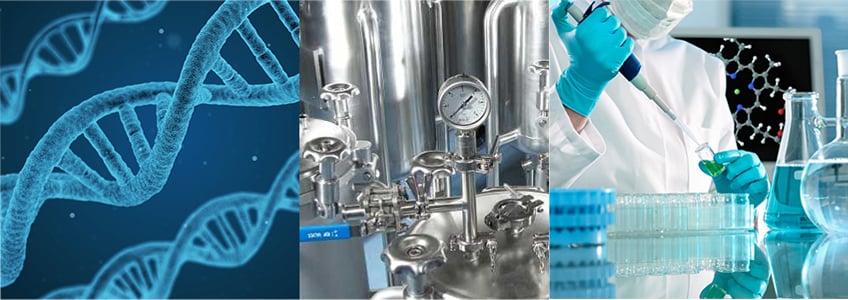
We look into the pitfalls and problems caused by stainless steel rouging in high purity water, WFI, biopharmaceutical, and BPE manufacturing equipment.
In a previous blog post we discussed how our Dursan® coating improves corrosion resistance and rouging of stainless steel surfaces exposed to corrosive environments. In this blog post we'll discuss the impact rouging has on high purity systems, what components can be protected from rouging, and how to prevent rouging in high purity water, water for injection (WFI), biopharmaceutical, and ASME-BPE (Bioprocessing Equipment).
Rouging Causes and Solutions
In this blog post you will learn:
- The causes and solutions to rouging in biopharmaceutical, WFI (Water For Injection), BPE (Bioprocessing Equipment), high purity and process water systems.
- How rouging can impact high purity systems
- How a corrosion resistant and inert coating like Dursan® can reduce or eliminate rouging in high purity water and other water containing systems that exhibit rouging, rouge, or pitting.
|
Background What is Rouging?
Rouging is what is described as red staining (rouge) or black staining on flow path surfaces exposed to corrosive fluids. Rouging can result in a red or black haze on the exposed surface or can exhibit a slimy appearance similar to bio contamination, depending on exposure, and can result in surface pitting of the flow path surface. Corrosion Doctors.org describes rouging as:
"Rouging of stainless steel is the result of the formation of iron oxide, hydroxide or carbonate either from external sources or from destruction of the passive layer. Color variation is a result of the oxide/hydroxide/carbonate type and variations in the water of hydration associated with the corrosion products. These colors range from orange to red to black."
Rouging is a term used in biopharmaceutical manufacturing related applications to describe corrosive attack on flow path surfaces exposed to corrosive streams in water or water based systems. Rouging can be caused by several factors including: the flow path environmental conditions, material quality, fluid pH, duration and frequency of exposure, and the temperature range of the exposed flow path surface.
Rouging can be found in a variety of water systems or water containing systems including pure water, ultra-pure water, steam, treated potable water or untreated process water systems.
What Causes Rouging
*
For the purposes of this blog post we'll discuss the causes of rouging that relate to stainless steel surfaces. With that in mind we'll review some of the causes of rouging in biopharma, high purity water, WFI, and other systems that require high purity and high corrosion resistance.
Rouging can be caused by a range of conditions and materials in treated and untreated water systems or water-based systems including:
Material, equipment, and installation related causes
- The quality of the stainless steel, and the number of non-metallic inclusions in the stainless steel.
- Particulate contamination resulting from system assembly, grinding, welding or cutting particles.
- Metallic defects resulting from improper welding or heating.
- Iron contamination resulting from steel to stainless steel contact.
- Erosion or pump cavitation of stainless steel impellers or high velocity flow paths that result in stainless particulate generation which oxidizes and forms rouge.
Water/process fluid conditions
- For WFI and high purity, and process water systems or water based fluids, the oxygen content and pH of the water can result in corrosive attack and pitting.
- The pH level in WFI high purity water systems can have an effect on metal ions like ferrous and ferric ions found in stainless steel. Ferrous ion leaching can cause the red or black staining found in rouging.
- Metal Ion leaching resulting from deionized or high purity reverse osmosis water can result in surface pitting and rouging effects. Especially heated water which can erode the surface passivation due to less dissolved oxygen. High temperature will also increase iron diffusion rates which can then react with the oxygen in the water to cause iron oxides and hydroxides.
- Chlorine or dissolved oxygen in the process fluid causing oxidation of ferrous bicarbonate resulting in red/brown deposits in untreated water or process water systems.
- Exposure to high temperature, high purity, steam can result in a black surface. In electropolished systems the surface may appear glossy black. For mechanically polished finishes a flat black surface may result.
Cleaning and denaturing agents
- Cleaning agents and protein denaturing agents like guanidine hydrochloride can pit and corrode stainless steel flow paths, resulting in rouging.
- Contamination or corrosion resulting from aggressive cleaning agents or improper cleaning methods.
Impact of Rouging on high purity components
Rouging can contaminate high purity systems which can adulterate products, cause yield problems, increase maintenance, may result in lost product, and can reduce efficiency. Cleaning or restoring the surface to original condition can be time consuming and costly and involves a combination of one or all of the following:
- Acid cleaning, neutralizing and flushing the system.
