASTM G31 guidelines for immersion corrosion). The higher amount of surface that interacts with the liquid, the more likely a corrosion event is to take place. The last column of the table is total metal ions adjusted for surface area of the samples.
Table 2: Concentration of metal ions leached into methanol among the four different alloys tested. Blank boxes were either not measured or not detected. The final column is adjusted for surface area of the samples that were tested. All values are in ppb.
Alloy
|
Fe
|
Ni
|
Cr
|
Mo
|
Co
|
Ti
|
Total metal per m2
|
Stainless steel
|
812.81
|
61.48
|
33.55
|
---
|
---
|
---
|
1011
|
Titanium
|
---
|
---
|
---
|
---
|
---
|
13.92
|
696
|
Hastelloy
|
101.04
|
902.54
|
151.16
|
49.88
|
0.6
|
---
|
8031
|
MP35N
|
---
|
6.969
|
0.474
|
0.363
|
4.005
|
---
|
100255
|
The results in acetonitrile can be found in Figure 2. There was a total of 1.73 ppb of metals leached into the acetonitrile solution. Compared to both methanol and water, acetonitrile appears to be the most benign solvent toward the alloys tested. Once again, the three coatings all provided sufficient protections against the leaching of metal ions into acetonitrile. All coated values were at the same level as the acetonitrile blank from the bottle.
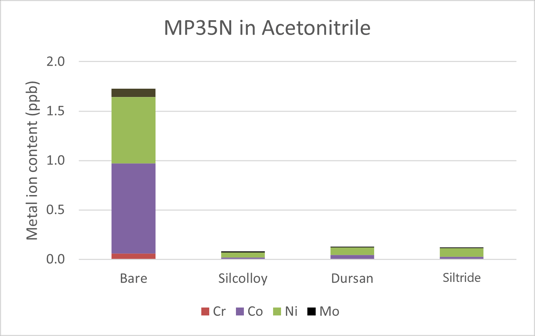
Figure 2: Metal ions leached into acetonitrile solution after one month of soak time. The coated samples were all at or near baseline levels of the methanol in the bottle.
Table 3 shows a comparison between the four different alloys tested in this series. Once again, the last column is adjusted for the surface area of the sample in the acetonitrile. While the total metal content is much lower in acetonitrile than it is for methanol, the pattern among the four alloys is the same.
Titanium shows the least amount of metal ion contamination followed by stainless steel. Both of these alloys are capable of creating stable oxides on the surface of the alloy (titanium oxide for titanium and chromium oxide for stainless steel). Oddly enough, nickel-based alloys, which are marketed as having superior corrosion resistance, follow with Hastelloy and finally MP35N showing the most metal ion leaching when compensating for surface area.
Table 3: Concentration of metal ions leached into acetonitrile among the four different alloys tested. Blank boxes were either not measured or not detected. The final column is adjusted for surface area of the samples that were tested. All values are in ppb.
Alloy
|
Fe
|
Ni
|
Cr
|
Mo
|
Co
|
Ti
|
Total metal per m2
|
Stainless steel
|
19.8
|
12.96
|
---
|
---
|
---
|
---
|
134
|
Titanium
|
---
|
---
|
---
|
---
|
---
|
0.159
|
8
|
Hastelloy
|
3.8
|
554.58
|
0.2
|
0.03
|
0.3
|
---
|
3715
|
MP35N
|
---
|
0.67
|
0.06
|
0.08
|
0.91
|
---
|
14333
|
The results for water can be seen in Figure 3. The total metal concentration is 667 ppb. This is much more than what was leached in both methanol and acetonitrile. A similar pattern was seen for Hastelloy which is also a nickel-based alloy. As was the case for the first two solvents, the coatings were able to block all metal ion leaching into the water.
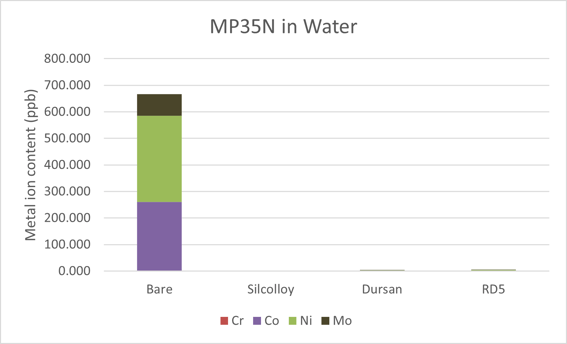
Figure 3: Metal ions leached into deionized water after one month of soak time. The coated samples were all at or near baseline levels of the water in the bottle.
Table 4 shows the comparison between all four alloys soaked in water for one month. The adjusted column for surface area shows just how different the nickel-based alloys are from titanium and stainless steel for this type of trace level corrosion. The MP35N sample, when adjusted for surface area, leaches 0.55% per m2. This amount of leaching is surprisingly high. It is possibly a reason why the sales of high surface area materials, such as frits/sintered filter media, is not currently available.
Table 4: Concentration of metal ions leached into DI water among the four different alloys tested. Blank boxes were either not measured or not detected. The final column is adjusted for surface area of the samples that were tested. All values are in ppb.
Alloy
|
Fe
|
Ni
|
Cr
|
Mo
|
Co
|
Ti
|
Total metal per m2
|
Stainless steel
|
75.1
|
53.62
|
4.34
|
7.7
|
---
|
---
|
574
|
Titanium
|
---
|
---
|
---
|
---
|
---
|
0.58
|
29
|
Hastelloy
|
1.99
|
3881.53
|
3.62
|
1216.41
|
---
|
---
|
33929
|
MP35N
|
---
|
324.5
|
0.49
|
81.44
|
260.44
|
---
|
5557250
|
Conclusion:
MP35N is a corrosion resistant, high strength metal alloy that is commonly used in HPLC and the medical industry for its biocompatibility. Here we see that when adjusted for surface area, it leaches the most metal ions of any alloy tested thus far in methanol, acetonitrile, and water. Also, this is the first alloy that has been tested that leaches appreciable amounts of cobalt into solution.
Tests in our 6 part series have consistently shown that SilcoTek silicon coatings, like Dursan, Silcolloy, and RD5, virtually eliminate contamination from metal ion leaching. Applications for coating components and flow path surfaces include:
- Semiconductor manufacturing
- Biopharmaceutical production
- Medical diagnostics
- Food and beverage processing
- Precision cleaning
- Industrial and process analytical
- Analytical HPLC
Keep abreast of the latest in coating technology, subscribe to our emails and blog, or follow us on LinkedIn.
