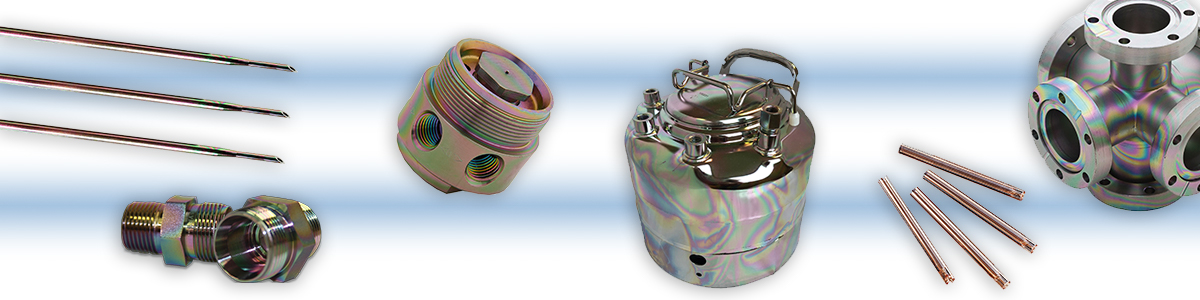
SilcoTek® offers custom silicon CVD coatings for analytical, semiconductor, energy, and other applications. But how custom are CVD coatings? Let's find out.
How Custom are Silicon CVD Coatings?
If you look on our website you'll see a list of chemical vapor deposition (CVD) coatings offered for various applications they include:
A tough, corrosion resistant, inert, hydrophobic coating. Ideal for oil and gas, chemical processing, refining, and other demanding environments.
The original, most inert and chemically compatible coating available on the market. A required coating when analyzing low levels of active, reactive, organo-sulfur, and many more active compounds.
A corrosion and oxidation resistant coating that increases the lifetime of system components and prevents metal ion contamination.
A non-stick coating specifically designed to reduce the onset of carbon coking and fouling on stainless steel at high temperature.
A low outgassing, rapid pump down, high purity coating designed to improve performance in ultra high vacuum, mass spec, and semiconductor systems.
An inert corrosion resistant silicon barrier coating formulated especially for high purity processes.
Improves surface repelling properties to resist unwanted build-up of water, oils, sticky hydrocarbons, and other foulants.
So it looks like we offer 7 coatings is that really custom? Well that's not the whole story. In fact we offer over 30 coating variants and the list keeps growing. In this blog post we'll discuss customization of coatings for your application.
In this blog post you will learn:
- How SilcoTek® customizes our coatings for your application.
- Learn how our coating technology allows for customization and learn how innovative ways to change the performance of our coatings.
- Learn about the customization process.
|
Our Technology and Customization
The silicon chemical vapor deposition technology employed by SilcoTek allows various compounds to be applied to the surface or as a primer layer to improve thermal or other performance properties of the primary coating. Below is a Auger plot of a silicon coating. The you can see the body of the coating (purple line) is silicon.
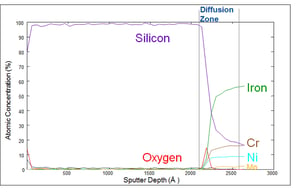
To enhance the performance of the coating the very top layer of the silicon coating or the body of the coating can be changed by bonding select compounds to the silicon, as seen below.
Another customization option may involve bonding a primer layer to the substrate to act as a barrier between the silicon coating and the substrate. The purpose of the primer is to improve overall material compatibility and to prevent catalytic action between the coating and substrate.
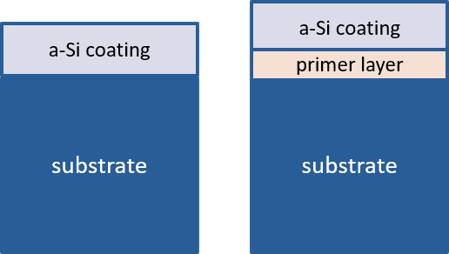
The coating method also plays a part in an effective coating process. We use chemical vapor deposition (CVD) because we're able to coat all areas of a part, including blind holes tubing or shadowed areas. Contrast CVD with physical vapor deposition (PVD) where only line of site areas are coated.