- Disassembly and re-polishing or electropolishing components or flow paths.
- Mechanical cleaning of the surface.
- Employing chelating agents to remove iron
- Sanitizing or conditioning the surface to approved specifications.
- Testing the system to assure operation and quality is within specifications.
The remediation process for removing rouge and rouging effects may not be realistic for some high purity applications. For some systems, component replacement may be the only option. Because remediation or replacement are costly options, it's worth considering employing methods to prevent rouging from happening in the first place.
How to prevent rouging in WFI, Biopharma, and BPE Systems
Preventing rouging and corrosion in high purity water, and biopharma process systems is preferred to costly component replacement or the associated maintenance and risk of product contamination. Options for preventing rouging range from:
- Selecting materials that are resistant to oxidation and chloride attack.
- Adjusting the pH of the water system to reduce the rouging potential.
- Adding a strong surfactant to the rinse solution to remove chlorides.
- Coating the stainless steel surface with a corrosion resistant and inert barrier coating like Dursan.
Tips for Rouging Prevention
Material selection can also play an important role in reducing rouging. 304 stainless steel (lower nickel content) offers the least rouging protection. 316L offers a measure of improvement but more costly alloys such as alloys C-276 or C 22 (high nickel alloys) offer the highest protection and cost.
Other options relating to materials include increasing the molybdenum and nickel content of the alloy at the surface. Higher molybdenum content will increase the protection against chloride attack.
Electropolishing the stainless steel surface may also offer some limited protection against rouge effects, especially when compared to unpolished or mechanically polished surfaces. Electropolishing will reduce the number of crevices and will smooth the surface, thus reducing areas where high pH fluids can pool and react with the base metal.
Maintaining a system pH above 7 (basic solution) will reduce the potential of rouging by elimination of the acid, even short exposure to pH of less than 7 may increase the chance of rouging. Unfortunately, it may not be realistic to maintain a basic environment given the required process conditions or system fluid specifications.
Adding a surfactant can aid in wetting the surface and improve acid film removal on the surface. However surfactants themselves can leave a film on the surface and result in system contamination.
Of the prevention options listed, coating the surface with a high purity, non-line-of-sight, precision, corrosion resistant coating like Dursan®, is a simple and cost effective way to reduce or eliminate rouging.
Corrosive Attack and Rouging in Analytical and Chemical Processes
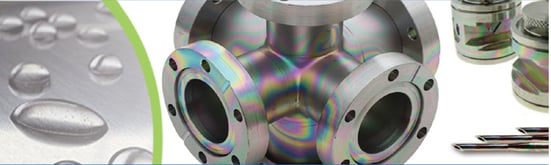
An example of chloride related rouging can be found in common denaturing agents and cleaners like guanidine hydrochloride (sometimes referred to as guanidinium chloride). Guanidine hydrochloride is a powerful protein denaturing agent. It works by disrupting the hydrogen bonding network in water which, in turn, will change the stability of the native state of other molecules that are in the water.
In the biopharmaceutical world, it is often used as a cleaning agent in high concentrations. Concentrations of 6M or higher will cause most proteins to lose their ordered structure and turn into randomly coiled molecules. Unfortunately guanidine hydrochloride also corrodes stainless steel flow paths which can lead to pitting and rouging and promote areas susceptible to carryover and cross contamination in analytical and chemical process applications.
To test the effectiveness of Dursan as a rouging prevention option we compared coated and uncoated 316L stainless steel coupons. When exposed to 6M guanidine hydrochloride, 316L stainless steel showed rouging while Dursan coated coupons were unaffected. You can test the performance of Dursan yourself by ordering free Dursan coated test coupons.
To learn more about how Dursan or other SilcoTek® coatings can improve your process, read our latest Corrosion Solutions Presentation.
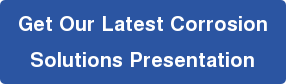
Experiment, Data and Discussion: Preventing Rouging with Dursan - Corrosion Resistant Coatings for Stainless Steel
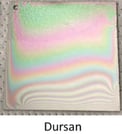
Dursan® coated and bare coupons were immersed in 6M guanidine hydrochloride purchased from BioVision Incorporated. The coupons were evaluated at 1-week and 1-month intervals. Evaluations included:
- Removing the coupons from the solution.
- Rinsing the surface with DI water.
- Sonicating in DI water for 15 minutes.
- Followed by drying in a 230°F oven for an hour.
Corrosion can be quantitatively calculated by the change in mass before and after exposure to the corrosive media. In this study it was found that there was no mass change both after 1 week and 1 month of exposure for coated and uncoated coupons. This shows that guanidine hydrochloride is not nearly as corrosive as other media that SilcoTek® Corporation has tested such as hydrochloric acid, sulfuric acid, or bleach which is another cleaning agent used in the biopharmaceutical industry.
Read more about how SilcoTek coatings can improve corrosion resistance in analytical flow paths.
ASTM G31 immersion testing (below) shows that Dursan significantly reduces corrosion and rouging in common applications found in analytical testing. After immersion in concentrated bleach, the Dursan coupon reduced corrosion by more than an order of magnitude.
