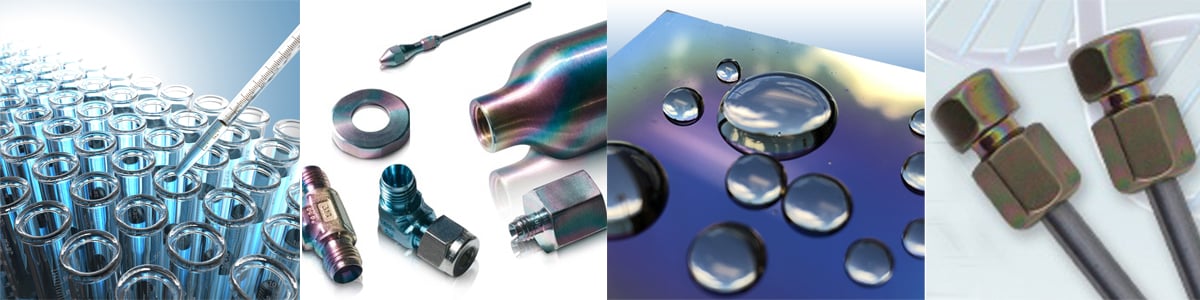
Confused about how to buy and use our coatings? Here are some simple tips to help make improving your products easy!
Tips on Buying and Using SilcoTek Barrier Coatings
In this blog post you will learn:
- What to do and what not to do when sending parts to SilcoTek® for coating service
- How to make the coating process faster and easier
- Where to get a quick reference guide to help you through the coating process
|
The First Steps. About Us, Our Coatings, and Applications
Before making a coating buying decision, you should do some research into the company and it's products. After-all, you're bringing a new vendor into your supply chain and quality system it pays huge dividends to select a company that not only makes your products better but also meets delivery commitments and shares the same high ethical standards. Take these first steps when learning about a coating and coating company:
Learn about who you're dealing with. Research the company, its mission and ethics. For SilcoTek, go to the About Us section of our website to learn about our company mission and core values.
Learn what coatings are offered and the benefits of using a select coating in your application. Go to our Applications page to learn about the benefits our CVD coatings offer in your industry and application.
You can learn about the coatings we offer by going to our Coating Technologies page. Or get our introductory guide SilcoTek 101 to read about our coatings. Not into reading? Watch our quick video (below). It covers all the bases!
You can also consult with our Technical Service Team online to help with a coating selection or address any questions. Want to take a short cut and learn all you need to know about buying CVD coatings?
Watch Our Video to Learn More About Our Coating Service
Digging Deeper, Researching and Testing Our Coatings
Ugh, remember those high school papers? I still remember spending hours looking for information at a place called "The Library". If you enjoyed looking for information at the library you definitely were a nerd. Well now it's easy! And nobody will call you a nerd! Just go to our whitepapers page. There you can click on a drop-down box to see relevant papers and technical insights written by our team of PhD scientists. Can't find what you're looking for? Just click on our "need help finding a whitepaper" button and ask a question. No you won't be asked for a lot of intrusive information we're here to help, not mine for your information. You can try it here.

Customer Strategies: The Coating Purchase Process
We make buying our coatings easy. Want to navigate the purchase process as smoothly as possible and get the best price for a coating? Yep, we wrote a blog on that. We spill all the beans about how to get the best price for coating your parts. Read our blog post How to Get the Best Price for CVD Coatings to learn more.
The process for purchasing coatings is pretty easy but does involve answering some questions. Why the questions? Because providing us with more information when ordering helps to speed up the coating process. We know it's a pain to pull together details about your parts or to complete the online ordering form, but spending a few minutes providing complete information will save us all a lot of time and confusion in the long run. Time spent early in the ordering process is money saved in the long run and goes a long way toward creating a positive customer experience. That's your money saved by the way!
Key information we'll need before treating your part include:
- First we'll need to know how big your part is. Preferably a drawing (especially if the part is a custom or complex piece).
- We'll need to know what coating you want. (see previous blog post on selecting a coating)
- Of course we'll need to know some particulars about you. Your company, address, etc.
- Then we'll want to know some details about the part and proposed use.