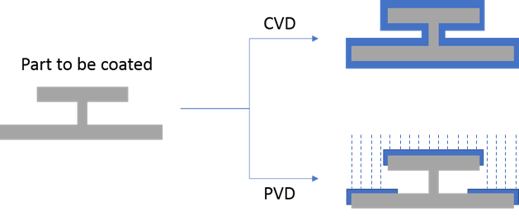
Customize for Your Application
The idea of offering variants to our basic coating selection developed over a period of 10 years. As we developed better and better coatings, customers found more challenging applications. Our R&D team began to develop a virtuous cycle where coating materials, surface modification options, and primer layer options allowed us to mix and match coating options to meet customer requirements. How does that process work? Let's discuss.

A custom coating solution starts with the customer and their performance needs. We encourage customers to contact SilcoTek Technical Service with application and performance requirements. We're often able to suggest one of our standard coatings and successfully meet the coating requirements. If we feel that a standard coating won't meet the need, we'll recommend one of the many custom options. Factors that can result in a customized coating include:
- A challenging part form factor. This may include a very narrow bore (found in needles), micro etching or fine channels, or surface modifications.
- A challenging environment. For example the part may be exposed to very high temperatures that can result in catalytic interactions with the coating.
- A new performance need. The part may need to have a hydrophobic surface or higher inertness.
- A difficult material application. Some materials may promote catalytic interference with the coating during processing, resulting in a marginal coating. Materials like monel, titanium, or aluminum may require special processing. Improved inertness and corrosion resistance for aluminum or other materials may require customization.
The customization process
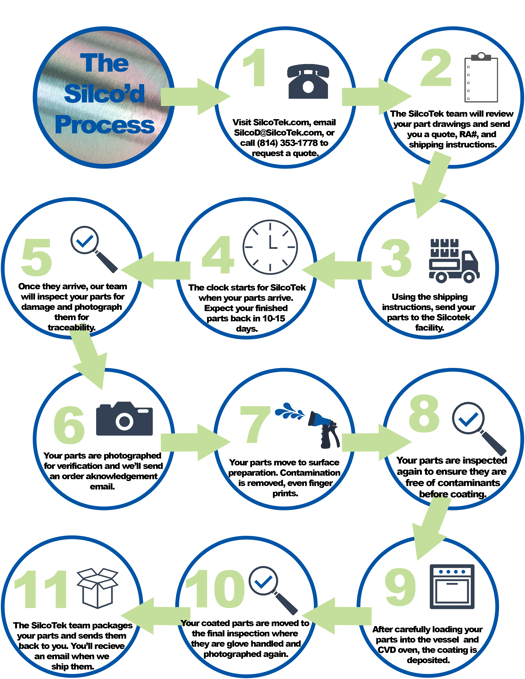
How will a potential buyer know if they need to customize a part? That's where we come in. After an initial consultation, the customer may request a coating to test, or they may give us a specification. Our Technical Service Team will suggest a coating for evaluation. As stated previously usually one of our standard coatings will meet the need.
A Customer may test the standard coating with some success but they may need better performance. Alternatively, our Technical Service Team may customize a coating to fit material or part form factor needs as part of our normal production evaluation process.
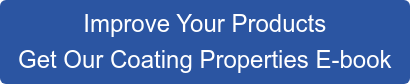
If the coating performance falls short, SilcoTek® R&D consults with the customer and goes to work. The team will modify the coating formulation or process as needed. SilcoTek and the customer will evaluate the revised coating to meet the desired specification.
Summary
SilcoTek offers many more coating options than those listed on our website, our Technology Team is often able to customize a cost effective coating solution that meets your needs. If your current material or coating is not performing to your specification, let us know. We'll work with you to find a solution.
Stay connected to the latest in coating development. Subscribe to our blog and email or follow us on LinkedIn.