/Bleach%20ss%20vs%20dursan.jpg?width=463&name=Bleach%20ss%20vs%20dursan.jpg)
Visually, there was a difference between the coated and the uncoated coupons at the 1-week mark of the experiment as shown in Figure 1. The uncoated coupon on the left shows that there are pockets across the surface that are starting to show oxidation, rust, or rouging. The coupon on the right shows that a Dursan® coated piece of steel does not experience rouging, oxidation, pitting or rust.
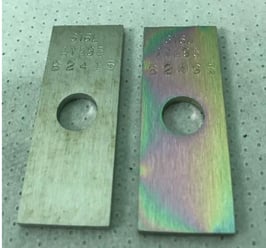
Figure 1: A bare stainless steel coupon (left) and a Dursan coated stainless steel coupon (right) were exposed to guanidine hydrochloride for one week. The bare steel shows minor rusting across all faces of the coupon where the Dursan coated coupon appears to be unaffected.
Since there was no loss of mass for the coupons after the 1-week trial (scale accuracy is 0.1 mg), they were returned to the 6M guanidine hydrochloride solution to soak for 3.5 more weeks (1 month total exposure). Again, there was no change in the mass of the coupons, but the minor rusting and rouging effects were much more dramatic as seen in Figure 2.
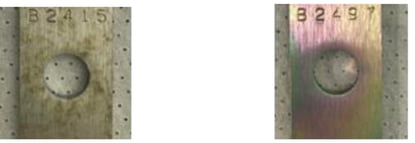
Figure 2: A bare stainless steel coupon (left) and a Dursan coated stainless steel coupon (right) were exposed to guanidine hydrochloride for one month. The rusting on the bare coupon is more severe than the 1-week exposure. As seen previously, the Dursan coated coupon is unaffected by the exposure.
In addition to the increased rouging, there was also a discoloration in the guanidine hydrochloride solution with the uncoated coupon immersed in it for one month. This color change, seen in Figure 3, was not seen at the one-week point of the experiment. The yellow tint to the liquid indicates that iron has leached out of the coupon and into the solution. This is a potential issue for many biopharmaceutical companies, as iron ions can interact with their various drugs and cause impurities and/or low yields.
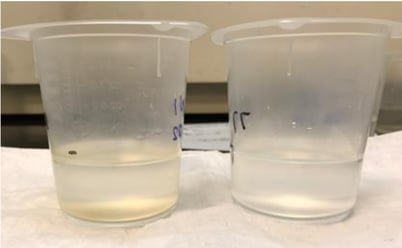
Figure 3: Guanidine hydrochloride solutions after a bare (left) and a Dursan coated (right) coupons were immersed for one month. The yellow tint in the solution that contained the bare coupon is a sign of corrosion, whereas the solution that contained the Dursan coated coupon showed no color change over the immersion period.
What components can be treated to minimize corrosion and rouging?
Dursan® is a precision coating that bonds to stainless steel surfaces resulting in a robust corrosion resistant coating capable of withstanding challenging process conditions such as high process temperatures, extreme pH ranges, aggressive rinse agents and conditions common to biopharma, WFI, and bioprocessing equipment. Dursan does not significantly interfere with tolerances, so existing components can be treated, resulting in significantly improved performance. Treat the entire stainless steel flow path with Dursan to reduce or eliminate rouging, including:
- Pump impellers and housings
- Valves and fittings
- Tubing
- Metal filters and filter housings
- Probes
- Analytical columns and analytical system components
- Sealing hardware
- Reactors or process fluid containers
For a more in-depth listing of what components can be coated, go to our coating list by clicking the box below.
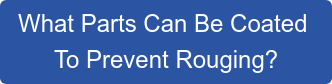
Conclusion:
Water based process fluids, treated and untreated water can cause extensive stainless steel rouging problems in high purity water, WFI, biopharmaceutical, and BPE manufacturing systems. Rouging of stainless steel can damage or contaminate sensitive WFI, biopharma, or other high purity systems. The cost of remediation or prevention of rouging in process systems can high. Rouging can cause performance problems, contamination, and maintenance problems in tubing, valving, and pumps constructed of stainless steel, commonly used in the biopharma industry. The cost due to lost productivity, lost product or product contamination can be higher.
In this blog we discussed the causes and solutions to rouging problems. We highlighted how guanidine hydrochloride (a commonly used cleaning agent in the biopharmaceutical industry) can damage stainless steel flow paths and how Dursan® coated flow paths significantly reduce rouging in stainless steel systems .
Rouging can cause issues in tubing, valving, and pumps constructed of 304 and 316 stainless steel (which is also common in that industry). Utilizing SilcoTek’s Dursan coating process, these issues can be mitigated leading to an increase in yields and a decrease in costs.
Have a question about how SilcoTek® coatings can improve the corrosion resistance of your products? Follow us on LinkedIn or contact our Technical Service Team.

Contributing writers and editors to this blog post: Geoff White, JD, LL.M; Dr. Jesse Bischof
*Image Credit: Corrosion Doctors.org https://corrosion-doctors.org/MatSelect/rouging.htm