- Where do you need the coating?
- What chemicals will the coating be exposed to?
- Can we fixture the part? At what locations?
- Any areas particularly sensitive to damage?
- Any blind holes or intricate passages?
- What's the part made of?
- Can the part be exposed to heat? Up to 400C?
- And finally we'll need to know how many parts you want to coat.
It sounds like a lot of information, if you're not sure about some of the particulars, no worries. Just let us know you're not sure and we'll figure things out on our end. We do ask customers to disassemble parts before shipping. That way you and SilcoTek are sure we're coating the part properly. Want to learn about the in's and out's of our coating process and how to get the most out of your product and grow your sales? Read our e-book.
Manufacturing Capabilities and Support
Before purchasing from a coating vendor, it's good to know if the supplier has the capacity and quality systems in place to enable fast and high quality coating service. SilcoTek's 70,000 square foot manufacturing facility offers the flexibility and capacity to coat many different size parts on an industrial scale. From large to small, short to long, we're able to coat many different form factors including:
Overall part size:
- Largest overall part size: 2.032m x .76m ID (80in x 29.92in)
- Smallest part size: Approximately 1mm. Call us to discuss.
|
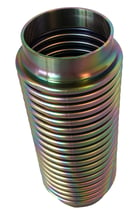 |
Tubing sizes:
SilcoTek offers two processes for coating tubes:
- Coat straight tubes up to 2 meters long.
- Coiled/Rolled Tubing
- Coated internally-only
- Maximum continuous length: 1000 to 2500 ft
|
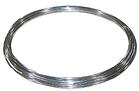 |
Go to our Frequently Asked Questions page to learn more about coating capabilities.Have a question about bending tubing? Here's a quick guide on bending SilcoTek coated tubing.

Product Support and Building Relationships
Have questions about our coatings, coating performance, or use in your application? Our Technical Service Team is here to help. Contact us to discuss any questions you have about our coatings.
Go to our Terms and Conditions page to learn about warranty and product support throughout the purchasing process and use of the coating. Want to get the most out of our coatings? Get our Coating Care Guide to learn about how to get the most out of our coatings.
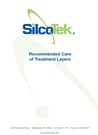
Placing follow on orders
Placing follow-on orders is easy. For high volume users all the hard work is done! Just contact us and let us know what coating part number and quantity of parts to be coated and we'll do the rest! And don't hesitate to get in touch if you have a question about researching or ordering the right coating for your application.
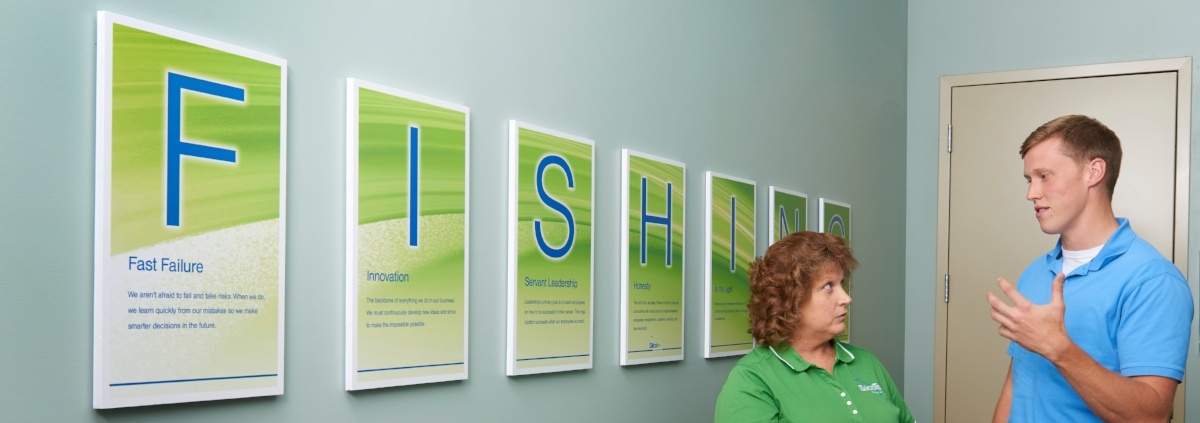